Le fait de l'existence d'un bathyscaphe, qui a réussi à conquérir l'abîme le plus profond, témoigne de la possibilité technique de créer des véhicules habités pour plonger à n'importe quelle profondeur.
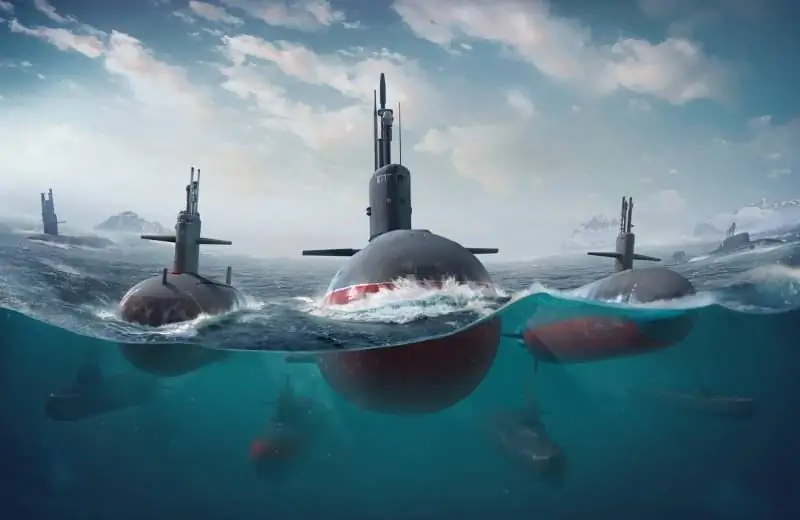
Pourquoi est-ce qu'aucun des sous-marins modernes n'est même près de pouvoir plonger - même à 1000 mètres ?
Il y a un demi-siècle, le bathyscaphe, assemblé à partir de moyens improvisés d'acier standard et de plexiglas, a atteint le fond de la fosse des Mariannes. Et je pourrais continuer ma plongée s'il y avait de grandes profondeurs dans la nature. La profondeur de conception de sécurité pour Trieste était de 13 kilomètres !
Plus des 3/4 de la superficie de l'Océan Mondial tombent sur la zone abyssale: un fond océanique à plus de 3000 m de profondeur, véritable espace opérationnel pour la flotte sous-marine ! Pourquoi personne ne profite de ces opportunités ?
La conquête des grandes profondeurs n'a rien à voir avec la solidité de la coque des "Sharks", "Boreyev" et "Virginia". Le problème est différent. Et l'exemple du bathyscaphe "Trieste" n'y est pour rien.
Ils sont similaires, comme un avion et un dirigeable
Bathyscaphe est un "flotteur". Wagon-citerne avec de l'essence, avec une nacelle d'équipage fixée en dessous. Lorsque les ballasts sont embarqués, la structure acquiert une flottabilité négative et s'enfonce en profondeur. Lorsque le ballast est lâché, il revient à la surface.
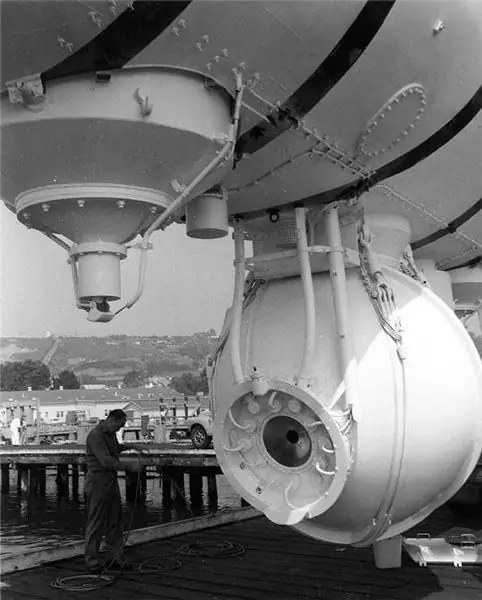
Contrairement aux bathyscaphes, les sous-marins doivent modifier à plusieurs reprises la profondeur d'immersion au cours d'une plongée. En d'autres termes, le sous-marin a la capacité de modifier à plusieurs reprises la réserve de flottabilité. Ceci est réalisé en remplissant les ballasts avec de l'eau de mer, qui est soufflée d'air lors de la remontée.
En règle générale, les bateaux utilisent trois systèmes d'air: l'air à haute pression (HPP), l'air à moyenne pression (HPA) et l'air à basse pression (HPP). Par exemple, sur les navires américains modernes à propulsion nucléaire, l'air comprimé est stocké dans des cylindres à 4 500 psi. pouce. Soit, humainement, environ 315 kg/cm2. Cependant, aucun des systèmes consommant de l'air comprimé n'utilise directement le VVD. Les chutes de pression soudaines provoquent un gel intense et un blocage des vannes, créant en même temps un danger d'explosions de compression des vapeurs d'huile dans le système. L'utilisation généralisée du VVD sous pression supérieure à 300 atm. créerait des risques inacceptables à bord du sous-marin.
Le VVD via un système de réducteurs de pression est fourni aux consommateurs sous forme de VVD sous une pression de 3000 lb. par m² pouce (environ 200 kg/cm2). C'est avec cet air que sont soufflés les ballasts principaux. Pour assurer le fonctionnement des autres mécanismes du bateau, le lancement des armes, ainsi que le soufflage des réservoirs d'assiette et d'égalisation, de l'air "de travail" est utilisé à une pression encore plus faible d'environ 100-150 kg / cm2.
Et c'est là que les lois du drame entrent en jeu !
Avec une plongée dans les profondeurs marines tous les 10 mètres, la pression augmente d'1 atmosphère
A une profondeur de 1500 m, la pression est de 150 atm. A 2000 m de profondeur, la pression est de 200 atm. Cela correspond exactement à la valeur maximale de l'IRR et de l'IRR dans les systèmes sous-marins.
La situation est aggravée par les volumes limités d'air comprimé à bord. Surtout après que le bateau a été sous l'eau pendant longtemps. A 50 mètres de profondeur, les réserves disponibles peuvent être suffisantes pour évacuer l'eau des ballasts, mais à 500 mètres de profondeur, cela ne suffit qu'à souffler à travers 1/5 de leur volume. Les grandes profondeurs sont toujours un risque, et il faut procéder avec la plus grande prudence.
De nos jours, il existe une possibilité pratique de créer un sous-marin avec une coque conçue pour une profondeur de plongée de 5000 mètres. Mais souffler les réservoirs à une telle profondeur nécessiterait de l'air sous une pression de plus de 500 atmosphères. Concevoir des canalisations, des vannes et des raccords conçus pour cette pression, tout en maintenant leur poids raisonnable et en éliminant tous les risques associés, est aujourd'hui une tâche techniquement insoluble.
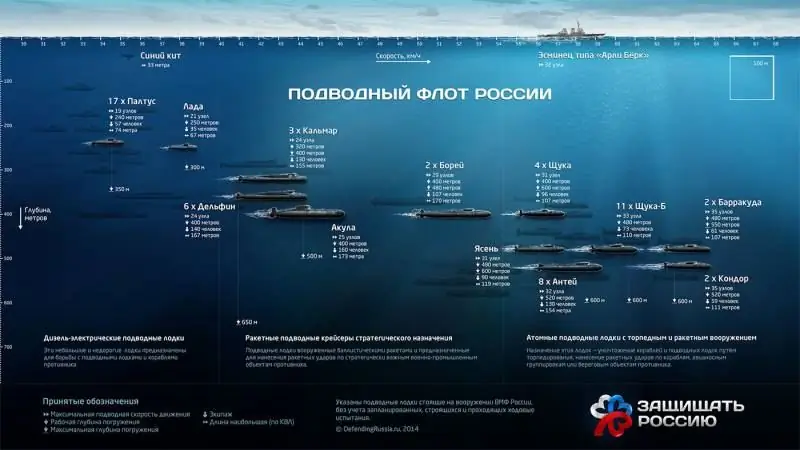
Les sous-marins modernes sont construits sur le principe d'un équilibre raisonnable des performances. Pourquoi construire une coque à haute résistance qui peut résister à la pression d'une colonne d'eau d'un kilomètre de long alors que les systèmes de surfaçage sont conçus pour des profondeurs beaucoup plus faibles ? Après avoir coulé un kilomètre, le sous-marin sera de toute façon voué à l'échec.
Cependant, cette histoire a ses propres héros et parias.
Les sous-mariniers américains sont considérés comme des outsiders traditionnels dans le domaine de la plongée sous-marine
Depuis un demi-siècle, les coques des bateaux américains sont constituées d'un seul alliage HY-80 aux caractéristiques très médiocres. Haut rendement-80 = alliage à haut rendement 80 000 psi pouce, ce qui correspond à la valeur de 550 MPa.
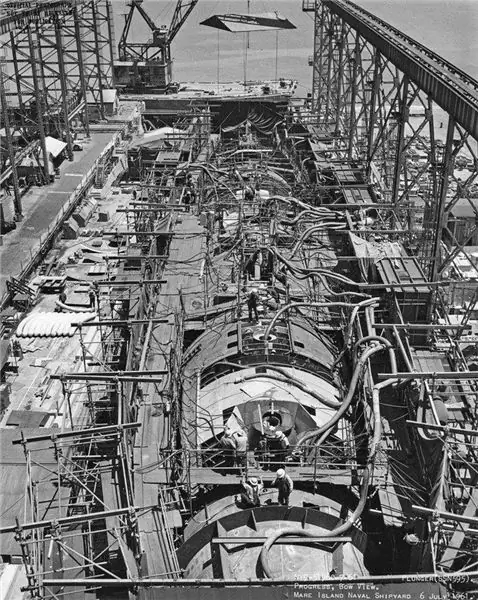
De nombreux experts expriment des doutes sur l'adéquation d'une telle solution. En raison de la faible coque, les bateaux ne sont pas en mesure d'exploiter pleinement les capacités des systèmes de remontée. Ce qui permet de souffler des réservoirs à des profondeurs beaucoup plus importantes. On estime que la profondeur de travail de submersion (la profondeur à laquelle le bateau peut se trouver longtemps, en effectuant des manœuvres) pour les sous-marins américains ne dépasse pas 400 mètres. La profondeur maximale est de 550 mètres.
L'utilisation du HY-80 permet de réduire le coût et d'accélérer l'assemblage des structures de coque; parmi les avantages, les bonnes qualités de soudage de cet acier ont toujours été citées.
Pour les ardents sceptiques, qui déclareront immédiatement que la flotte de "l'ennemi potentiel" est massivement reconstituée en déchets non combattables, il convient de noter ce qui suit. Ces différences de rythme de construction navale entre la Russie et les États-Unis ne sont pas tant dues à l'utilisation de nuances d'acier de meilleure qualité pour nos sous-marins qu'à d'autres circonstances. De toute façon.
À l'étranger, on a toujours cru que les super-héros n'étaient pas nécessaires. Les armes sous-marines doivent être aussi fiables, silencieuses et nombreuses que possible. Et il y a du vrai là-dedans.
Komsomolets
L'insaisissable "Mike" (K-278 selon la classification de l'OTAN) a établi un record absolu de profondeur de plongée parmi les sous-marins - 1027 mètres.
La profondeur d'immersion maximale des "Komsomolets" selon les calculs était de 1250 m.
Parmi les principales différences de conception, inhabituelles pour les autres sous-marins domestiques, il y a 10 réservoirs sans anneaux situés à l'intérieur d'une coque durable. Possibilité de tirer des torpilles depuis de grandes profondeurs (jusqu'à 800 mètres). Capsule de sauvetage escamotable. Et le point culminant principal est le système d'urgence pour le soufflage des réservoirs à l'aide de générateurs de gaz.
Le corps en alliage de titane a permis de réaliser tous les avantages inhérents.
Le titane lui-même n'était pas une panacée pour conquérir les profondeurs de la mer. L'essentiel dans la création des Komsomolets en eau profonde était la qualité de construction et la forme d'une coque solide avec un minimum de trous et de points faibles.
L'alliage de titane 48-T avec une limite d'élasticité de 720 MPa n'était que légèrement supérieur en résistance à l'acier de construction HY-100 (690 MPa), à partir duquel les sous-marins SeaWolf ont été fabriqués.
Les autres "avantages" décrits du boîtier en titane sous la forme de faibles propriétés magnétiques et de sa moindre sensibilité à la corrosion ne valaient pas en eux-mêmes l'investissement. La magnétométrie n'a jamais été une méthode prioritaire pour détecter les bateaux; sous l'eau, tout est décidé par l'acoustique. Et le problème de la corrosion marine est résolu depuis deux cents ans par des méthodes plus simples.
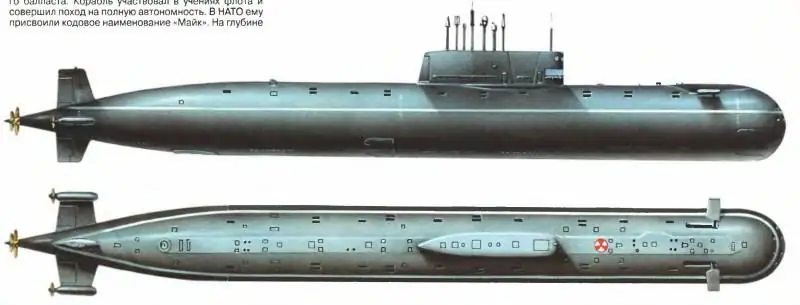
Le titane du point de vue de la construction navale de sous-marins domestiques présentait DEUX avantages réels:
a) moins de densité, ce qui signifiait un corps plus léger. Les réserves émergentes ont été dépensées pour d'autres postes de charge, par exemple des centrales électriques de plus grande puissance. Ce n'est pas un hasard si des sous-marins à coque en titane (705 (K) "Lira", 661 "Anchar", "Condor" et "Barracuda") ont été construits en conquérants de la vitesse.;
b) Parmi tous les aciers et alliages à haute résistance l'alliage de titane 48-T s'est avéré être le plus avancé technologiquement dans le traitement et l'assemblage des structures de coque.
"Le plus avancé technologiquement" ne veut pas dire simple. Mais les qualités de soudage du titane permettaient au moins l'assemblage de structures.
L'outre-mer avait une vision plus optimiste de l'utilisation des aciers. Pour la fabrication des coques des nouveaux sous-marins du XXIe siècle, l'acier à haute résistance de la marque HY-100 a été proposé. En 1989, les États-Unis ont jeté les bases du leader SeaWolfe. Après deux ans, l'optimisme s'est estompé. La coque du SeaWolfe a dû être démontée et repartie à zéro.
De nombreux problèmes ont maintenant été résolus et les alliages d'acier ayant des propriétés équivalentes à celles du HY-100 trouvent des applications plus larges dans la construction navale. Selon certains rapports, un tel acier (WL = Werkstoff Leistungsblatt 1.3964) est utilisé dans la fabrication d'une coque durable de sous-marins allemands non nucléaires "Type 214".
Il existe des alliages encore plus résistants pour la construction de boîtiers, par exemple l'alliage d'acier HY-130 (900 MPa). Mais en raison des mauvaises propriétés de soudage, les constructeurs navals considéraient l'utilisation du HY-130 impossible.
Pas encore de nouvelles du Japon.
signifie limite d'élasticité
Comme le dit le vieil adage, "Quoi que vous fassiez bien, il y a toujours un Asiatique qui le fait mieux."
Il y a très peu d'informations dans les sources ouvertes sur les caractéristiques des navires de guerre japonais. Cependant, les experts ne sont pas arrêtés par la barrière de la langue ou le secret paranoïaque inhérent à la deuxième marine la plus puissante du monde.
D'après les informations disponibles, il s'ensuit que les samouraïs, ainsi que les hiéroglyphes, utilisent largement les désignations anglaises. Dans la description des sous-marins, il y a une abréviation NS (Naval Steel - naval steel), associée à des indices numériques 80 ou 110.
Dans le système métrique, "80" lors de la désignation d'une nuance d'acier signifie très probablement une limite d'élasticité de 800 MPa. L'acier plus résistant NS110 a une limite d'élasticité de 1100 MPa.
Du point de vue américain, l'acier standard des sous-marins japonais est le HY-114. Mieux et plus durable - HY-156.
Scène muette
"Kawasaki" et "Mitsubishi Heavy Industries" sans aucune promesse bruyante et "Poseidons" ont appris à fabriquer des coques à partir de matériaux qui étaient auparavant considérés comme incompatibles et impossibles dans la construction de sous-marins.
Les données fournies correspondent à des sous-marins obsolètes avec une installation indépendante de l'air du type "Oyashio". La flotte est composée de 11 unités, dont les deux plus anciennes, entrées en service en 1998-1999, ont été transférées dans la catégorie des unités de formation.
"Oyashio" a un design mixte à double coque. L'hypothèse la plus logique est que la section centrale (coque solide) est constituée de l'acier le plus durable NS110, une conception à double coque est utilisée à la proue et à la poupe du bateau: une coque légère et profilée en NS80 (pression à l'intérieur = à l'extérieur pression), recouvrant les ballasts principaux à l'extérieur de la coque solide. …
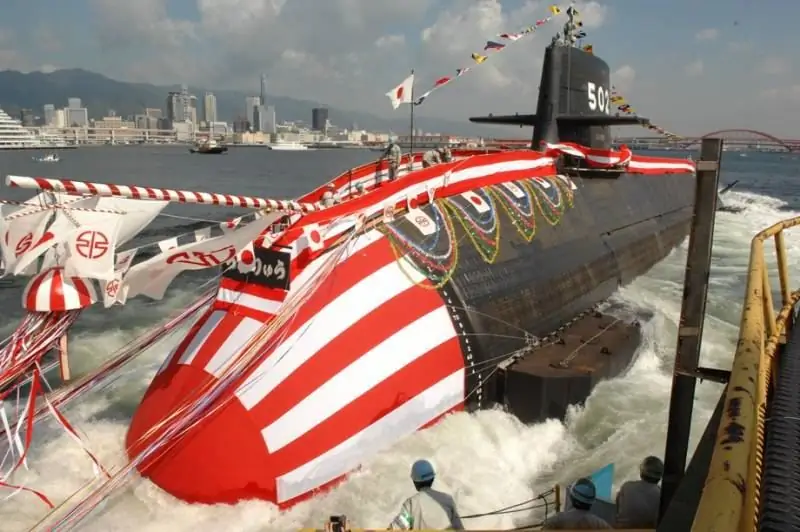
Les sous-marins japonais modernes de type "Soryu" sont considérés comme des "Oyashio" améliorés tout en conservant les solutions de conception de base héritées de leurs prédécesseurs.
Avec sa robuste coque en acier NS110, la profondeur de travail du Soryu est estimée à au moins 600 mètres. La limite est de 900.
Compte tenu des circonstances présentées, les Forces d'autodéfense japonaises disposent actuellement de la flotte de sous-marins de combat la plus importante.
Les japonais "pressent" tout ce qui est disponible. Une autre question est de savoir dans quelle mesure cela aidera dans un conflit naval. Pour la confrontation dans les profondeurs de la mer, une centrale nucléaire est nécessaire. Le pitoyable "demi-mesures" japonais en augmentant la profondeur de travail ou en créant un "bateau à piles" (le sous-marin Oryu qui a surpris le monde) ressemble à un bon visage pour un mauvais jeu.
D'un autre côté, l'attention traditionnelle aux détails a toujours permis aux Japonais d'avoir un avantage sur l'ennemi. L'émergence d'une centrale nucléaire pour la marine japonaise est une question de temps. Mais qui d'autre dans le monde possède des technologies pour fabriquer des boîtiers ultra-résistants en acier avec une limite d'élasticité de 1100 MPa ?