La guerre est connue pour être le meilleur moteur du progrès. L'industrie des chars de l'Union soviétique a fait un saut qualitatif vertigineux en quelques années de guerre seulement. La véritable couronne était les chars de la série IS.
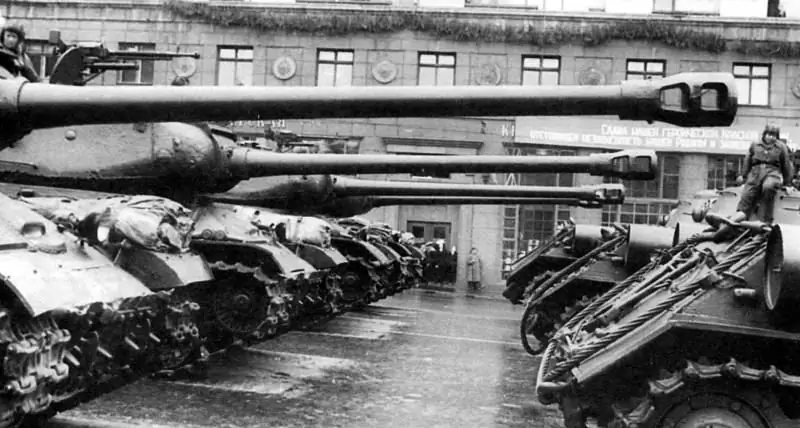
Recettes de Magnitogorsk
Dans la partie précédente de l'histoire, il s'agissait du blindage coulé de haute dureté 70L utilisé pour les tourelles des chars IS. Les développeurs d'armures de TsNII-48 étaient loin d'être la première expérience dans la création de protections pour les chars lourds.
Avant le Kursk Bulge, qui est devenu un catalyseur pour le développement de la construction de chars lourds domestiques, le principal objet de la modernisation était le char KV. Initialement, tous les travaux visaient à réduire la proportion d'additifs d'alliage rares dans la composition de l'armure. Même le nom de TsNII-48 en a trouvé un approprié - un acier économiquement allié. Le blindage d'origine de la marque FD-7954, avec lequel le char KV est entré dans la Grande Guerre patriotique, contenait, selon les exigences techniques, jusqu'à 0,45% de molybdène, 2,7% de nickel et de chrome.
À la fin de 1941, un groupe de chercheurs dirigé par Andrei Sergeevich Zavyalov de l'Institut blindé a créé une recette pour l'acier FD-6633 ou 49C, dans laquelle le molybdène ne nécessitait pas plus de 0,3%, le chrome - jusqu'à 2,3% et le nickel - jusqu'à 1, 5%. Considérant que les chars de la série KV de la seconde moitié de 1941 à 1943 ont été collectés à environ 4 000 exemplaires, on peut imaginer le montant des économies réelles en métaux d'alliage.
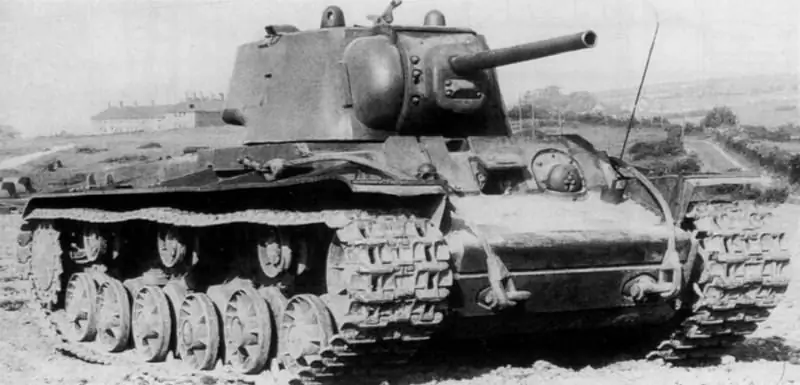
Le secret du succès
Le secret du succès des métallurgistes réside dans l'étude des paramètres de formation de la fracture fibreuse des armures - paramètre principal de la résistance des projectiles. Il s'est avéré que vous pouvez vous passer d'une proportion importante d'éléments d'alliage en modifiant simplement la vitesse de refroidissement de l'armure lors de la trempe. Mais c'est simple en mots - combien d'expériences préliminaires et de fontes les métallurgistes ont dû faire, seules les archives désormais classées pourront le dire.
À l'usine métallurgique de Magnitogorsk en 1941, les premiers prototypes d'acier 49C ont été obtenus, qui n'étaient pas inférieurs à l'armure traditionnelle "d'avant-guerre". En particulier, le bombardement du canon de 76 mm a montré une pleine conformité avec les exigences tactiques du char. Et depuis 1942, seule une armure portant le nom 49C était utilisée pour la série KV. Il convient de rappeler que la consommation de chrome, de molybdène et de nickel a considérablement diminué.
La recherche de nouvelles formulations de blindage pour l'équipement lourd ne s'est pas arrêtée là. En 1942, l'acier GD-63-3 a été « soudé », complètement dépourvu de chrome et de nickel rares. Dans une certaine mesure, le nickel a été remplacé par le manganèse - sa part a été multipliée par plus de trois (jusqu'à 1,43%). Des prototypes de la nouvelle armure ont été tirés. Et ils se sont avérés tout à fait adaptés à une utilisation de masse dans la conception du KV. Mais les chars Klim Voroshilov avec un blindage de dureté moyenne se retiraient. Et la place des véhicules lourds a été prise par des véhicules «Joseph Staline» avec un blindage de haute dureté.
Armure roulée 51C
Si le blindage 70L de la tourelle IS-2 pouvait être coulé, alors cette astuce ne fonctionnait pas avec les parties de la coque du char. Ici, les ingénieurs ont été confrontés à deux problèmes à la fois - la création d'une armure de haute dureté et de grande épaisseur et la nécessité de la souder dans une coque finie.
Tous ceux qui sont intéressés sont probablement déjà au courant des problèmes causés par le soudage de l'armure T-34 - il existe une forte probabilité de fissuration dans la zone des soudures. L'IS-2 n'a pas fait exception. Et son corps était à l'origine censé être cuit à partir de pièces finalement traitées thermiquement.
Réalisant les difficultés et les dangers qu'une telle solution technologique apporterait dans une opération militaire, les spécialistes du TsNII-48 ont modifié le cycle de production des chars. En conséquence, en 1943, à l'usine de construction de machines lourdes de l'Oural et à l'usine n° 200 de Tcheliabinsk, il a été décidé que la coque de l'IS-2 était cuite à partir de plaques de blindage qui n'avaient passé que des vacances élevées après avoir roulé. C'est, en fait, la coque d'un char lourd a été assemblée à partir d'acier "brut". Cela a considérablement réduit les défauts de soudage sur l'armure laminée à haute dureté 51C.
Le traitement thermique final par chauffage avant trempe était déjà réalisé sur le corps soudé de la cuve, l'ayant préalablement renforcé avec des entretoises internes. Le corps a été maintenu au four pendant trois heures. Et puis, sur des appareils spéciaux, ils ont été transférés dans un réservoir de trempe à l'eau et y ont été conservés pendant 15 minutes. De plus, la température de l'eau dans la cuve de trempe est passée de 30 à 55°C. La température de surface du corps après avoir été retiré de l'eau était de 100 à 150 ° C. Et ce n'est pas tout.
Après la trempe, le corps a été immédiatement soumis à un faible revenu dans un four à circulation à une température de 280 à 320 ° C avec maintien après avoir atteint cette température pendant 10 à 12 heures. La faible trempe des tours coulées à partir d'armures 70L a été réalisée de manière similaire. Fait intéressant, le contrôle des fissures dans les coques expérimentales IS-2 a duré quatre mois, lorsque les premiers réservoirs de production ont quitté les portes de l'usine.
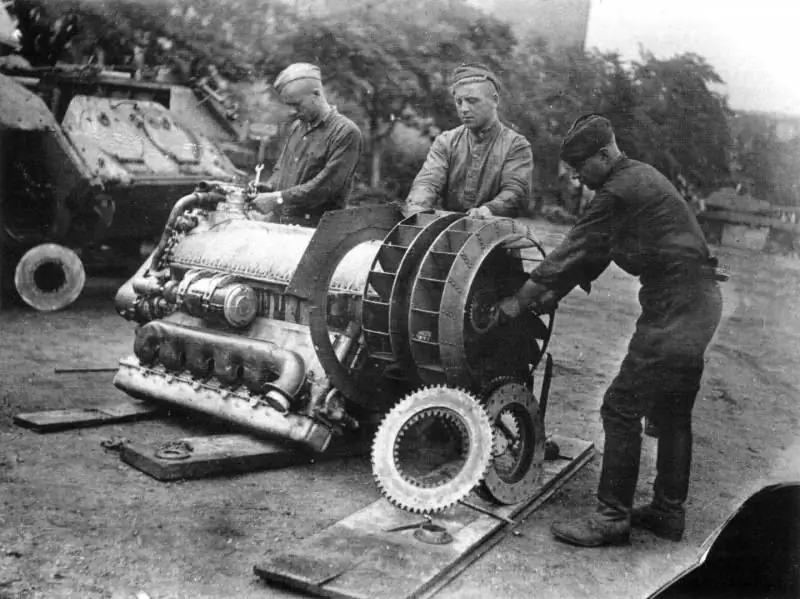
Composition chimique
Quel était le blindage laminé 51C qui est devenu le principal pour les IS-2, ISU-122 et ISU-152 ? Il s'agit d'un acier à durcissement profond pour de fortes épaisseurs d'armures avec la composition chimique suivante (%):
C 0, 18-0, 24
Mn 0, 70-1, 0
Si 1, 20-1, 60
Cr 1, 0-1, 5
Ni 3.0-3.8
Lu 0, 20-0, 40
P 0,035
S 0,035.
Par rapport à l'armure coulée 70L, l'acier laminé 51C avait une proportion plus élevée de molybdène et de nickel, ce qui garantissait une augmentation de la trempabilité jusqu'à 200 mm. Lorsque les coques des chars lourds ont été tirées avec des obus de 88 mm, il s'est avéré que le blindage de haute dureté était bien supérieur en termes de durabilité à ses prédécesseurs de dureté moyenne. Le problème du placement de l'armure enroulée 51C a été résolu immédiatement.
Soudage intelligent
Une contribution importante au succès du développement de la production de blindage des chars de la série IS a été apportée par le soudage automatique de l'acier sous une couche de flux. Comme il était impossible de transférer l'ensemble du processus de fabrication d'une coque blindée de char à une telle soudure au début de 1944, les ingénieurs se sont concentrés sur l'automatisation des coutures les plus étendues et les plus chargées mécaniquement.
À l'usine n° 200 de Chelyabinsk, en cours d'assemblage de la coque du char lourd IS-2, seulement 25 % de toutes les soudures ont pu être automatisées. À la mi-1944, Tankograd était capable d'automatiser 18% de tous les 25% possibles des soudures. La longueur totale des soudures le long de la coque du char lourd IS-2 était de 410 mètres courants, dont 80 mètres courants ont été réalisés par la méthode de soudage automatisé.
Ce résultat a permis de réaliser d'importantes économies de ressources rares et d'électricité. Il a été possible de libérer jusqu'à 50 soudeurs manuels qualifiés (leurs coûts de main-d'œuvre s'élevant à 15 400 heures-homme) et d'économiser 48 000 kilowattheures d'électricité. Diminution de la consommation d'électrodes (environ 20 000 kg, austénitique - 6 000 kg), d'oxygène (de 1 440 mètres cubes).
Le temps consacré au soudage a également été considérablement réduit. Par exemple, le soudage du fond et du boîtier de la tourelle sur les côtés avec une couture de seize mètres a pris 9,5 heures-homme en mode manuel, et seulement 2. Une couture de longueur similaire reliant le fond aux côtés de la coque du réservoir en mode automatique était requise 3 heures-homme (en manuel immédiatement 11, 4). Dans le même temps, les soudeurs hautement qualifiés pourraient être remplacés par des ouvriers non qualifiés en soudage automatique.
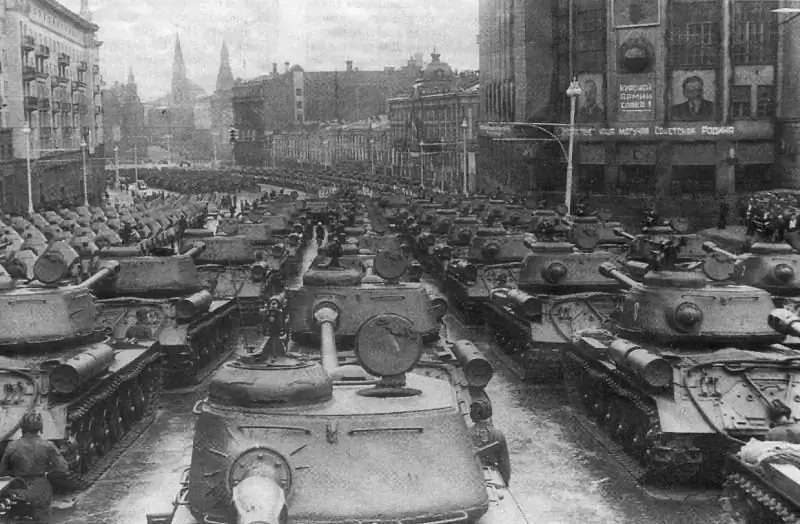
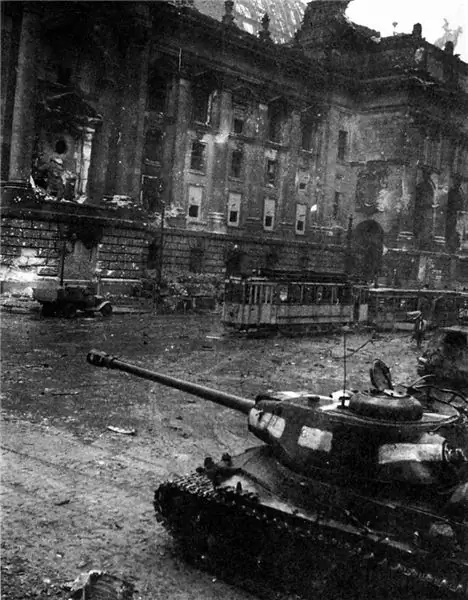
SAG de l'Oural
Chercheur de l'industrie des chars soviétiques, candidat aux sciences historiques Zapariy Vasily Vladimirovich de l'Institut d'histoire et d'archéologie de la branche de l'Oural de l'Académie des sciences de Russie dans l'un de ses ouvrages décrit en détail les unités de soudage automatique utilisées dans l'Oural pour les blindés fabrication de coque.
Le plus répandu était un fusil d'assaut de type "ACC" à tête Bushtedt. Il y avait huit installations de ce type à Uralmash. La vitesse d'alimentation du fil dans cette machine dépendait de la tension dans l'arc. Il nécessitait 5 unités, dont 3 moteurs électriques cinématiques et 1 moteur-générateur.
Au milieu de 1943, la machine à souder SA-1000 a été conçue pour les besoins des chars lourds IS-2. Ou une machine à souder d'une capacité jusqu'à 1000 A.
Afin de maîtriser la production de coques blindées pour le nouveau char lourd Tcheliabinsk IS-3, les ingénieurs de l'usine ont conçu en 1944 l'appareil "SG-2000". Cette machine a été conçue pour travailler avec des fils de soudure à faible teneur en carbone et de diamètre accru (6 à 8 mm) et a trouvé son application dans la fabrication de la tour IS-3. L'installation disposait d'un distributeur permettant d'introduire une composition spéciale (ferroalliages divers) dans la section de soudure afin de désoxyder (restaurer) le métal qu'elle contenait. Au total, sur le principe d'autorégulation de l'arc de soudage à l'UZTM, en 1945, 9 installations de soudage automatique de trois types ont été créées: "SA-1000", "SG-2000", "SAG" ("Soudage automatique diriger").
Plus belle qu'une armure allemande
Le résultat de toute l'histoire avec le blindage des chars lourds de l'IS a été le développement étonnamment rapide d'une recette d'acier qui surpassait le blindage allemand dans ses propriétés tactiques. TsNII-48 a reçu un acier durcissable de 120 mm, dont l'épaisseur, si nécessaire, pouvait être augmentée à 200 mm.
C'est devenu le fondement principal du développement de la famille des chars lourds soviétiques d'après-guerre.