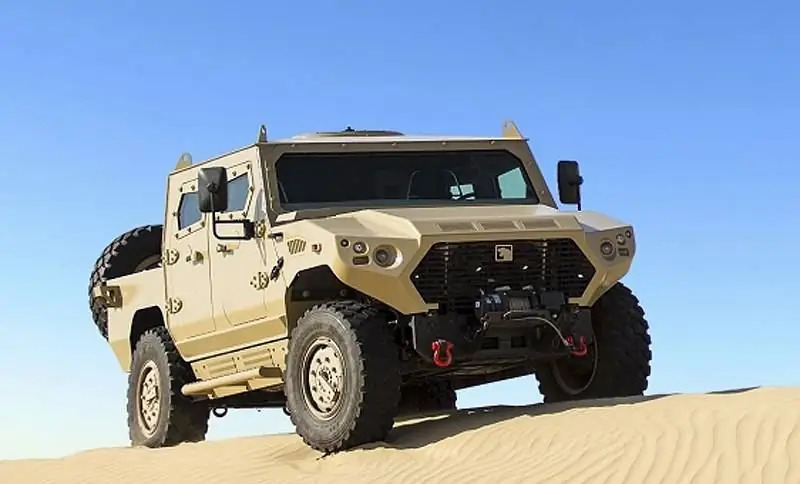
L'armure a des millions d'années de plus que l'humanité, et elle s'est développée principalement pour protéger contre les mâchoires et les griffes. Il est possible que les crocodiles et les tortues puissent en partie inspirer les humains à créer des éléments protecteurs. Toutes les armes à énergie cinétique, qu'il s'agisse d'une massue préhistorique ou d'un projectile perforant, sont conçues pour concentrer une grande force dans une petite zone, sa tâche est de pénétrer la cible et de lui infliger un maximum de dégâts. Par conséquent, le rôle du blindage est d'empêcher cela en déviant ou en détruisant les moyens d'attaque et/ou en dispersant l'énergie d'impact sur une surface la plus large possible afin de minimiser les dommages aux hommes, aux systèmes de transport et aux structures qu'il protège.
L'armure moderne se compose généralement d'une couche externe dure pour arrêter, dévier ou détruire le projectile, une couche intermédiaire avec un « travail de rupture » très élevé et une couche interne visqueuse pour éviter les fissures et les débris.
Acier
L'acier, qui est devenu le premier matériau largement utilisé dans la création de véhicules blindés, est toujours en demande, malgré l'émergence de blindages à base d'alliages légers d'aluminium et de titane, de céramiques, de composites à matrice polymère, renforcés de fibres de verre, d'aramide et le polyéthylène à ultra haut poids moléculaire, ainsi que les matériaux composites à matrice métallique.
De nombreuses aciéries, y compris SSAB, continuent de développer des aciers à haute résistance pour une variété d'applications critiques en termes de poids, telles que le gainage supplémentaire. La nuance d'acier blindé ARM OX 600T, disponible dans des épaisseurs de 4 à 20 mm, est disponible avec une dureté garantie de 570 à 640 unités HBW (abréviation de Hardness, Brinell, Wolfram; un test dans lequel une bille de tungstène d'un diamètre standard est pressée dans un échantillon de matériau avec une force connue, puis le diamètre de l'évidement formé est mesuré; puis ces paramètres sont substitués dans la formule, ce qui permet d'obtenir le nombre d'unités de dureté).
SSAB souligne également l'importance d'atteindre le bon équilibre entre dureté et ténacité pour la pénétration et la protection contre l'éclatement. Comme tous les aciers, ARMOX 600T est composé de fer, de carbone et d'un certain nombre d'autres composants d'alliage, notamment du silicium, du manganèse, du phosphore, du soufre, du chrome, du nickel, du molybdène et du bore.
Il existe des limitations sur les techniques de fabrication utilisées, notamment en ce qui concerne la température. Cet acier n'est pas destiné à un traitement thermique supplémentaire; s'il est chauffé à plus de 170°C après livraison, SSAB ne peut garantir ses propriétés. Les entreprises qui peuvent contourner ce type de restriction sont susceptibles d'attirer l'attention des fabricants de véhicules blindés.
Une autre société suédoise, Deform, propose des pièces moulées à chaud en acier blindé résistant aux balles aux fabricants de véhicules blindés, en particulier à ceux qui cherchent à améliorer la protection des véhicules commerciaux/civils.
Des pare-feu monoblocs Deform sont installés dans le Nissan PATROL 4x4, le minibus Volkswagen T6 TRANSPORTER et la camionnette Isuzu D-MAX, ainsi qu'une feuille de sol solide du même matériau. Le procédé de formage à chaud développé par Deform et utilisé dans la production de tôles maintient une dureté de 600HB [HBW].
La société affirme qu'elle peut restaurer les propriétés de tous les aciers de blindage sur le marché tout en conservant une forme structurellement définie, tandis que les pièces résultantes sont de loin supérieures aux structures traditionnelles soudées et partiellement superposées. Dans la méthode développée par Deform, les tôles sont trempées et revenus après forgeage à chaud. Grâce à ce procédé, il est possible d'obtenir des formes tridimensionnelles qui ne peuvent être obtenues par formage à froid sans l'obligatoire dans de tels cas "des soudures qui violent l'intégrité des points critiques".
Les tôles d'acier déformées à chaud ont été utilisées sur BAE Systems BVS-10 et CV90 et, depuis le début des années 1990, sur de nombreuses machines Kraus-Maffei Wegmann (KMW). Des commandes arrivent pour la production de plaques de blindage tridimensionnelles pour le char LEOPARD 2 et de plusieurs plaques profilées pour les véhicules BOXER et PUMA, ainsi que pour plusieurs véhicules Rheinmetall, dont à nouveau le BOXER, ainsi qu'une trappe pour le véhicule WIESEL. Deform fonctionne également avec d'autres matériaux de protection, notamment l'aluminium, le kevlar/aramide et le titane.
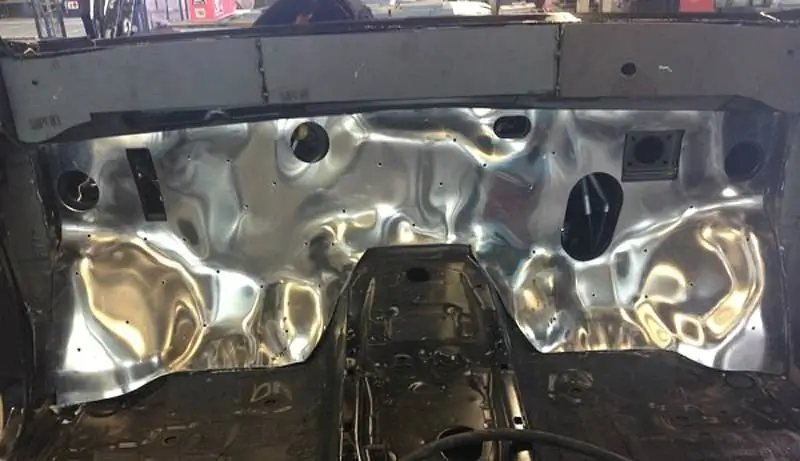
Progrès de l'aluminium
En ce qui concerne les véhicules blindés, pour la première fois, un blindage en aluminium a été largement utilisé dans la fabrication du véhicule blindé de transport de troupes M113, produit depuis 1960. C'était un alliage, désigné 5083, contenant 4,5% de magnésium et des quantités beaucoup plus faibles de manganèse, fer, cuivre, carbone, zinc, chrome, titane et autres. Bien que le 5083 conserve bien sa résistance après le soudage, ce n'est pas un alliage pouvant être traité thermiquement. Il n'a pas une aussi bonne résistance aux balles perforantes de 7,62 mm, mais, comme les tests officiels l'ont confirmé, il arrête mieux les balles perforantes de style soviétique de 14,5 mm que l'acier, tout en économisant du poids et en ajoutant la résistance souhaitée. Pour ce niveau de protection, la tôle d'aluminium est plus épaisse et 9 fois plus résistante que l'acier avec une densité plus faible de 265 r/cm3, ce qui se traduit par une réduction du poids de la structure.
Les fabricants de véhicules blindés ont rapidement commencé à demander des blindages en aluminium plus légers, plus résistants sur le plan balistique, soudables et pouvant être traités thermiquement, ce qui a conduit au développement d'Alcan du 7039 et plus tard du 7017, tous deux avec une teneur en zinc plus élevée.
Comme pour l'acier, l'emboutissage et l'assemblage ultérieur peuvent affecter négativement les propriétés protectrices de l'aluminium. Lors du soudage, les zones affectées thermiquement se ramollissent, mais leur résistance est partiellement restaurée en raison du durcissement lors du vieillissement naturel. La structure du métal évolue dans des zones étroites à proximité de la soudure, créant d'importantes contraintes résiduelles en cas d'erreurs de soudage et/ou d'assemblage. Par conséquent, les techniques de fabrication doivent les minimiser, tandis que le risque de fissuration par corrosion sous contrainte doit également être minimisé, en particulier lorsque la durée de vie de la machine est estimée à plus de trois décennies.
La fissuration par corrosion sous contrainte est un processus d'apparition et de croissance de fissures dans un environnement corrosif, qui a tendance à se détériorer à mesure que le nombre d'éléments d'alliage augmente. La formation de fissures et leur croissance ultérieure se produisent à la suite de la diffusion d'hydrogène le long des joints de grains.
La détermination de la susceptibilité à la fissuration commence par l'extraction d'une petite quantité d'électrolyte des fissures et son analyse. Des tests de corrosion sous contrainte à faible vitesse de déformation sont effectués pour déterminer à quel point un alliage particulier a été endommagé. L'étirement mécanique de deux échantillons (l'un dans un environnement corrosif et l'autre dans l'air sec) se produit jusqu'à ce qu'ils échouent, puis la déformation plastique au site de fracture est comparée - plus l'échantillon est étiré jusqu'à la rupture, mieux c'est.
La résistance à la fissuration par corrosion sous contrainte peut être améliorée pendant le traitement. Par exemple, selon Total Materia, qui s'autoproclame « la plus grande base de données de matériaux au monde », Alcan a amélioré de 40 fois les performances du 7017 dans les tests de fissuration par corrosion sous contrainte accélérée. Les résultats obtenus permettent également de développer des méthodes de protection contre la corrosion pour les zones de structures soudées, dans lesquelles il est difficile d'éviter les contraintes résiduelles. Des recherches visant à améliorer les alliages afin d'optimiser les caractéristiques électrochimiques des joints soudés sont en cours. Les travaux sur les nouveaux alliages traitables thermiquement se concentrent sur l'amélioration de leur résistance mécanique et de leur résistance à la corrosion, tandis que les travaux sur les alliages non traitables thermiquement visent à lever les contraintes imposées par les exigences de soudabilité. Les matériaux les plus résistants en développement seront 50 % plus résistants que les meilleures armures en aluminium utilisées aujourd'hui.
Les alliages à faible densité tels que l'aluminium au lithium offrent une économie de poids d'environ 10 % par rapport aux alliages précédents avec une résistance aux balles comparable, bien que les performances balistiques n'aient pas encore été entièrement évaluées selon Total Materia.
Les méthodes de soudage, y compris robotiques, s'améliorent également. Parmi les tâches à résoudre figurent la minimisation de l'apport de chaleur, un arc de soudage plus stable grâce à l'amélioration des systèmes d'alimentation en énergie et en fil, ainsi que la surveillance et le contrôle du processus par des systèmes experts.
MTL Advanced Materials a travaillé avec ALCOA Defence, un fabricant renommé de plaques de blindage en aluminium, pour développer ce que l'entreprise décrit comme un « processus de formage à froid fiable et reproductible ». La société note que les alliages d'aluminium développés pour les applications de blindage n'ont pas été conçus pour le formage à froid, ce qui signifie que son nouveau processus devrait aider à éviter les modes de défaillance courants, notamment la fissuration. L'objectif ultime est de permettre aux concepteurs de machines de minimiser le besoin de soudage et de réduire le nombre de pièces, selon l'entreprise. La réduction du volume de soudage, souligne la société, augmente la résistance structurelle et la protection de l'équipe tout en réduisant les coûts de production. En commençant par l'alliage 5083-H131 qui a fait ses preuves, l'entreprise a développé un procédé de formage à froid de pièces avec un angle de pliage de 90 degrés le long et à travers les grains, puis est passé à des matériaux plus complexes, par exemple les alliages 7017, 7020 et 7085., obtenant également de bons résultats.
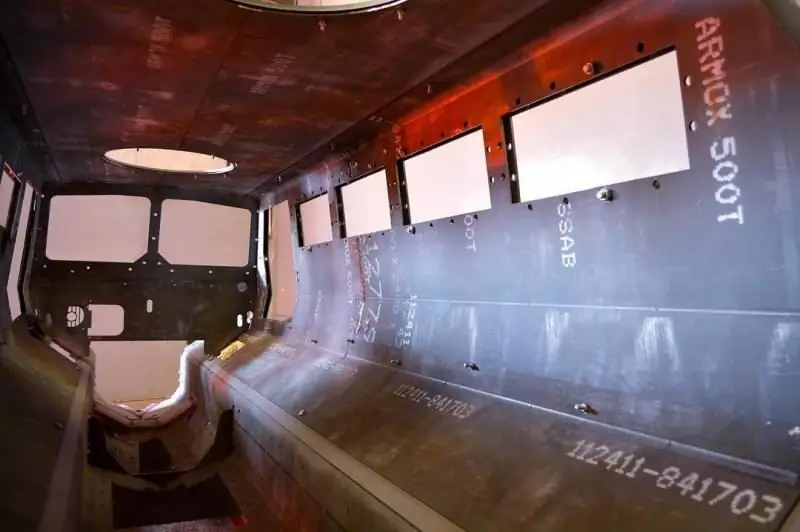
Céramiques et composites
Il y a plusieurs années, Morgan Advanced Materials a annoncé le développement de plusieurs systèmes de blindage SAMAS, qui consistaient en une combinaison de céramiques avancées et de composites structuraux. La gamme de produits comprend des blindages articulés, des revêtements anti-fragmentation, des capsules de survie en composites structurels pour remplacer les coques métalliques et protéger les modules d'armes, à la fois habités et inhabités. Tous peuvent être adaptés à des besoins spécifiques ou fabriqués sur commande.
Fournit une protection STANAG 4569 de niveau 2 à 6, ainsi que des performances multi-impacts et des économies de poids (la société affirme que ces systèmes pèsent deux fois moins que des produits en acier similaires) et s'adaptent à des menaces, plates-formes et missions spécifiques. … Les revêtements anti-éclats peuvent être réalisés à partir de panneaux plats pesant 12,3 kg pour couvrir une surface de 0,36 m2 (environ 34 kg/m2) ou de ferrures solides pesant 12,8 kg pour 0,55 m2 (environ 23,2 kg/m2).
Selon Morgan Advanced Materials, un blindage supplémentaire conçu pour les nouvelles plates-formes et la modernisation des plates-formes existantes offre les mêmes capacités à la moitié du poids. Le système breveté offre une protection maximale contre un large éventail de menaces, y compris les armes de petit et moyen calibre, les engins explosifs improvisés (EEI) et les grenades propulsées par fusée, ainsi que des performances multi-impacts.
Un système de blindage "semi-structural" avec une bonne résistance à la corrosion est proposé pour les modules d'armes (en plus des applications aériennes et maritimes), et en plus d'économiser du poids et de minimiser les problèmes de centre de gravité, contrairement à l'acier, il crée moins de problèmes de compatibilité électromagnétique.
La protection des modules d'armes est un problème particulier, car ils constituent une cible attrayante, car leur mise hors service altère drastiquement la maîtrise de la situation par l'équipage et la capacité du véhicule à faire face aux menaces proches. Ils ont également une optoélectronique délicate et des moteurs électriques vulnérables. Comme ils sont généralement installés au sommet du véhicule, le blindage doit être léger afin de maintenir le centre de gravité aussi bas que possible.
Le système de protection des modules d'armes, qui peut inclure des vitres blindées et une protection de la partie supérieure, est complètement repliable, deux personnes peuvent le remonter en 90 secondes. Les capsules composites de survie sont fabriquées à partir de ce que la société décrit comme « des matériaux résistants et des formulations polymères uniques », elles offrent une protection contre les éclats d'obus et peuvent être réparées sur le terrain.
Protection du soldat
Le SPS (Soldier Protection System) développé par 3M Ceradyne comprend des casques et des inserts dans les gilets pare-balles pour les composants Integrated Head Protection System (IHPS) et VTP (Vital Torso Protection) - ESAPI (Enhanced Small Arms Protective Insert) - insert amélioré pour la protection contre armes légères) du système SPS.
Les exigences de l'IHPS incluent un poids plus léger, une protection auditive passive et une meilleure protection contre les chocs contondants. Le système comprend également des accessoires tels qu'un composant pour protéger la mâchoire inférieure d'un soldat, une visière de protection, un support pour lunettes de vision nocturne, des guides pour, par exemple, une lampe de poche et un appareil photo, et une protection modulaire supplémentaire contre les balles. Le contrat, d'une valeur de plus de 7 millions de dollars, prévoit la fourniture d'environ 5 300 casques. En attendant, plus de 30 000 kits ESAPI - des inserts plus légers pour gilets pare-balles - seront livrés dans le cadre du contrat de 36 millions de dollars. La production de ces deux kits a commencé en 2017.
Toujours dans le cadre du programme SPS, KDH Defence a sélectionné les matériaux SPECTRA SHIELD et GOLD SHIELD de Honeywell pour cinq sous-systèmes, y compris le sous-système de protection du torse et des extrémités (TEP) à fournir pour le projet SPS. Le système de protection TEP est 26% plus léger, ce qui réduit finalement le poids du système SPS de 10%. KDH utilisera le SPECTRA SHIELD, basé sur la fibre UHMWPE, et le GOLD SHIELD, basé sur les fibres d'aramide, dans ses propres produits pour ce système.
Fibre SPECTRA
Honeywell utilise un procédé exclusif de filage et d'étirage de fibres polymères pour incorporer la matière première UHMWPE dans la fibre SPECTRA. Ce matériau est 10 fois plus résistant que l'acier en termes de poids, sa résistance spécifique est 40% supérieure à celle de la fibre aramide, il a un point de fusion plus élevé que le polyéthylène standard (150°C) et une plus grande résistance à l'usure par rapport aux autres polymères, par exemple, le polyester.
Le matériau SPECTRA solide et rigide présente une forte déformation à la rupture, c'est-à-dire qu'il s'étire très fortement avant de se rompre; cette propriété permet d'absorber une grande quantité d'énergie d'impact. Honeywell affirme que les composites de fibres SPECTRA fonctionnent très bien sous les impacts à grande vitesse tels que les balles de fusil et les ondes de choc. Selon l'entreprise, « notre fibre avancée réagit à l'impact en éliminant rapidement l'énergie cinétique de la zone d'impact…, de l'eau et de la lumière UV."
Dans sa technologie SHIELD, Honeywell étale des brins de fibres parallèles et les lie ensemble en les imprégnant d'une résine avancée pour créer un ruban unidirectionnel. Ensuite, les couches de ce ruban sont placées en croix aux angles souhaités et à une température et une pression données, soudées en une structure composite. Pour les applications portables douces, il est laminé entre deux couches de film transparent mince et flexible. Parce que les fibres restent droites et parallèles, elles dissipent l'énergie d'impact plus efficacement que si elles étaient tissées dans un tissu tissé.
Short Bark Industries utilise également SPECTRA SHIELD dans le garde du corps BCS (Ballistic Combat Shirt) pour le système SPS TEP. Short Bark est spécialisé dans la protection souple, les vêtements tactiques et les accessoires.
Selon Honeywell, les soldats ont choisi des éléments de protection fabriqués à partir de ces matériaux après avoir démontré des performances supérieures par rapport à leurs homologues en fibre d'aramide.