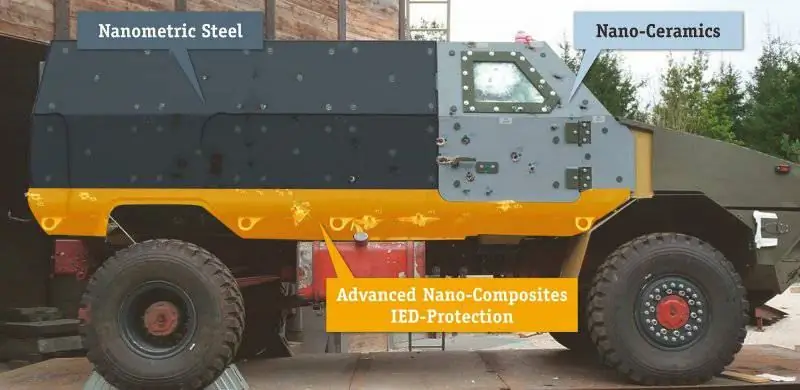
Le monospace Iveco utilise les dernières solutions de protection IBD Deisenroth, principalement basées sur la nanotechnologie
Armure passive: la dernière barrière
Les coques des véhicules blindés sont toujours en acier, auquel des kits de blindage supplémentaires sont boulonnés. Cependant, plus la conception de base peut donner en termes de protection balistique et explosive, plus le niveau final de protection sera élevé. De plus, même avec l'installation de systèmes de protection active qui détruisent les projectiles attaquants même à l'approche, les fragments à haute énergie résultants peuvent causer de graves dommages au véhicule, ce qui nécessite là encore une bonne protection de base
La société suédoise SSAB est l'un des spécialistes renommés dans le domaine des matériaux de blindage, et sa famille d'aciers de blindage Armox est bien connue dans le monde entier. La famille comprend six types différents, le nombre dans la désignation de la nuance d'acier indique la dureté Brinell moyenne. Alors que la dureté affecte directement la protection balistique, la ténacité est nécessaire pour absorber l'énergie du souffle - deux caractéristiques qui, en fait, ne peuvent pas coexister. La formabilité exacerbe ce conflit, car les aciers à haute résistance sont généralement moins formables et ont souvent des problèmes de soudabilité.
Au fil du temps, les caractéristiques balistiques des aciers SSAB se sont progressivement améliorées: en 1990, l'acier Armox 500T d'une épaisseur de 9 mm était nécessaire pour arrêter le projectile M193/SS92 volant à une vitesse de 937 m/s, mais dix ans plus tard avec l'Armox Alliage 600T, seulement 6 ont été nécessaires pour arrêter mm. Encore dix ans et 4,5 mm Armox Advance fait de même, même si le chiffre n'en vaut plus la peine, puisque la dureté est au-delà de l'échelle Brinell ! D'un niveau initial de 70,7 kg/m2, SSAB a réussi à réduire le poids à 47,1 kg/m2 en dix ans, et à 35,3 kg/m2 au cours de la prochaine décennie. Selon les experts de SSAB, aucune autre baisse significative n'est attendue, le chiffre réel pour 2020 est de 30 kg/m2. Le service R&D de l'entreprise travaille plus sur l'amélioration de la ténacité et de la formabilité du matériau existant que sur sa dureté, d'autant plus que l'explosion est aujourd'hui la principale menace. Son acier Armox 440T 420-480 HB Brinell a été surnommé le mangeur d'énergie préféré, et sa ténacité permet d'obtenir facilement n'importe quelle forme, comme un fond solide. Même l'acier Armox 500T plus dur, avec une dureté de 480-540 HB, est considéré comme un matériau de protection contre les explosions.
Comme mentionné ci-dessus, la principale caractéristique d'Armox Advanced est la dureté, c'est pourquoi cet acier est considéré par SSAB comme une céramique de facto. Par conséquent, l'entreprise déconseille fortement de le mouler ou de le souder, car il ne doit pas être chauffé au-dessus de 100°C pour conserver sa dureté. Comment atteindre des niveaux de protection et de poids similaires à l'avenir avec des matériaux plus moulables est une tâche très difficile aujourd'hui.
Parmi les nouveaux aciers de blindage, il faut bien sûr noter le Super Bainite, introduit à l'automne 2011. Développé par le laboratoire britannique des sciences et technologies de la défense DSTL, le nouvel acier est fabriqué chez Tata Steel UK. Il présente de bien meilleures performances que l'acier blindé standard. Ces caractéristiques ne sont pas seulement une conséquence de la composition chimique, mais aussi du procédé de fabrication, notamment traitement thermique avec refroidissement à l'air et aux sels fondus. Le produit final a deux fois les performances balistiques d'une armure homogène laminée.
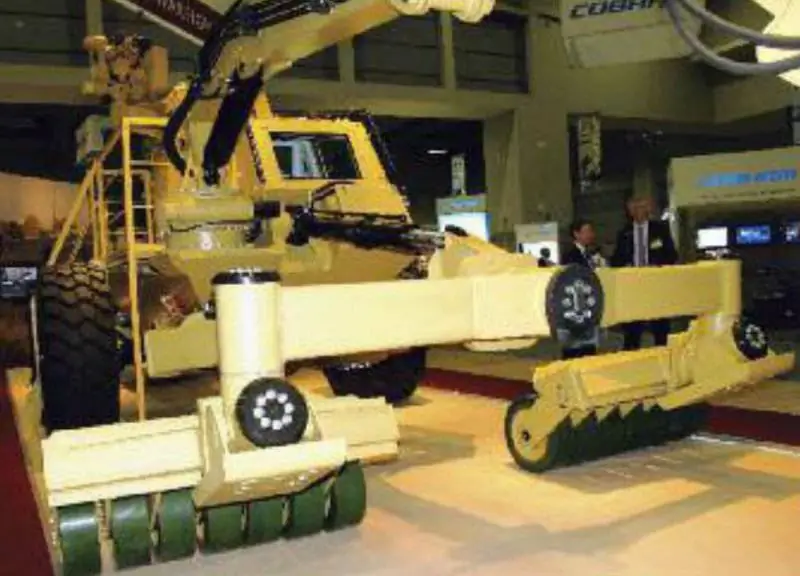
La société sud-africaine Aardvark Perroc utilise largement l'acier SSAB Armox 500 dans ses produits. Cela démontre que même cet acier à haute dureté est capable d'absorber de grandes quantités d'énergie.
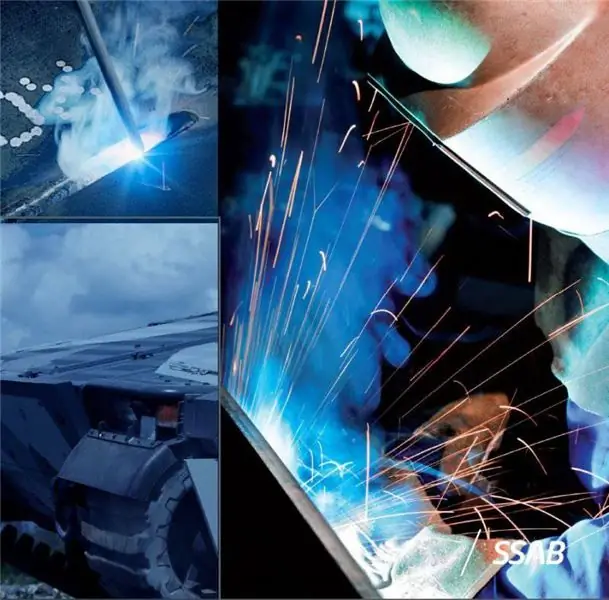
SSAB fabrique des formes complexes à partir de son acier Armox 440T, souvent appelé « mangeur d'énergie ». Il est très bien adapté aux structures exposées aux engins explosifs improvisés. SSAB travaille actuellement à rendre ses aciers de blindage plus moulables.
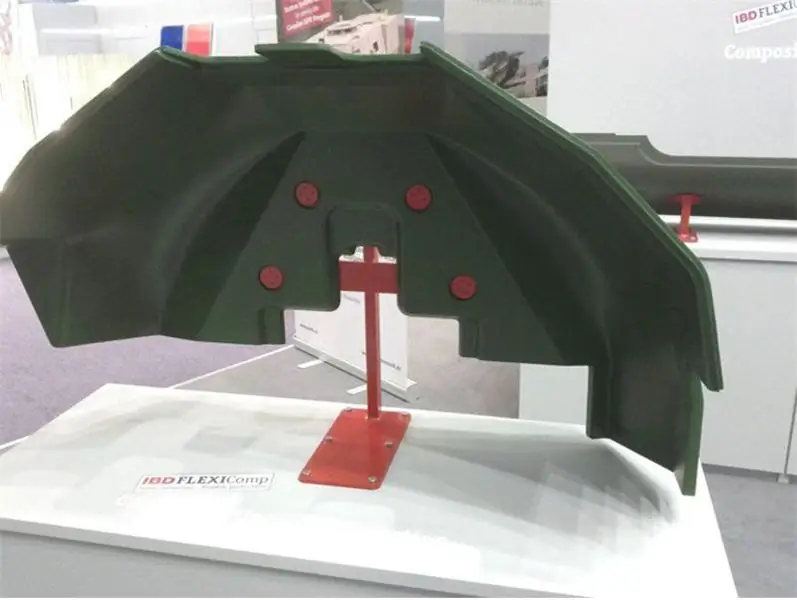
L'utilisation de la doublure IBD FlexiComp permet la production d'éléments de sécurité volumétriques, réduisant le nombre de points faibles dans le système de sécurité global
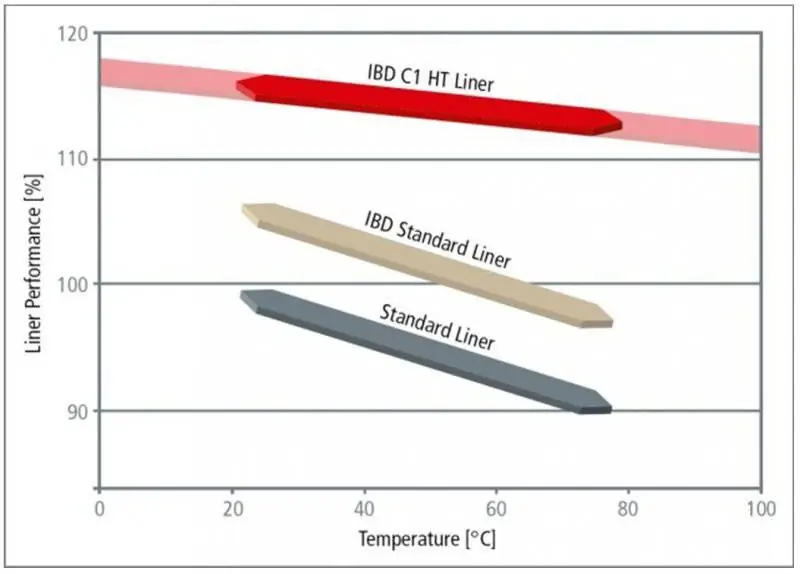
Diagramme des caractéristiques des chemises IBD en fonction de la température. L'effet des températures élevées est une préoccupation majeure lors du déploiement de machines dans des climats chauds
En décembre 2012, Lockheed Martin UK et l'Université du Surrey ont annoncé une nouvelle méthode plus simple pour améliorer la protection et la capacité de survie des véhicules blindés. Les scientifiques ont développé une méthode de traitement des matériaux céramiques afin d'améliorer la force d'adhérence des céramiques d'alumine et des céramiques de carbure de silicium à un substrat composite, ce qui augmente considérablement la résistance de l'armure. La fixation des plaques céramiques sur leur support a toujours été le talon d'Achille de cette technologie. Les résultats ont montré que la nouvelle technique améliore les forces de traction. Des tests ont montré que lorsqu'une balle incendiaire perforante de 14,5 mm est tirée sur une plaque de blindage, elle reste intacte.
Le développement technologique reste le cœur de métier d'IBD Deisenroth Engineering, tandis que les solutions passives sont actuellement sous-traitées à Rheinmetall Chempro, détenue à 51 % par Rheinmetall Defence et à 49 % par la famille Deisenroth.
Lorsque le Dr Ulf Deisenroth a développé les technologies de blindage de quatrième génération pour divers types de matériaux, la tâche était de réduire la masse tout en maintenant le niveau de protection, ou vice versa, d'augmenter le niveau de protection pour une masse donnée, tandis que les nouvelles technologies promettent des économies. de plus de 40 %. Ils s'appuient sur les dernières avancées dans le domaine de la protection passive associées aux nanomatériaux, qui comprennent les céramiques nanocristallines, l'acier nanométrique et les fibres à haute résistance. En collaboration avec des sidérurgistes, IBD a développé des aciers à l'azote à haute résistance qui sont presque à égalité avec les matériaux céramiques standard. Ces nouveaux types d'aciers peuvent être appliqués aux éléments structuraux, tandis qu'ils peuvent réaliser des gains de poids encore plus importants s'ils sont utilisés dans les premières étapes de la conception. Quant aux fibres à haute résistance, par exemple, IBD C1 HT Liner, elles ont des caractéristiques qui sont presque 20% plus élevées non seulement par rapport à la doublure standard, mais même 10% plus élevées que les autres doublures IBD; la détérioration de leurs paramètres avec l'augmentation des températures est également plus lente, ce qui est particulièrement important compte tenu des températures extrêmes sur les champs de bataille modernes. En plus des aciers nanométriques et des nanocéramiques utilisés sur les machines nouvellement développées, IBD a également développé de nouvelles solutions de matériaux composites qui permettent la production d'éléments avec des géométries courbes complexes, ce qui permet d'atteindre 100% de couverture de la zone protégée avec presque aucun écart balistique. Cette solution est notamment utilisée dans la réalisation d'éléments de fond, où le moindre écart peut compromettre l'ensemble de la protection.
IBD a également réussi à développer des stratifiés nanocomposites dont la résistance est tellement augmentée qu'ils peuvent remplacer les pièces structurelles d'une machine tout en servant également de protection balistique de haut niveau. Du fait de leur faible densité surfacique, le poids global de ce niveau de protection est ainsi considérablement réduit. Ces composites sont basés sur les matériaux nanotechnologiques susmentionnés d'IBD. Des processus de liaison spécifiques ont été développés et sont utilisés pour fabriquer des stratifiés nanocomposites de matériaux structurels, connus sous le nom d'IBD FlexiComp, avec une résistance structurelle et des performances balistiques accrues. Avec 10 % de densité en moins par rapport aux stratifiés standards, les propriétés élastiques de ces matériaux sont deux fois plus élevées. Cette haute résistance leur permet d'être intégrés dans la conception de la machine, tandis que les caractéristiques balistiques lui permettent de faire face aux menaces de haut niveau, tandis que les matériaux FlexiComp ont un bon potentiel de réduction de poids. Leur utilisation peut s'incarner dans deux approches différentes. Une approche directe consiste à les utiliser pour la protection contre les mines et les engins explosifs improvisés en tant que blindage supplémentaire dans les passages de roue, les ailes, les plaques antimines et les planchers internes espacés. Lors du moulage de pièces volumétriques, elles peuvent remplacer d'autres solutions, comme les assemblages assemblés par soudure ou boulonnage. La deuxième approche est l'intégration de pièces composites telles que les trappes, les trappes de moteur, les portes arrière et les rampes. Ils constituent une part importante de la surface totale du véhicule, et de ce fait, la réduction de poids absolue sera très importante. Pour le STANAG 4569 Niveau 4, cette réduction de poids est de 1500 kg pour une machine 8x8 (voir tableau). En termes de coûts de fabrication, les procédés développés par IBD permettent de réaliser des pièces composites sans l'utilisation d'autoclaves, offrant des économies de coûts importantes, notamment pour les composants de grande taille, leur coût est comparable au coût des composants réalisés avec des technologies standards.
Ces composants sont actuellement fabriqués par Rheinmetall Chempro, dont la tâche est de maîtriser les technologies IBD Deisenroth Engineering, de les développer dans un processus de production afin d'obtenir des prix compétitifs, de développer davantage des solutions spécialisées et de les suivre jusqu'au processus de qualification de la machine. Les livraisons de composants fabriqués à l'aide des dernières technologies de pointe ont commencé début 2013, principalement des machines AMPV de KMW-Rheinmetall et Medium Protected Vehicle d'Iveco DV-KMW. Plus d'une douzaine de fabricants d'équipement d'origine dans le monde recevront bientôt des composants qui leur permettront de réduire véritablement le poids de leurs machines, augmentant ainsi la charge utile et réduisant les coûts de cycle de vie, a déclaré la division Protection de Rheinmetall.
Le portefeuille passif de Rheinmetall Chempro comprend diverses versions de la famille Amap (Advanced Modular Armor Protection). Cette famille utilise la dernière technologie développée par IBD. Les produits Amap sont généralement combinés pour fournir la protection souhaitée contre une grande variété de menaces. Parmi les différents produits opaques, on retrouve la solution balistique Amap-B, qui assure une protection contre les armes légères et les munitions de moyen calibre, la protection contre les mines Amap-M, Amap-IED conçu pour lutter contre les IED, les doublures Amap-L qui protègent le compartiment de combat en absorbant les éclats d'obus secondaires, Amap-SC contre les projectiles HEAT et, enfin, la solution Amap-X, qui protège contre les menaces typiques des conditions urbaines.
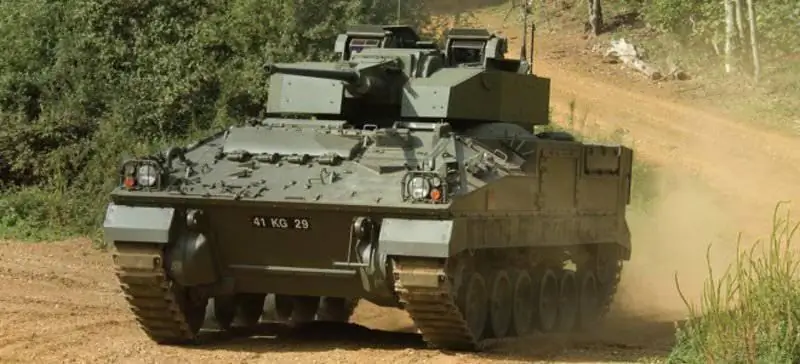
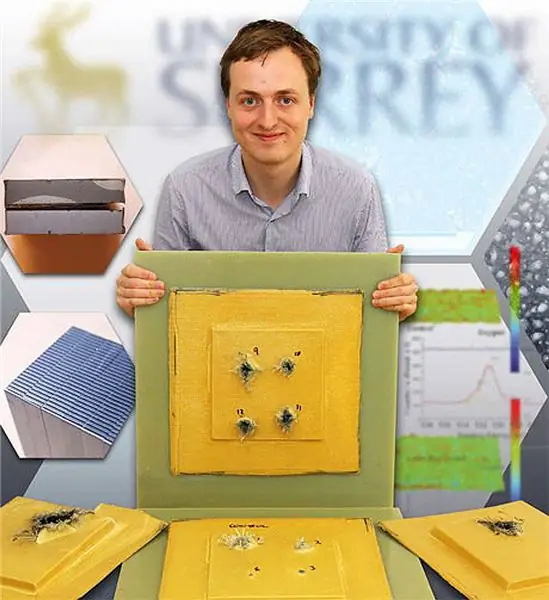
Une nouvelle technologie de collage développée par Lockheed Martin UK et l'Université du Surrey pourrait améliorer considérablement la protection des véhicules blindés tels que le Warrior BMP (ci-dessus)
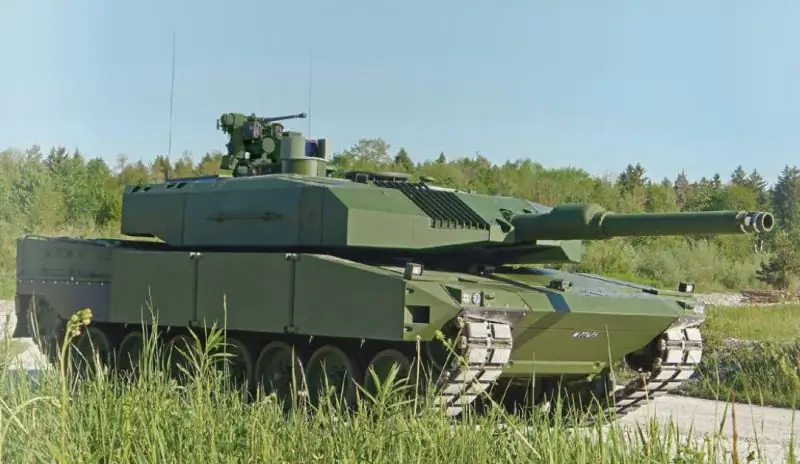
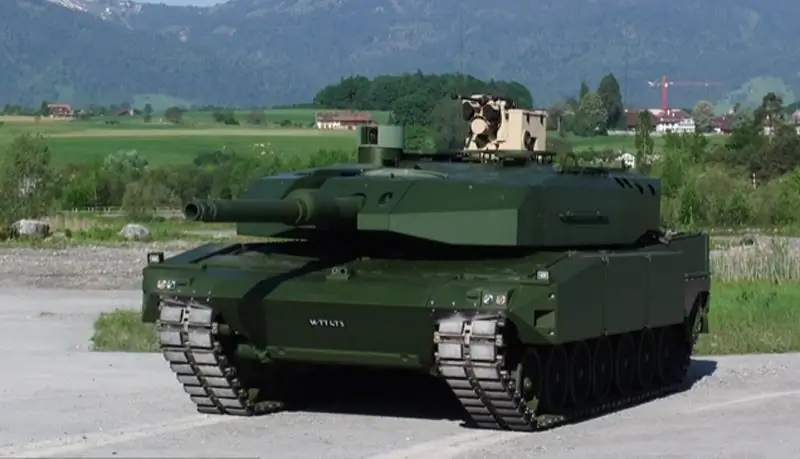
Modules SidePro-ATR supplémentaires pour MBT Leopard
A noter qu'au sein du groupe Rheinmetall, une autre société est engagée dans la protection passive, Rheinmetall Ballistic Protection GmbH, qui a reçu son nouveau nom le 1er janvier 2013. Auparavant, elle s'appelait Rheinmetall Verseidag Ballistic Protection GmbH. Entièrement détenue par Rheinmetall, cette entreprise est spécialisée dans la conception et la fabrication de solutions de blindage pour les véhicules militaires légers qui utilisent des matériaux tels que la céramique, les métaux avancés et les tissus spéciaux.
Bien que Ruag Defense ait toujours des solutions de protection dynamique (blindage actif-réactif) dans son portefeuille, elle ne se présente plus aux yeux des consommateurs comme une entreprise ultramoderne capable d'augmenter la capacité de survie des véhicules moyens et lourds. À cet égard, la société suisse s'est attachée à mettre au point des solutions entièrement passives capables de faire face aux charges cinétiques et creuses. Le système SidePro-ATR va bien au-delà de l'agressivité du RPG-7, car il peut gérer les charges creuses utilisées dans des scénarios symétriques, tandis que la version de base garantit une protection balistique de niveau 5. SidePro-ATR a été présenté pour la première fois au public en 2012, ce système est évolutif et peut donc être utilisé aussi bien sur des véhicules blindés de transport de troupes que sur des chars. Dans sa version de base, il a une épaisseur de 400 mm, et sa masse est comparable à la masse d'une solution réactive (soit environ 300 kg/m2). Ce système a été qualifié pour le char Leopard 2A4. Le niveau de protection balistique peut être considérablement augmenté au point que le système résistera à l'impact d'un noyau allongé de 120 mm, bien qu'aucune donnée n'ait été fournie à cet égard.
L'évolutivité de SidePro-ATR lui permet d'être utilisé dans des scénarios de combat symétriques et asymétriques. Une autre solution pour lutter contre les munitions cinétiques et les IED sous la désignation SidePro-KE / IED a été testée sur le véhicule blindé de reconnaissance Fennek, qui est en service avec l'Allemagne et les Pays-Bas. Principalement basée sur la céramique, cette solution était destinée à lutter contre les IED de première génération. Les nouvelles bombes en bordure de route, utilisées dans divers théâtres, génèrent des milliers de fragments à grande vitesse, et il est donc nécessaire de disposer de très bonnes caractéristiques multi-impacts. Depuis lors, Ruag a affiné le système KE / IED, s'éloignant de la céramique et utilisant des sacs multicouches non extensibles. La nouvelle solution SidePro-KE / IED, disponible depuis 2012, offre une protection de niveau 4 / niveau 5 contre les armes cinétiques et présente des performances multi-impacts extrêmement élevées. En supposant que le châssis soit en acier balistique de 7 mm, un panneau de 30 mm pourrait fournir la protection complète requise, le système KE / IED permettant le gain de poids le plus faible, en fonction uniquement du type de véhicule. Cette solution est en attente chez plusieurs constructeurs.
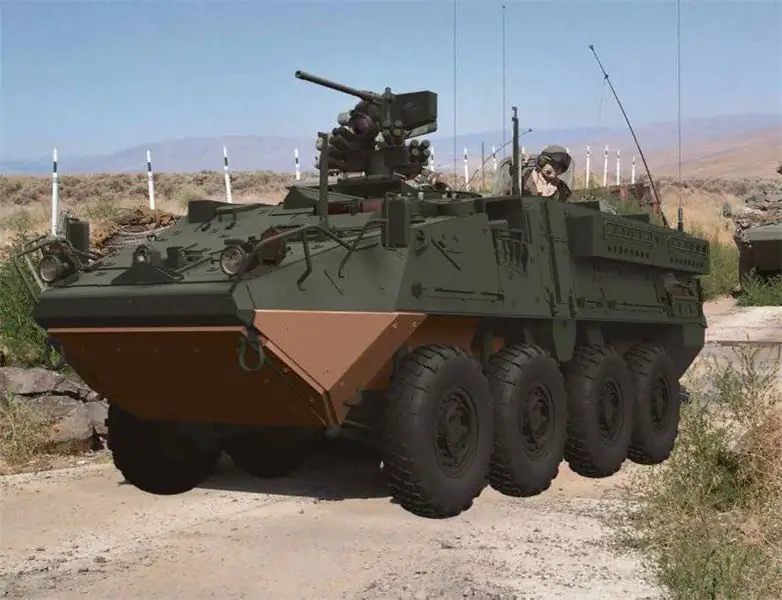
Ruag a finalisé le SidePro KE / IED. Le photomontage montre les éléments d'un système conçu pour contrer les nouveaux appareils qui génèrent de multiples fragments.
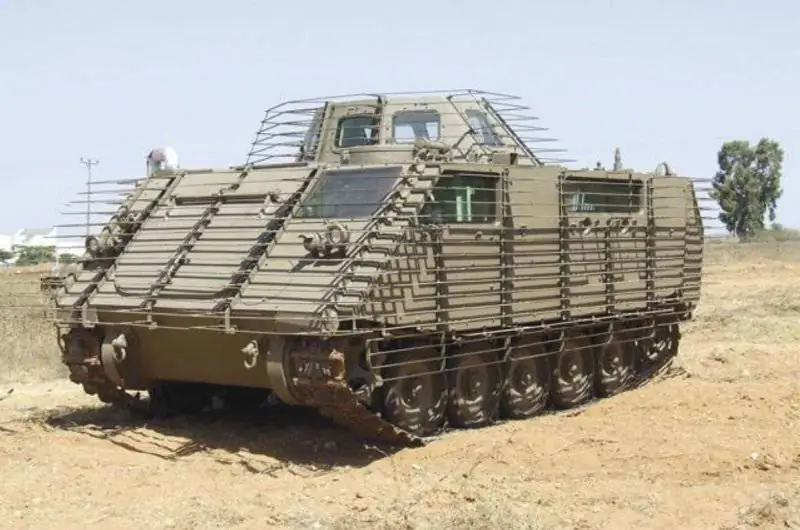
BTR M113, équipé d'un système passif anti-RPG Iron Wall d'Israel Military Industries, combinant une armure passive et en treillis
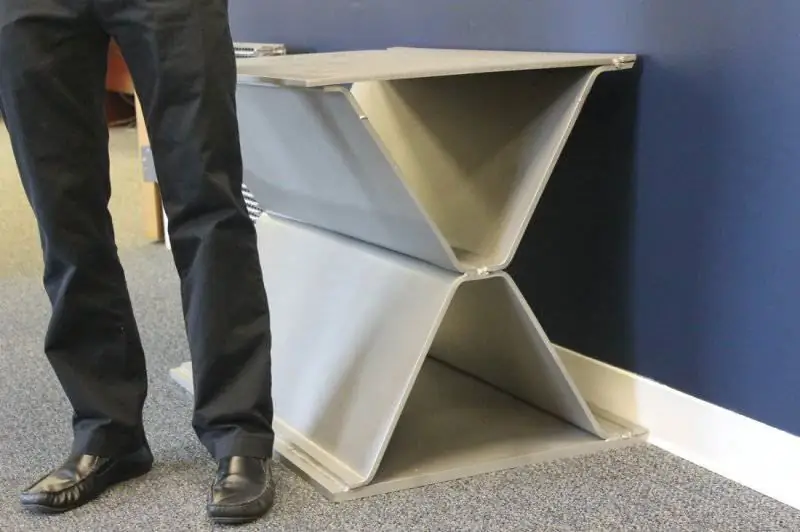
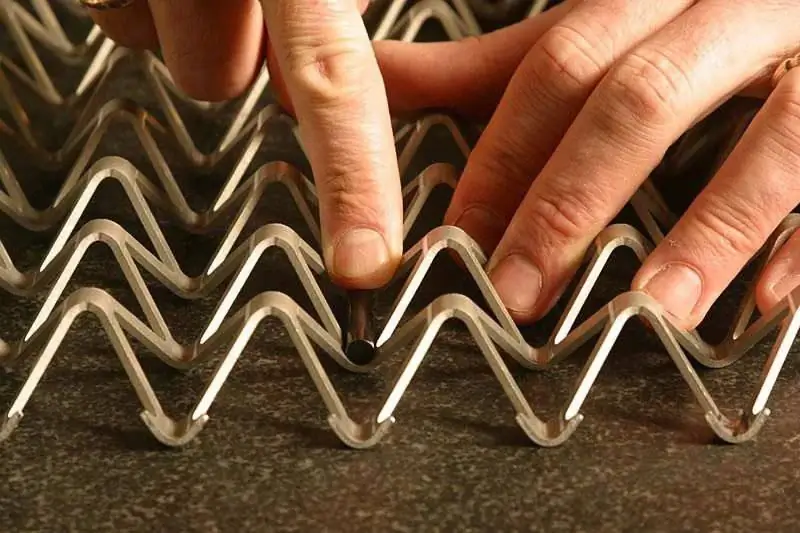
Ceradyne et Cellular Materials International ont développé un bouclier inférieur à base de nid d'abeille en aluminium CMI MicroTruss qui absorbe jusqu'à un tiers de l'énergie générée par une explosion. Ci-dessous se trouve le gros plan du matériel MicroTruss.
Exemple de réduction de poids pour une machine 8 x 8 avec des composants en IBD FLEXICOMP
Poids en kg
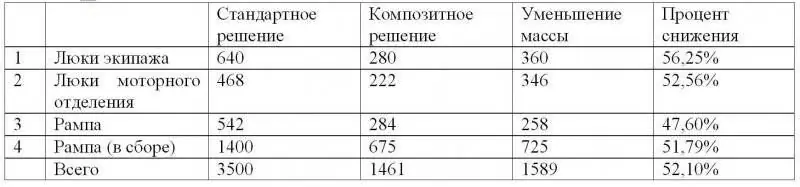
Plasan Sasa reste l'un des acteurs clés de l'industrie de la réservation passive. Aucun détail technologique n'est donné dans ce domaine, alors que la société est active à la fois dans les réservations supplémentaires et dans les bâtiments préfabriqués. La deuxième approche a été prise avec le développement du Mrap de Navistar MaxxPro et du M-ATV d'Oshkosh. "Cela nous permet d'augmenter la production en utilisant une main-d'œuvre sans compétences en soudage, car notre approche de style Lego est basée sur des blocs contenant tous les composants qui peuvent être assemblés en un minimum de temps", a déclaré une source de l'entreprise. Certains des plus de deux cents ingénieurs de l'entreprise travaillent sur de nouvelles solutions qui pourraient résulter de l'émergence de nouveaux matériaux ou de solutions géométriques innovantes. L'approche systémique reste au cœur du cycle de protection.
IMI a récemment développé une gamme de solutions passives et réactives pour contrer les derniers types d'IED, y compris les différents types de "shock cores" EFP ou SFF (Self Formed Fragmentation) et les derniers modèles RPG. La société a proposé une solution passive Iron Wall basée sur une combinaison de métal et de composites complétée par une armure en treillis. Selon le niveau de protection recherché, l'épaisseur peut varier entre 110 et 150 mm et le poids entre 200 et 230 kg/m2. Iron Wall subit actuellement des essais militaires avec l'armée israélienne.
IMI propose également son blindage en treillis en tant que système autonome. L-VAS (Light Vehicle Armor System - système de blindage pour véhicules légers) est conçu pour protéger les véhicules tels que les véhicules blindés de transport de troupes. Afin de réduire le poids, le système est basé sur des matériaux composites et des éléments réactifs, ces derniers contiennent un minimum de matériaux énergétiques. Cela réduit les pertes indirectes, et le type de matériau évite le risque de détonation secondaire des éléments adjacents. Selon IMI, le système L-VAS protège également contre les obus perforants de 14,5 mm et les fragments d'artillerie. Le système a été entièrement qualifié en Israël pour son M113 APC et a une densité d'environ 200 kg / m2.
Un système de brise-lames plus lourd est également offert. Cette armure réactive, composée d'éléments métalliques et composites, est conçue pour lutter contre trois menaces principales: les RPG, les SFF et les EFP. IMI a effectué des tests approfondis et procède actuellement aux qualifications pour commencer à produire une solution d'une épaisseur de 350 à 400 mm et d'un poids de 430 à 450 kg / m2 fin 2013.
Ceradyne est un autre acteur majeur du booking passif. Selon Mark King, président de Ceradyne, l'acier reste le matériau principal dans le domaine des réservations, dans le but d'améliorer les performances et de réduire les coûts. "Aux États-Unis, le facteur déterminant est principalement le coût d'acquisition d'un véhicule, pas le coût de sa durée de vie, et cela va à l'encontre des mises à niveau", a déclaré King lors de la conférence AUSA de 2012. tandis qu'aux États-Unis, l'accent était mis sur quantité, ce qui a amené les développeurs européens de systèmes de protection devant les développeurs américains. Cependant, King a souligné que l'Amérique progressait actuellement, en se concentrant principalement sur la protection anti-explosive du soubassement, la protection balistique étant considérée comme un problème résolu. L'intérêt de l'armée américaine, encore une fois démontré à résoudre le problème de la protection du dessous de véhicules tels que, par exemple, le Humvee (20 millions de dollars seulement pour le développement), est évalué positivement par King. Ceradyne fait partie de ceux qui seront certainement en compétition pour un contrat pour leur modernisation. L'exigence prévoit une protection maximale avec des économies de poids significatives afin de réduire l'impact sur les performances de la machine.
Ceradyne a développé une solution MicroTruss de Cellular Materials International Inc (CMI). Ce matériau en alliage d'aluminium poreux a une densité de 58 kg/m2 par rapport à la densité de 112 kg/m2 d'une solution métallique monolithique équivalente. Cette solution diffère par l'angle "V" du corps égal à seulement 5°, ce qui est suffisant pour réfléchir l'onde de choc et a une masse de 300 kg. MicroTruss garantit une absorption jusqu'à 30% de l'énergie d'explosion, ce qui non seulement limite l'impact sur la capsule de l'équipage, mais réduit également le mouvement vertical du véhicule. Ceradyne est également fortement impliqué dans le programme de réservation Flyer Gen.2, qui vise le projet Special Operations Forces pour le GMV 1.1. Pour maintenir la transportabilité à l'intérieur des hélicoptères V-22, CH-47D et CH-53E lorsque la masse et la largeur doivent être maintenues dans certaines limites, la société a développé un kit qui fournit un niveau de protection balistique B6 (.357 Magnum) pour les portes et toit.
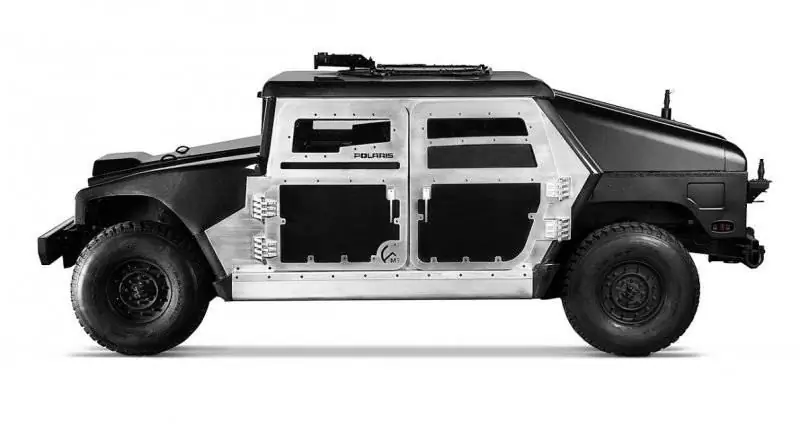
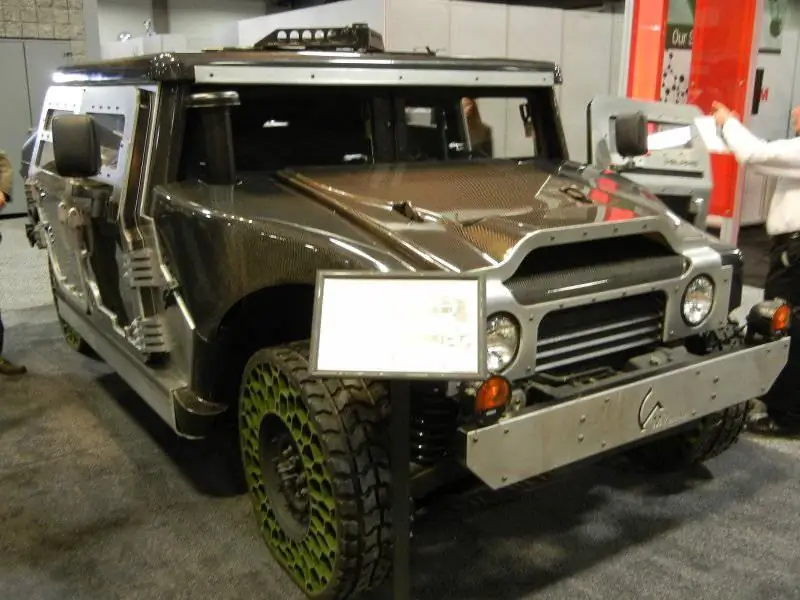
Polaris Defence et M9 Defense Armor Technology ont développé une armure structurelle composite en acier hybride qui peut réduire considérablement le poids du Humvee tout en maintenant les niveaux de protection. Le prototype illustré à droite a un poids à vide de seulement 3 400 kg, soit près de 50 % de moins que le Humvee avec protection de niveau 3.(Notez les roues de la voiture en bas)
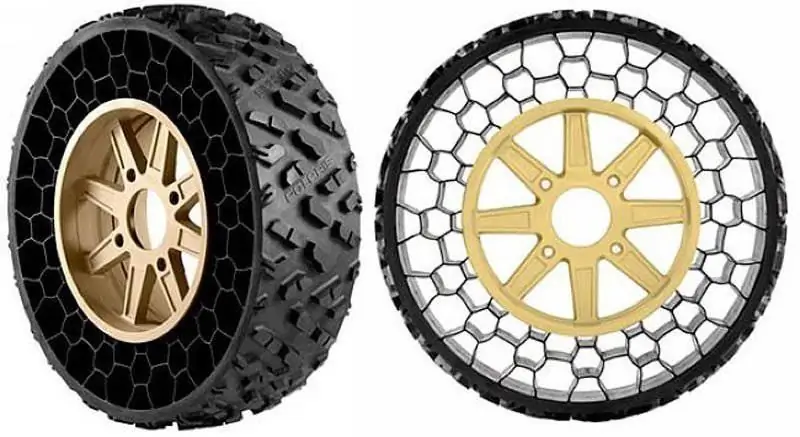
La protection, c'est aussi ne pas rester sur le champ de bataille en cas de crevaison d'une roue. Les roues non pneumatiques de Polaris Defense garantissent une durabilité nettement supérieure par rapport aux pneus standard et peuvent résister à une balle de 12,7 mm. Actuellement, elles sont disponibles non seulement pour les voitures, y compris la classe Hummer, mais maintenant ces roues sont également développées pour les voitures plus lourdes de la classe Mraps.
Ceradyne participe également au programme de transport de personnel des Marines en partenariat avec Lockheed Martin et Patria sur un véhicule du Corps des Marines basé sur le Patria AMV finlandais. Il est à noter que le 28 novembre 2012, il a été annoncé que Ceradyne a été acquis par le Groupe 3M, ce qui lui permettra d'investir davantage dans la R&D et les solutions innovantes.
L'intégration du design et de la protection est une solution très recherchée pour les véhicules légers. À AUSA 2012, Polaris Defence a présenté un prototype de véhicule Humvee avec un nouveau concept développé en collaboration avec M9 Defence. Le défi consiste à réduire le poids à vide tout en maintenant et en augmentant les niveaux de protection. Pour ce faire, l'équipe Polaris-M9 a retiré tout le blindage supérieur pour examiner le concept de blindage structurel. Ensuite, tout a été retiré de la voiture, il ne restait qu'un châssis nu, puis une structure hybride légère (matériau acier-composite) a été posée dessus. Cette armure structurelle peut fournir une protection de niveau 3 avec une masse de 70 kg / m2, et avec une masse de 83 kg / m2, elle est capable de résister à une balle de 12,7 x 99 mm, bien que le groupe Polaris-M9 soit convaincu qu'il peut atteindre le niveau 3+ (balle perforante de 12, 7 mm). La solution Polaris-M9 protège également le moteur. Alors que le véhicule blindé standard Hummer pèse environ 6 350 kg, la solution proposée permet de réduire son poids à 3 400 kg. L'armure structurelle hybride utilise un matériau non exotique, ce qui permet à l'équipe Polaris-M9 de parler du coût de la nouvelle solution, comparable au coût des solutions actuelles. De plus, ce matériau est moulé dans des formes complexes, ce qui donne, entre autres, des fonds en forme de V sans couture. L'obtention de la forme souhaitée est obtenue grâce au formage hydraulique - un processus à grande vitesse qui contribue à réduire les coûts. Selon l'équipe Polaris-M9, cette technologie peut réduire le poids de 40 %.
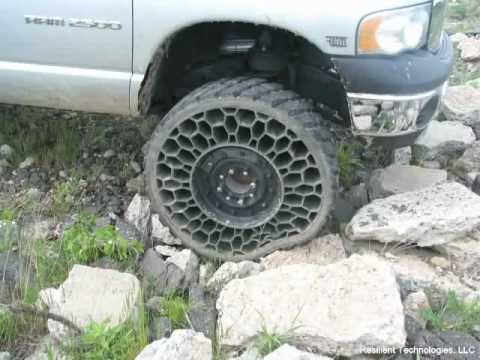
Démonstration des roues non pneumatiques de Polaris Defence
L'équation de défense comprend un autre terme qui se rapporte directement à la mobilité - la roue. Suite à l'acquisition de Resilient Technologies, Polaris Defence propose désormais des roues non pneumatiques (NPT). La consommation des roues est l'un des problèmes logistiques les plus importants dans un moteur à turbine et la solution NPT aidera dans de nombreux cas à le résoudre. Selon le commandement des forces d'opérations spéciales en Afghanistan, les pneus conventionnels parcourent environ 1 300 km, tandis qu'une roue NPT crevée par une balle de 12,7 mm peut parcourir plus de 8 000 km et, par conséquent, déplacer les roues de secours de la chaîne d'approvisionnement, tout en améliorant la qualité de conduite.. Des prototypes NPT ont déjà été réalisés pour les véhicules Hummer. L'objectif actuel est un jeu de roues NPT pour la machine de 7,7 tonnes, ce qui représente presque le poids total de la variante JLTV à usage général. Selon les représentants de l'entreprise, la modélisation a montré que la masse peut atteindre 18 tonnes, c'est-à-dire que les roues peuvent supporter une voiture de classe Mrap. À mesure que la charge utile augmente, la technologie reste la même et les programmes de simulation de l'entreprise permettent des prévisions très précises. Ce qui va changer, c'est le matériau qui doit s'adapter à la masse, qui à son tour n'a pas encore fait son apparition dans le futur.