Début août 2016, l'US Navy a testé avec succès le tiltrotor Osprey MV-22. Cet avion lui-même n'est pas inhabituel. Le véhicule birotor est en service dans la marine américaine depuis longtemps (il a été mis en service dans la seconde moitié des années 1980), mais pour la première fois dans l'histoire, des pièces critiques ont été installées sur un tiltrotor (sécurité des vols dépend directement d'eux), qui étaient une imprimante imprimée en 3D.
Pour les tests, l'armée américaine a imprimé un support pour fixer le moteur à l'aile du tiltrotor en titane à l'aide d'un frittage laser direct couche par couche. Dans le même temps, une jauge de contrainte a été montée sur le support lui-même, conçu pour enregistrer une éventuelle déformation de la pièce. Chacun des deux moteurs du tiltrotor Osprey MV-22 est fixé à l'aile à l'aide de quatre supports de ce type. Parallèlement, lors du premier vol d'essai du tiltrotor, qui a eu lieu le 1er août 2016, un seul support, imprimé sur une imprimante 3D, y était installé. Auparavant, il avait été signalé que les supports de nacelle imprimés par la méthode d'impression tridimensionnelle étaient également installés sur le rotor basculant.
Le développement des pièces imprimées pour le tiltrotor a été réalisé par le US Navy Aviation Combat Operations Center situé à la base commune McGuire-Dix-Lakehurst dans le New Jersey. Des essais en vol de l'Osprey MV-22 avec des pièces imprimées ont été effectués à la base de l'US Navy à Patxent River, les tests ont été reconnus par l'armée comme totalement réussis. L'armée américaine pense que grâce à l'introduction généralisée de l'impression tridimensionnelle, la technologie sera à l'avenir en mesure de produire rapidement et à relativement bon marché des pièces de rechange pour les convertisseurs. Dans ce cas, les détails nécessaires peuvent être imprimés directement sur les navires. De plus, les pièces imprimées peuvent ensuite être modifiées afin d'améliorer les performances des ensembles et systèmes embarqués.
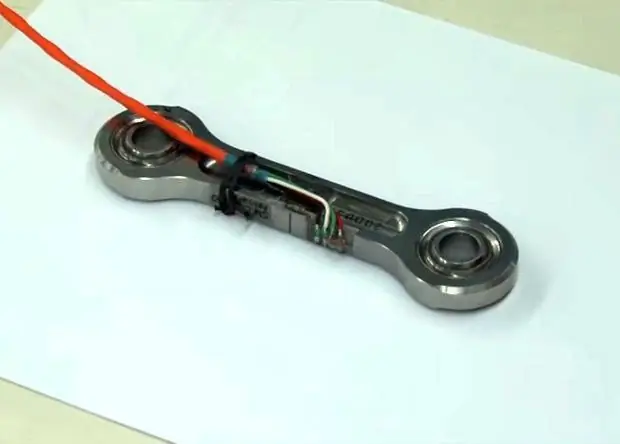
Support de montage de moteur imprimé en titane
L'armée américaine s'est intéressée aux technologies d'impression 3D il y a quelques années, mais jusqu'à récemment, les fonctionnalités des imprimantes 3D n'étaient pas assez larges pour être utilisées en routine pour construire des pièces assez complexes. Les pièces du tiltrotor ont été créées à l'aide d'une imprimante 3D additive. La pièce est faite progressivement en couches. Toutes les trois couches de poussière de titane sont collées au laser, ce processus est répété aussi longtemps que nécessaire pour obtenir la forme souhaitée. Après achèvement, l'excédent est coupé de la pièce; l'élément résultant est complètement prêt à l'emploi. Étant donné que les tests se sont terminés avec succès, l'armée américaine ne s'arrêtera pas là, elle va construire 6 éléments structurels plus importants du tiltrotor, dont la moitié sera également en titane et l'autre en acier.
Impression 3D en Russie et dans le monde
Malgré le fait que la production de type imprimante ait été mise en œuvre avec succès aux États-Unis et en Russie il y a plusieurs années, la création d'éléments pour équipements militaires est en cours de finalisation et de test. Tout d'abord, cela est dû aux exigences très élevées pour tous les produits militaires, principalement en termes de fiabilité et de durabilité. Cependant, les Américains ne sont pas les seuls à progresser dans ce domaine. Pour la deuxième année consécutive, les designers russes ont produit des pièces pour les fusils d'assaut et les pistolets développés en utilisant la technologie d'impression 3D. Les nouvelles technologies permettent de gagner un temps précieux de dessin. Et la mise en service de ces pièces peut permettre un remplacement rapide sur le terrain, dans les bataillons de réparation, puisqu'il n'y aura pas besoin d'attendre les pièces de rechange de l'usine pour les mêmes chars ou véhicules aériens sans pilote.
Pour les sous-mariniers, les imprimantes 3D militaires vaudront tout simplement leur pesant d'or, puisqu'en cas de navigation autonome au long cours, le remplacement des pièces par les sous-mariniers eux-mêmes donnera au sous-marin une ressource quasi inépuisable. Une situation similaire est observée avec les navires effectuant de longs voyages et les brise-glace. La plupart de ces navires recevront des drones dans un avenir très proche, qui nécessiteront éventuellement une réparation ou un remplacement complet. Si une imprimante 3D apparaît sur le navire, ce qui permettra d'imprimer rapidement des pièces détachées, alors dans quelques heures l'équipement pourra à nouveau être utilisé. Dans les conditions de la fugacité des opérations et de la grande mobilité du théâtre d'opérations militaires, l'assemblage local de certaines pièces, ensembles et mécanismes sur place permettra de maintenir un haut niveau d'efficacité des unités de soutien.
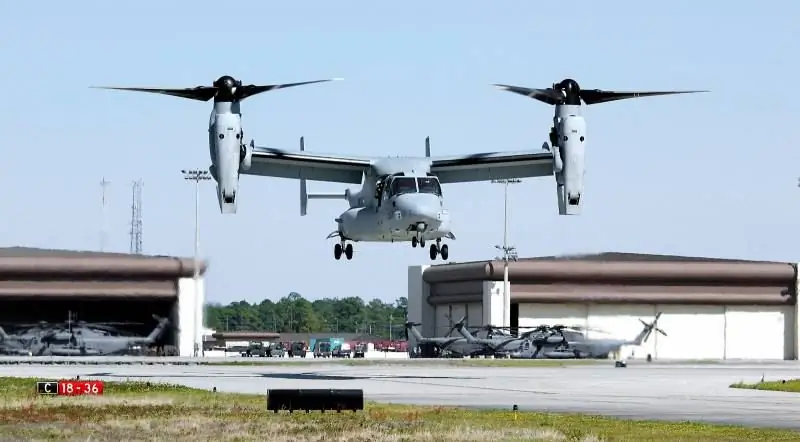
Balbuzard pêcheur MV-22
Alors que l'armée américaine lance ses avions convertis, les fabricants russes du char Armata utilisent une imprimante industrielle à Uralvagonzavod depuis déjà la deuxième année. Avec son aide, des pièces pour véhicules blindés, ainsi que des produits civils, sont produites. Mais jusqu'à présent, ces pièces ne sont utilisées que pour des prototypes, par exemple, elles ont été utilisées dans la création du char Armata et de ses tests. À la Kalachnikov Concern, ainsi qu'à TsNIITOCHMASH, sur ordre de l'armée russe, les concepteurs fabriquent diverses parties d'armes légères à partir de puces métalliques et polymères à l'aide d'imprimantes 3D. Le Tula Instrument Design Bureau, nommé d'après Shipunov, le célèbre CPB, connu pour un riche assortiment d'armes manufacturées: des pistolets aux missiles de haute précision, n'est pas en reste. Par exemple, un pistolet prometteur et un fusil d'assaut ADS, destinés à remplacer les forces spéciales AK74M et APS, sont assemblés à partir de pièces en plastique à haute résistance qui sont imprimées sur une imprimante. Pour certains produits militaires, le CPB a déjà pu réaliser des moules, actuellement l'assemblage en série des produits est en cours d'élaboration.
Dans les conditions où une nouvelle course aux armements est observée dans le monde, le moment de la sortie de nouveaux types d'armes devient important. Par exemple, dans les véhicules blindés, seul le processus de création d'un modèle et de transfert des dessins vers un prototype prend généralement un an ou deux. Lors du développement de sous-marins, cette période est déjà 2 fois plus longue. « La technologie d'impression 3D va réduire le délai de plusieurs fois à plusieurs mois », note Alexey Kondratyev, un expert dans le domaine de la marine. - Les concepteurs pourront gagner du temps sur les dessins lors de la conception d'un modèle 3D sur ordinateur et réaliser immédiatement un prototype de la pièce souhaitée. Très souvent, les pièces sont retravaillées en tenant compte des tests effectués et en cours de révision. Dans ce cas, vous pouvez libérer l'assemblage à la place de la pièce et vérifier toutes les caractéristiques mécaniques, comment les pièces interagissent les unes avec les autres. En fin de compte, le calendrier du prototypage permettra aux concepteurs de réduire le temps total nécessaire au premier échantillon fini pour entrer dans la phase de test. De nos jours, il faut environ 15 à 20 ans pour créer un sous-marin nucléaire de nouvelle génération: du croquis à la dernière vis lors de l'assemblage. Avec le développement ultérieur de l'impression tridimensionnelle industrielle et le lancement de la production en série de pièces de cette manière, le délai peut être réduit d'au moins 1,5 à 2 fois."
Selon les experts, les technologies modernes sont désormais à un à deux ans de la production en série de pièces en titane sur imprimantes 3D. On peut dire sans risque de se tromper que d'ici la fin de 2020, les représentants militaires des entreprises du complexe militaro-industriel accepteront des équipements qui seront assemblés à 30 à 50 % à l'aide des technologies d'impression 3D. Dans le même temps, la plus grande importance pour les scientifiques est la création de pièces en céramique sur une imprimante 3D, qui se distinguent par des propriétés de résistance élevée, de légèreté et de protection thermique. Ce matériau est très largement utilisé dans les industries spatiales et aéronautiques, mais il peut être utilisé dans des volumes encore plus importants. Par exemple, la création d'un moteur céramique sur une imprimante 3D ouvre l'horizon pour la création d'avions hypersoniques. Avec un tel moteur, un avion de ligne pourrait voler de Vladivostok à Berlin en quelques heures.
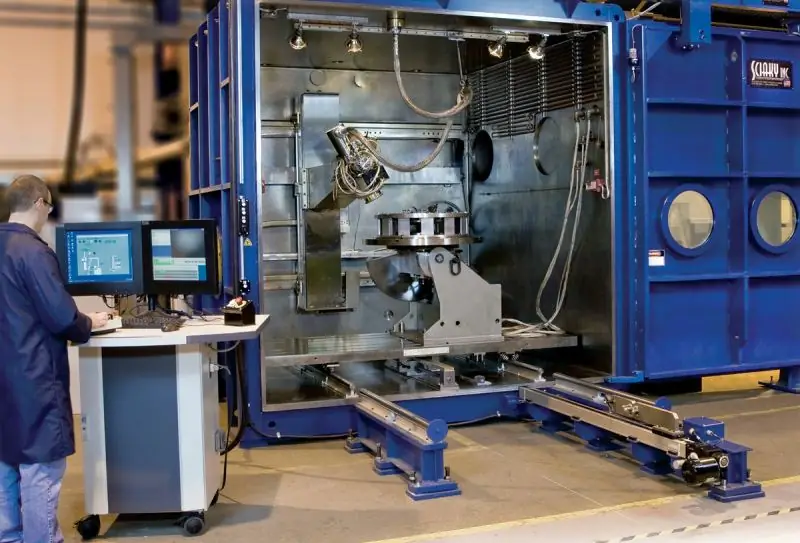
Il est également rapporté que des scientifiques américains ont inventé une formule de résine spécifiquement pour l'impression dans des imprimantes 3D. La valeur de cette formule réside dans la haute résistance des matériaux obtenus à partir de celle-ci. Par exemple, un tel matériau peut résister à des températures critiques supérieures à 1700 degrés Celsius, ce qui est dix fois supérieur à la résistance de nombreux matériaux modernes. Stephanie Tompkins, directrice scientifique pour Advanced Defense Research, estime que les nouveaux matériaux créés avec des imprimantes 3D auront des combinaisons uniques de caractéristiques et de propriétés jamais vues auparavant. Grâce à la nouvelle technologie, Tompkins affirme que nous serons en mesure de produire une pièce durable à la fois légère et énorme. Les scientifiques pensent que la production de pièces en céramique sur une imprimante 3D signifiera une percée scientifique, y compris dans la production de produits civils.
Le premier satellite 3D russe
Actuellement, la technologie d'impression 3D produit déjà avec succès des pièces directement à bord des stations spatiales. Mais les experts nationaux ont décidé d'aller encore plus loin, ils ont immédiatement décidé de créer un microsatellite à l'aide d'une imprimante 3D. La Rocket and Space Corporation Energia a créé un satellite, dont le corps, le support et un certain nombre d'autres pièces ont été imprimés en 3D. Dans le même temps, une précision importante est que le microsatellite a été créé par des ingénieurs d'Energia en collaboration avec des étudiants de l'Université polytechnique de Tomsk (TPU). Le premier satellite d'imprimante a reçu le nom complet "Tomsk-TPU-120" (le numéro 120 dans le nom en l'honneur du 120e anniversaire de l'université, qui a été célébré en mai 2016). Il a été lancé avec succès dans l'espace au printemps 2016 avec le vaisseau spatial Progress MS-02, le satellite a été livré à l'ISS puis lancé dans l'espace. Cette unité est le premier et le seul satellite 3D au monde.
Le satellite créé par les étudiants de TPU appartient à la classe des nanosatellites (CubSat). Il a les dimensions suivantes 300x100x100 mm. Ce satellite a été le premier vaisseau spatial au monde à avoir un corps imprimé en 3D. À l'avenir, cette technologie pourrait devenir une véritable percée dans la création de petits satellites, ainsi que rendre leur utilisation plus accessible et plus répandue. La conception du vaisseau spatial a été développée au centre scientifique et éducatif TPU "Modern Production Technologies". Les matériaux à partir desquels le satellite a été fabriqué ont été créés par des scientifiques de l'Université polytechnique de Tomsk et de l'Institut de physique de la force et de science des matériaux de la branche sibérienne de l'Académie des sciences de Russie. L'objectif principal du satellite était de tester les nouvelles technologies de la science des matériaux spatiaux; il aidera les scientifiques russes à tester plusieurs développements de l'université de Tomsk et de ses partenaires.
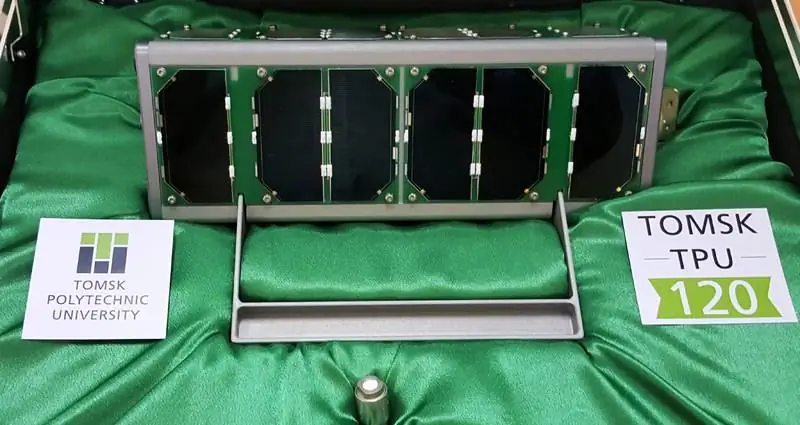
Selon le service de presse de l'université, le lancement du nanosatellite Tomsk-TPU-120 devait être effectué lors de la sortie dans l'espace depuis l'ISS. Le satellite est un vaisseau spatial assez compact, mais en même temps à part entière, équipé de batteries, de panneaux solaires, d'équipements radio embarqués et d'autres appareils. Mais sa principale caractéristique était que son corps était imprimé en 3D.
Divers capteurs du nanosatellite enregistreront la température à bord, sur les batteries et les cartes, et les paramètres des composants électroniques. Toutes ces informations seront ensuite transmises à la Terre en ligne. Sur la base de ces informations, les scientifiques russes pourront analyser l'état des matériaux du satellite et décider s'ils les utiliseront dans le développement et la construction d'engins spatiaux à l'avenir. Il convient de noter qu'un aspect important du développement des petits engins spatiaux est également la formation de nouveau personnel pour l'industrie. Aujourd'hui, les étudiants et les enseignants de l'Université polytechnique de Tomsk, de leurs propres mains, développent, fabriquent et améliorent la conception de toutes sortes de petits engins spatiaux, tout en acquérant non seulement des connaissances fondamentales de haute qualité, mais également les compétences pratiques nécessaires. C'est ce qui fait des diplômés de cet établissement d'enseignement des spécialistes uniques à l'avenir.
Les projets futurs des scientifiques et des représentants de l'industrie russes incluent la création d'un essaim de satellites universitaires. « Aujourd'hui, nous parlons de la nécessité de motiver nos étudiants à étudier tout ce qui, d'une manière ou d'une autre, est lié à l'espace - cela peut être l'énergie, les matériaux, la création de moteurs de nouvelle génération, etc. Nous avons discuté plus tôt que l'intérêt pour l'espace dans le pays s'est quelque peu estompé, mais il peut être ravivé. Pour ce faire, il faut partir non même pas d'un banc d'élève, mais d'un banc d'école. Ainsi, nous nous sommes engagés sur la voie du développement et de la production de CubeSat - de petits satellites », - note le service de presse de l'Institut polytechnique de Tomsk en référence au recteur de cet établissement d'enseignement supérieur, Peter Chubik.