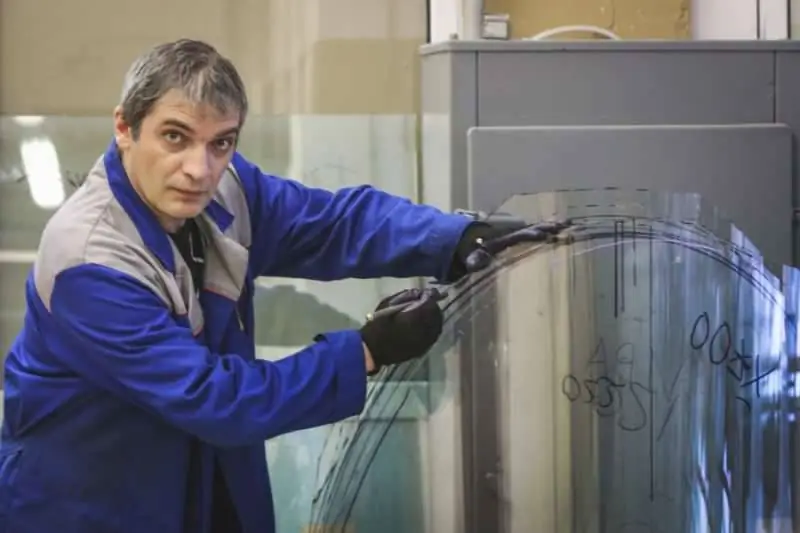
En Russie, de nouvelles technologies ont été développées pour la fabrication de vitrages de cabines d'avions militaires et civils à partir de verre au silicate. De tels produits s'avèrent plus légers et plus résistants que s'ils étaient créés à partir de matériaux organiques précédemment utilisés. Le verre au silicate est également utilisé dans d'autres domaines, de l'exploration spatiale à la construction de logements.
Depuis plusieurs années maintenant, il y a un débat parmi les chercheurs spatiaux sur l'évaluation de la sécurité et l'exploitation de la Station spatiale internationale. Le fait est qu'il y a 13 fenêtres installées dans le segment russe de l'ISS. Lors des discussions conjointes sur l'ISS, il est proposé de fermer les fenêtres du segment russe avec des bouchons aveugles en raison du danger de défauts dans le verre dus aux impacts de micrométéorites - disent-ils, la sécurité de la station pourrait s'améliorer. Mais le représentant de la partie russe - le directeur de l'Institut de recherche scientifique sur le verre technique (NITS), scientifique émérite, vice-président de l'Académie des sciences de l'ingénieur de la Fédération de Russie, docteur en sciences techniques, le professeur Vladimir Solinov tient bon - pendant de nombreuses années, la résistance résiduelle après l'impact des microparticules spatiales a été préservée et, divers rayonnements et autres menaces provenant de l'espace n'ont pas affecté la sécurité des fenêtres créées à l'institut, ainsi que l'équipage, il n'y a donc aucune raison de limiter l'observation de notre planète, « obscurcit » le travail des cosmonautes dans les modules russes de la station orbitale.
Les hublots pour la station orbitale ne sont que l'un des rares produits fabriqués par NITS. L'essentiel du travail des scientifiques et des technologues de l'institut situé dans le sud-ouest de Moscou est bien sûr associé à la création d'optique structurelle, de vitrage ou comme on dit ici de "systèmes optiques transparents complexes" pour avions de combat des quatrième et cinquième générations produites par les usines UAC. Et chaque année, il y a beaucoup plus de travail pour l'aviation.
Silicate ou organique
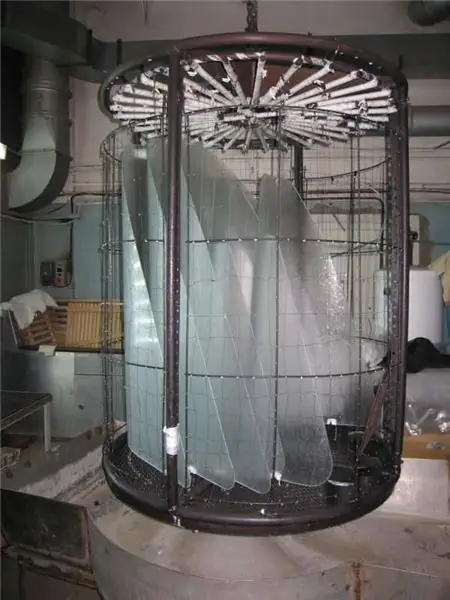
Sur la photo: ébauches de pare-brise T-50 dans une cassette de durcissement.
Le verre silicaté est un matériau aux propriétés uniques. Sa transparence, son optique élevée, sa résistance à la chaleur, sa résistance et la possibilité d'utiliser divers revêtements le rendent indispensable pour les vitrages aéronautiques. Mais pourquoi la priorité a-t-elle été donnée à la matière organique lors des vitrages des cabines d'avions à l'étranger et dans notre pays ? Pour une seule raison - c'est plus facile. On dit aussi que le verre au silicate est trop fragile.
Au cours des dernières années, les développements des scientifiques des matériaux NITS ont permis de changer radicalement le concept du verre de silicate en tant que matériau fragile. Les méthodes modernes de renforcement permettent de donner au vitrage des avions de combat modernes une résistance suffisante pour résister à l'impact d'un oiseau pesant environ deux kilogrammes à une vitesse de 900 km / h.
« Aujourd'hui, la méthode de durcissement de la couche superficielle s'est épuisée. Il est temps de changer la structure interne du verre, sa défectuosité », explique Vladimir Solinov. Aussi étrange que cela puisse paraître, cela est facilité par les sanctions imposées par l'Occident. Le fait est que même à l'époque "avant la sanction", les entreprises étrangères, par décision de l'OTAN, n'ont pas fourni à la Russie de verres au silicate de meilleure qualité, qui y étaient utilisés à des fins spéciales. Cela a obligé NITS à utiliser du verre architectural. Bien que les fabricants russes produisent des millions de mètres carrés de ce verre, sa qualité ne convient pas à une utilisation dans l'aviation.
La substitution des importations est venue à la rescousse: un nouveau projet de R&D et de conception d'équipements fondamentalement nouveaux pour l'industrie verrière a été lancé à Moscou.
Tous les procédés de synthèse du verre avec priorité russe seront testés dessus.
Le projet a été confié à la jeune scientifique Tatiana Kiseleva. Diplômé de 26 ans de l'Université russe de technologie chimique. D. I. Mendeleeva est à la tête du laboratoire, en 2015 elle a soutenu sa thèse. Au département du verre de Mendeleevka, Tatiana a étudié les propriétés des armures transparentes. L'un de ses défis professionnels est de développer un verre dont les propriétés seraient supérieures à celles de l'un des meilleurs analogues au monde - le verre herkulit, que la Russie n'a pas encore produit.
Le projet repose sur une nouvelle méthode originale de fusion du verre. Déjà aujourd'hui, le laboratoire a obtenu des échantillons de verre dont la résistance structurelle est trois fois supérieure aux analogues obtenus par la méthode traditionnelle. Ajoutez à cela les méthodes de durcissement existantes et vous obtenez du verre dont la résistance est plusieurs fois supérieure à celle de nombreux types d'acier allié. Un verre plus durable rend les produits plus légers. Cependant, il convient de noter que les développeurs de verre organique améliorent constamment les performances techniques de leurs produits, le différend sur le verre le meilleur n'est pas terminé.
Lanterne pour T-50
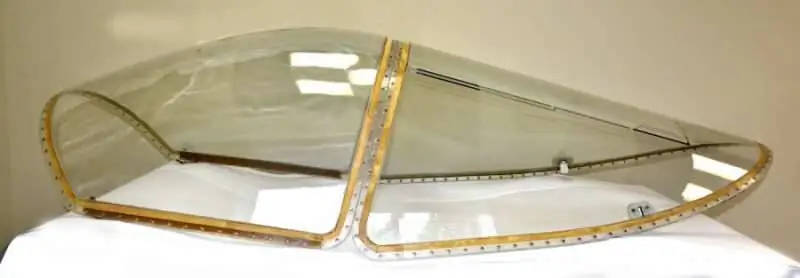
Sur la photo: un ensemble de vitrages pour un avion T-50 - une visière frontale et une partie pliante.
Imaginez un paquet de plusieurs plaques de verre de silice dont vous souhaitez rationaliser la visière avant d'un avion à grande vitesse.
Il y a une quarantaine d'années, les spécialistes du NITS ont développé la technologie du pliage profond. Plusieurs couches de verre sont déposées dans un four spécial. Pendant plusieurs heures à des températures élevées sous son propre poids, le verre se plie, acquérant la forme et la courbure souhaitées. Si nécessaire, des mécanismes spéciaux poussent la pièce, la forçant à se plier selon un calendrier spécial.
Pour la première fois au monde, utilisant cette technologie, le chasseur MiG-29 a remplacé la lanterne composée de trois verres par un verre sans silicate.
Avec une augmentation de la vitesse, les exigences de résistance à la chaleur du vitrage ont augmenté, auxquelles le verre organique ne pouvait plus faire face. Dans le même temps, les exigences en matière d'optique et de visibilité ont été renforcées. Il y a plusieurs années, en coopération avec la société Sukhoi, la United Aircraft Corporation, une nouvelle technologie pour la production de verre pour le T-50 a été développée.
Le développement a été financé par les avionneurs, en partie par le ministère de l'Industrie et du Commerce. Une aide substantielle a été apportée dans la réalisation du rééquipement technique de l'entreprise, a déclaré Yuri Tarasov, directeur du Centre technologique de l'UAC.
En conséquence, le pare-brise de l'avion T-50 est presque deux fois plus grand que la visière du MiG-29, et la forme du produit d'un cylindre classique s'est transformée en un format 3D complexe.
Le résultat - pour la première fois au monde, la partie frontale et pliante de la verrière de l'avion T-50 (fabriquée par Sukhoi) était en verre de silicate au format 3D. De plus, le poids de ces pièces s'est avéré plus faible que s'il s'agissait de verre organique.
Les résultats obtenus ont donné une impulsion à l'équipement des avions d'autres usines et bureaux d'études faisant partie de l'UAC avec des vitrages similaires. Immédiatement, il y avait un besoin de modernisation, en remplaçant le vitrage organique par du silicate, par exemple sur les avions Yak-130, Su-35, MiG-31, MiG-35. Après un tel remplacement (c'est-à-dire l'amélioration des caractéristiques de résistance du vitrage), le MiG-35, par exemple, a atteint pour la première fois une vitesse allant jusqu'à 2000 km / h, c'est-à-dire qu'il a pu voler 40% plus vite en moyenne que tout autre avion dans le monde.
Ces dernières années, le style de travail des scientifiques de Moscou a sérieusement changé. Environ trois cents spécialistes NITS effectuent un cycle complet - des spécifications techniques à la production à petite échelle. Cela comprend le développement de la technologie et la sélection de matériaux clés lors de l'utilisation du verre, ainsi qu'un vaste cycle de test pour tous les facteurs affectant l'avion, à la fois au sol et dans les airs.
Plusieurs exigences clés sont imposées au verre moderne, parmi lesquelles, en plus de la haute résistance, la transparence optique, la transmission lumineuse élevée, l'augmentation de la plage de vision, les propriétés antireflet, la protection contre les effets du rayonnement solaire et d'autres rayonnements, l'antigivrage propriétés, assurant une résistivité électrique uniforme.
Tout cela est réalisé par revêtement en aérosol, sous vide ou magnétron. Un équipement puissant et sophistiqué évaporant le métal et le déposant sur la surface du verre permet à NITS d'appliquer tous les revêtements, y compris ceux protégeant contre des facteurs spéciaux.
Cet ensemble de propriétés permet de parler d'un vitrage comme d'un système optique complexe, et les propriétés de haute résistance du verre, qui fait partie du cockpit de l'avion, ont créé un nouveau domaine scientifique et technologique et introduit le terme « optique structurelle produits » (ICO).
Nouvelles technologies
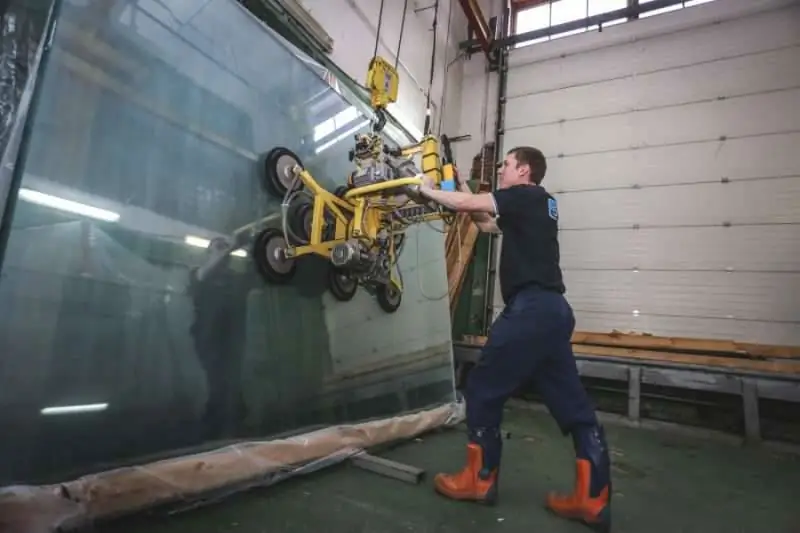
Sur la photo: chargement d'une feuille de verre pour un traitement ultérieur.
Lorsque le produit - la partie articulée de la lanterne du T-50 - est déchargé du four pour un traitement ultérieur, il ne ressemble guère à un futur produit. Lors du pliage du verre, les bords de la pièce sont déformés et il est impossible de les retirer d'une pièce de grande taille, de forme géométrique complexe, avec un outil diamanté. Le laser est venu à la rescousse. Le faisceau laser du complexe robotique non seulement coupe la pièce selon le programme qui y est défini, mais également, en faisant fondre le bord, augmente la résistance du bord des produits, empêchant l'apparition de fissures. La découpe au laser de produits 3D de grande taille a été utilisée pour la première fois à Moscou. Cette méthode a été brevetée en mars 2012. Le faisceau laser est également utilisé pour couper la couche électriquement conductrice sur la surface du verre, créant des zones de chauffage. Après le traitement au laser, la pièce ressemble de plus en plus à une lampe de poche T-50.
Après la coupe, chaque pièce est traitée sur une machine à cinq axes. Le logement unique lui permet de fournir des contraintes de montage initiales nulles. Le technologue en chef de l'institut, Alexander Sitkin, a évoqué les perspectives d'utilisation du complexe pour le meulage et le polissage de la surface du verre: un travail qui, si nécessaire, est effectué uniquement manuellement. Les technologies développées font la fierté de l'institut.
Plus récemment, un bloc de verre fini à l'aide d'un scellant a été monté dans un cadre métallique. Le passage aux matériaux composites développé par NITS a permis de réduire le poids du produit de 25 %, d'augmenter la résistance aux oiseaux et la ressource vitrage au niveau de la ressource vitrage vitrage. Il est devenu possible de remplacer le vitrage sur le terrain.
L'ensemble du cycle de production de l'ICO dure environ un mois et demi. La plupart des produits vont aux usines de fabrication d'UAC, certains pour réparer les usines de modernisation, et certains aux aérodromes de l'armée de l'air, dans les soi-disant trousses de premiers secours. L'essentiel des produits NITS est réalisé dans le cadre de l'ordonnance de défense de l'Etat.
NITS est réticent à partager des informations sur les caractéristiques des vitrages pour avions de combat. Mais il est clair que les verres développés pour les cockpits des avions civils domestiques sont supérieurs aux verres importés dans un certain nombre de paramètres.
Par exemple, comme vous pouvez le voir sur le site du NITS, l'épaisseur du verre sur le Tu-204 est de 17 mm, l'épaisseur du verre avec les mêmes propriétés pour le Boeing 787 est de 45 mm.
Génération V
Au cours des dernières années, le directeur de l'institut, Vladimir Solinov, a réussi à rajeunir considérablement l'équipe. Des jeunes et des spécialistes expérimentés travaillent à la production moscovite, qui a récemment célébré son 60e anniversaire. Les étudiants seniors de Mendeleevka viennent volontiers ici. Venant exercer à l'institut et apprenant qu'il existe des salaires de 70 000 roubles, ils sont d'abord employés par des travailleurs ordinaires, puis ils atteignent rapidement le niveau de technologues. Il y a aussi beaucoup de travailleurs expérimentés.
L'un d'eux, Nikolai Yakunin, traite du verre pour les hélicoptères. « Je suis venu ici juste après l'armée, il y a quarante ans. Mais sans le haut niveau d'automatisation, il n'aurait probablement pas survécu. C'est difficile pour moi de travailler toute la journée même en bonne forme physique avec un produit pesant 30 kg », explique Yakunin.
Les gens et les ongles
Partout dans le monde, les technologies développées pour la construction aéronautique qui permettent la production de verres de la résistance requise sont utilisées dans de nombreux autres secteurs de l'économie nationale.
Il y a plusieurs années, pour prouver la haute résistance du verre silicaté, l'institut fabriquait… des ongles en verre. Ils m'ont battu avec un marteau. Ils pourraient trouver une application dans des produits aux propriétés antimagnétiques.
De plus, ces clous ont été testés lors de la construction, à la place des pinces lors du collage des coques de yacht. Mais les ongles ne sont restés qu'exotiques. Désormais, personne n'a besoin de prouver la haute résistance du verre - toutes les œuvres de NITS sont la preuve de la haute qualité de ce matériau ancien et, en même temps, complètement nouveau.
Le directeur de l'institut Vladimir Solinov utilise toutes ses capacités pour prouver la nécessité d'assurer une haute résistance du verre, y compris architectural et de construction.
Il est membre de la Commission russo-américaine sur la sécurité spatiale, dont il a été question au début de cet article, ainsi que de la Commission sur le développement urbain de la Douma d'État - après tout, dans la construction de bâtiments modernes, une part croissante des matériaux est le verre. Cela signifie que les technologies et les matériaux développés pour l'aviation rendront dans un proche avenir la vie de millions de personnes plus confortable et plus sûre.