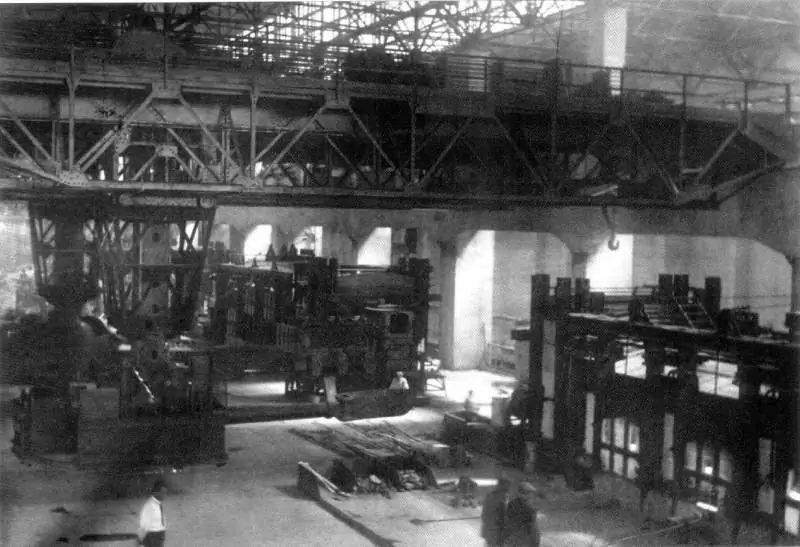
Ressource stratégique
Il est difficile de surestimer la production d'acier de haute qualité pour le complexe militaro-industriel dans des conditions de guerre. C'est l'un des facteurs les plus importants du succès des armées sur le champ de bataille.
Comme vous le savez, les métallurgistes de Krupp ont été parmi les premiers à apprendre à produire de l'acier de qualité militaire de haute qualité.
Les Allemands ont adopté le procédé de fabrication Thomas à la fin du 19ème siècle. Cette méthode de fusion de l'acier permettait d'éliminer les impuretés phosphorées du minerai, ce qui augmentait automatiquement la qualité du produit. L'acier d'armure et d'armes de haute qualité pendant la Première Guerre mondiale a souvent assuré la supériorité des Allemands sur le champ de bataille.
Pour organiser une telle production, de nouveaux matériaux réfractaires étaient nécessaires, qui tapissaient les surfaces intérieures des fours. Les Allemands utilisaient les derniers réfractaires de magnésite pour leur époque, résistant à des températures de plus de 2000 degrés. Ces substances plus réfractaires sont à base d'oxydes de magnésium avec de petits mélanges d'oxydes d'aluminium.
Au début du XXe siècle, les pays dotés de technologies de production de masse de réfractaires de magnésite pouvaient se permettre de produire des blindages et des canons d'armes à feu de haute qualité. Cela peut être comparé à un avantage stratégique.
Plus faibles en termes de résistance au feu étaient les matériaux dits hautement réfractaires qui résistent à des températures de 1750 à 1950 degrés. Ce sont des réfractaires à base de dolomie et à haute teneur en alumine. Les matériaux réfractaires en argile réfractaire, semi-acide, quartz et dinas peuvent résister à des températures de 1610 à 1750 degrés.
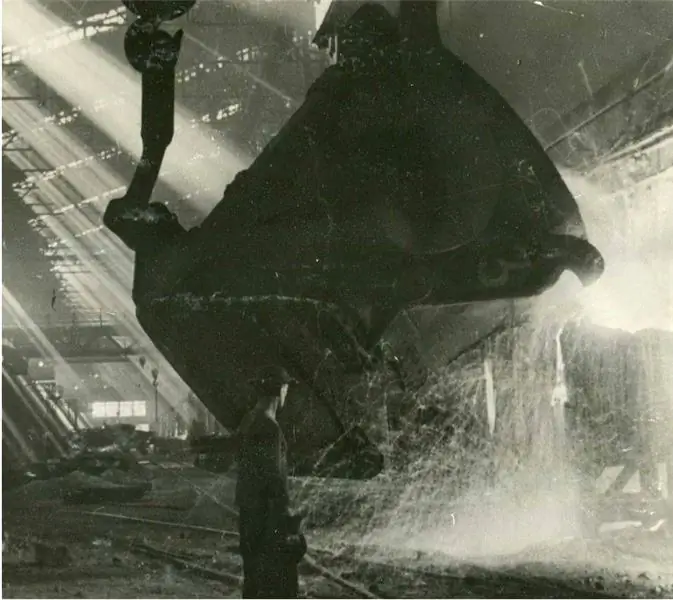
Soit dit en passant, les technologies et les sites de production de réfractaires de magnésite sont apparus pour la première fois en Russie en 1900.
La brique réfractaire de magnésite Satka en 1905 a reçu une médaille d'or à l'Exposition industrielle mondiale de Liège. Il a été produit près de Chelyabinsk dans la ville de Satka, où se trouvait un gisement de magnésite unique.
Le minéral périclase, à partir duquel les réfractaires étaient fabriqués en usine, était de haute qualité et ne nécessitait pas d'enrichissement supplémentaire. En conséquence, le réfractaire de magnésite de Satka était supérieur à ses homologues de Grèce et d'Autriche.
Combler le fossé
Malgré la brique de magnésite de Satka de très haute qualité, jusque dans les années 30, les principaux réfractaires des métallurgistes soviétiques étaient des matériaux dinas à base d'argile. Naturellement, l'obtention d'une température élevée pour la fusion de l'acier de qualité militaire n'a pas fonctionné - le revêtement intérieur des fours à foyer ouvert s'est effondré et a nécessité des réparations extraordinaires.
Il n'y avait pas assez de brique Satka et dans la période post-révolutionnaire, les principales technologies de production ont été perdues.
Dans le même temps, les Européens sont allés de l'avant - par exemple, la magnésite autrichienne Radex se distinguait par une excellente résistance au feu.
L'Union soviétique a acheté ce matériel. Mais il était impossible d'obtenir un analogue sans un secret de production. Ce problème a été abordé par un diplômé de l'Université technique d'État de Moscou. N. E. Bauman Alexeï Petrovitch Panarine. À l'usine Magnet (anciennement la moissonneuse-batteuse Satka) en 1933, il dirige le laboratoire central de l'usine. Et cinq ans plus tard, il lance la production en série de réfractaires périclase-chromite ou chromomagnésite pour fours à sole.
À l'usine métallurgique de Zlatoust et au marteau et à la faucille de Moscou, le réfractaire de Panarin a remplacé les dinas obsolètes.
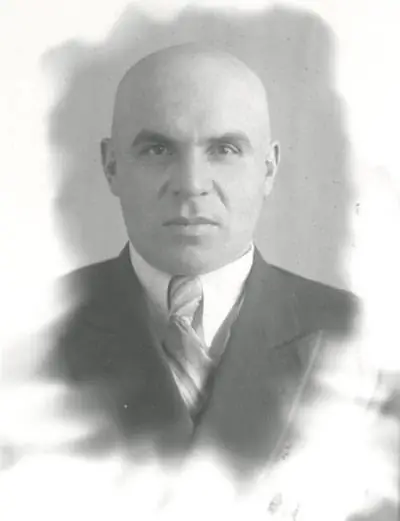
La technologie, qui avait été développée dans le laboratoire de "Magnezit" pendant plusieurs années, consistait en une composition et une granulométrie spéciales.
Auparavant, l'usine produisait des briques conventionnelles en chrome-magnésite, composées de magnésite et de minerai de fer au chrome, dans un rapport 50/50. Le secret révélé par le groupe de Panarin était le suivant:
«Si du minerai de chromite en gros grains granulométriques avec une teneur minimale en fractions inférieure à 0,5 mm est ajouté à une charge de magnésite ordinaire, alors même avec un ajout de 10% de ce minerai, la stabilité thermique de la brique augmente fortement.
Au fur et à mesure que l'ajout de minerai de chromite de granulométrie grossière augmente, la stabilité de la brique augmente et atteint un maximum à un certain rapport de composants. »
La chromite destinée au nouveau réfractaire a été prélevée à la mine de Saranovskoïe et la périclase a continué à être extraite à Satka.
À titre de comparaison, une brique de magnésite "pré-révolutionnaire" ordinaire a résisté à des températures 5 à 6 fois inférieures à la nouveauté de Panarin.
À la fonderie de cuivre de Kirovograd, le réfractaire au chrome-magnésite dans le toit d'un four à réverbère a résisté à des températures allant jusqu'à 1550 degrés pendant 151 jours. Auparavant, les réfractaires de ces fours devaient être changés tous les 20 à 30 jours.
En 1941, la production de réfractaires à grande échelle était maîtrisée, ce qui permettait d'utiliser les matériaux dans de grands fours sidérurgiques à des températures allant jusqu'à 1800 degrés. Une contribution importante à cela a été apportée par le directeur technique de "Magnezit" Alexander Frenkel, qui a développé une nouvelle méthode de fixation du matériau réfractaire aux toits des fours.
Réfractaires pour la victoire
À la fin de 1941, les métallurgistes de Magnitka ont accompli l'impensable auparavant - pour la première fois dans l'histoire, ils ont maîtrisé la fonte de l'acier de blindage pour les chars T-34 dans les principaux fours lourds à foyer ouvert.
Le principal fournisseur de réfractaires pour un processus aussi important était Satka "Magnezit". Il est inutile de parler des difficultés de la guerre, lorsqu'un tiers des ouvriers d'usine ont été appelés au front et que l'État a exigé que le plan soit dépassé. Néanmoins, l'usine faisait son travail, et Panarin en 1943
"Pour maîtriser la fabrication de produits hautement réfractaires à partir de matières premières locales pour la métallurgie ferreuse"
a reçu le prix Staline.
En 1944, ce métallurgiste-chercheur développera une technologie de production de poudre de magnésite de haute qualité "Extra". Ce produit semi-fini était utilisé pour préparer un réfractaire pressé utilisé dans la production particulièrement importante d'acier blindé dans les fours électriques. La limite de température pour ces réfractaires a atteint 2000 degrés.
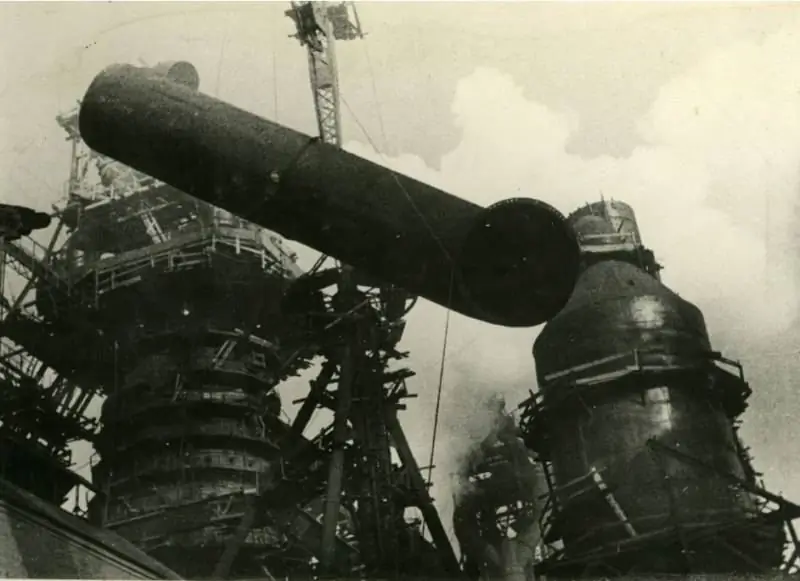
Mais il ne faut pas supposer que l'exemple d'une usine de Magnezit généralement réussie s'étend à l'ensemble de l'industrie réfractaire de l'Union soviétique.
Une situation particulièrement difficile se développa dans l'Oural, où pratiquement tout le bâtiment de chars du pays fut évacué en 1941-1942.
Les usines métallurgiques de Magnitogorsk et de Novotagilsk ont été réorientées vers la production d'armures, fournissant des produits à Sverdlovsk Uralmash, Chelyabinsk "Tankograd" et l'usine de réservoirs de Nijni Tagil n ° 183. Dans le même temps, les usines métallurgiques avaient leur propre production de réfractaires à partir de matières premières locales.
Par exemple, à Magnitka, l'usine de dinas-chamotte produisait 65 à 70 000 tonnes de briques par an. Cela ne suffisait même pas à leurs propres besoins, sans parler de l'approvisionnement d'autres entreprises.
Les premières difficultés sont survenues lorsque les usines de réservoirs ont commencé à construire leurs propres fours de chauffage et thermiques. La métallurgie de l'Oural avait déjà à peine assez de réfractaires, puis la production de coques d'usines de réservoirs nécessitait des matériaux de haute qualité pour le revêtement des fours.
On ne parlait pas ici de réfractaires à la chromomagnésite - ce matériau était rare et même exporté en échange du prêt-bail américain. Au moins, cela est mentionné dans un certain nombre de sources. Les historiens de l'Oural écrivent que la chromomagnésite coûteuse de Panarin pourrait aller à l'étranger en échange de ferroalliages rares pour le blindage des chars. Mais il n'y a pas encore de preuve directe de cela.
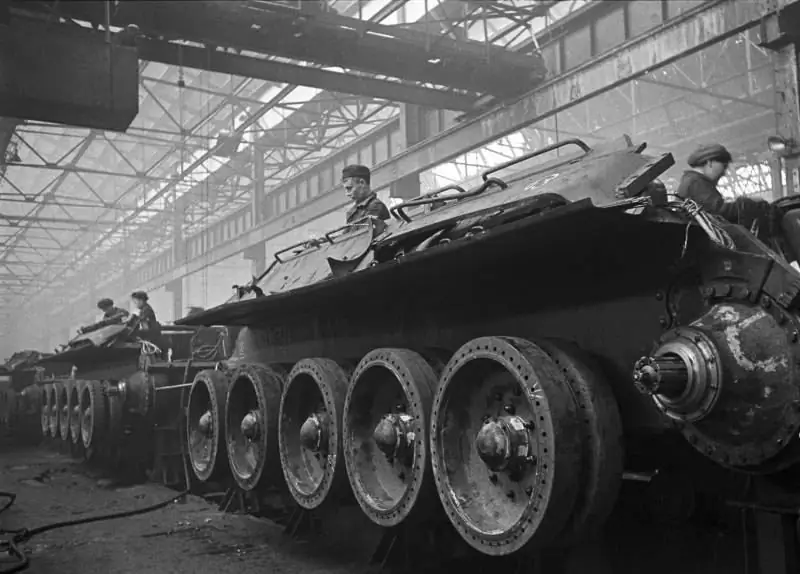
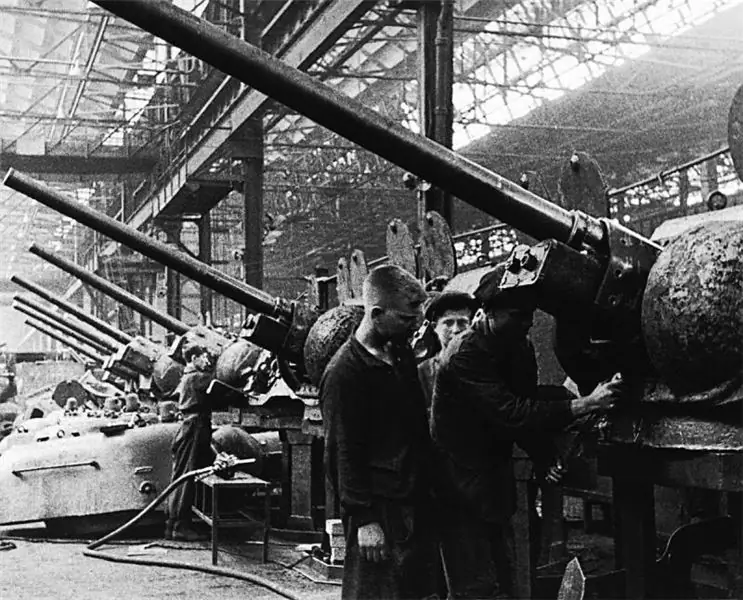
Les usines de réservoirs reposaient principalement sur le matériau réfractaire dinas produit par l'usine de Pervouralsk. Mais, d'une part, il n'était produit que 12 000 tonnes par mois et, d'autre part, les métallurgistes se sont taillé la part du lion.
L'expansion de la production à l'usine de Pervouralsk s'est déroulée très lentement. Et au milieu de 1942, seuls 4 nouveaux fours sont apparus. Les autres n'étaient pas prêts ou n'existaient généralement que dans des projets.
Les réfractaires pour les fours à foyer ouvert des usines de réservoirs étaient souvent de mauvaise qualité, pas entièrement et au mauvais moment. Seulement pour la réparation des fours Uralmash au quatrième trimestre de 1942, 1035 tonnes de briques résistantes au feu ont été nécessaires et seulement environ 827 tonnes ont été reçues.
En 1943, l'atelier à foyer ouvert d'Uralmash, en général, a failli s'arrêter en raison du manque de réfractaires à réparer.
La qualité des réfractaires fournis tout au long de la guerre laissait beaucoup à désirer. Si, dans des conditions normales, la brique dinas du four à foyer ouvert pouvait supporter 400 chaleurs, alors en temps de guerre, elle ne dépassait pas 135 chaleurs. Et en mars 1943, ce paramètre était tombé à 30-40 chaleurs.
Cette situation montre clairement comment le manque d'une ressource (en l'occurrence, le réfractaire) peut sérieusement ralentir le travail de l'ensemble de l'industrie de la défense. Comme l'écrit le candidat des sciences historiques Nikita Melnikov dans ses ouvrages, en mars 1943, trois fours à foyer ouvert d'Uralmash s'arrêtaient encore et effectuaient un cycle complet de travaux de réparation. Il a fallu 2346 tonnes de dinas, 580 tonnes de chamotte et 86 tonnes de magnésite rare.
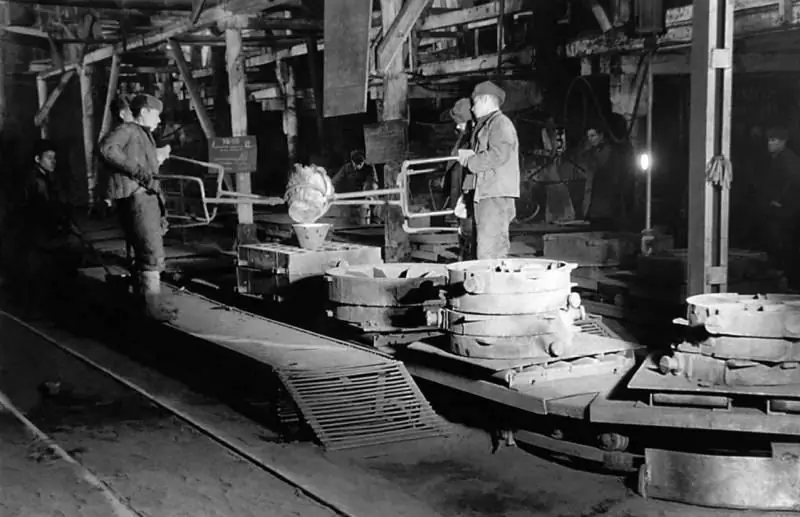
Au milieu de 1942, à l'usine de réservoirs n° 183, la situation évoluait de la même manière - la production d'acier était à la traîne par rapport à l'assemblage mécanique. Et nous avons dû "importer" les coques de T-34 d'Uralmash.
L'une des raisons était le manque de réfractaires pour la réparation des fours à foyer ouvert, qui au printemps 1942 fonctionnaient à leur limite. En conséquence, seuls 2 fours à sole ouverte sur 6 fonctionnaient à l'automne et les volumes de fusion n'ont été rétablis qu'au second semestre 1943.
La situation des réfractaires dans la structure du complexe de défense soviétique pendant la Grande Guerre patriotique illustre bien la complexité de la situation à l'arrière du pays.
Une pénurie chronique de, en général, pas le produit le plus high-tech a directement affecté le rythme de production de véhicules blindés.