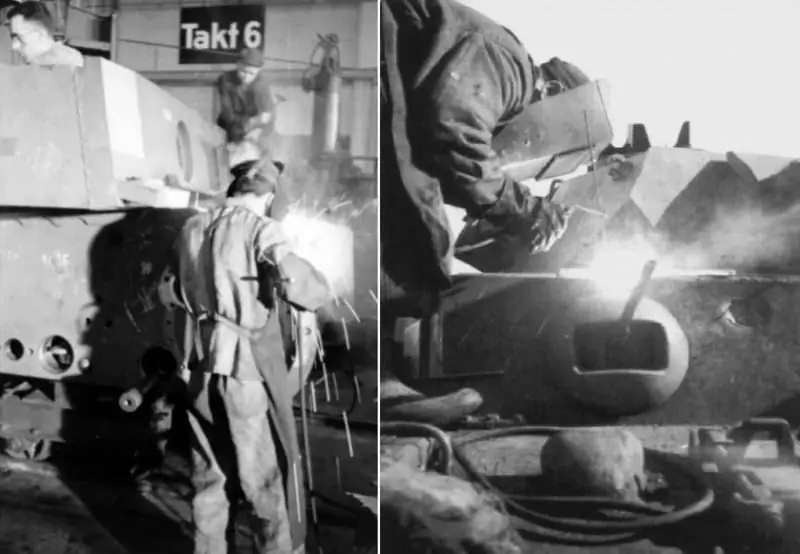
Approche allemande
Dans la première partie du matériel sur les technologies de soudage pendant la Grande Guerre patriotique, il a été mentionné que l'une des principales réalisations des technologues et scientifiques soviétiques était l'introduction de l'automatisation du soudage des coques et des tours de réservoir. Dans l'Allemagne nazie, le soudage automatique n'était pas utilisé dans les usines de chars. Il y avait une explication très importante à cela - pendant la principale période de la guerre, l'industrie des chars du Troisième Reich n'a pas connu de pénurie de main-d'œuvre hautement qualifiée, y compris des soudeurs. Et en Union soviétique, lors de l'évacuation de grandes entreprises vers l'est, du personnel précieux pour l'industrie a été perdu, ce qui a compromis non seulement la qualité de l'assemblage des chars, mais même la possibilité même de la production. En Allemagne, il en est venu au point que lors du soudage des coques des "Panthers" et des "Tigres", les soudeurs individuels étaient affectés à des coutures séparées! L'ingénieur V. V. Ardentov écrit à ce sujet dans le document "Expérience allemande dans la coupe de blindages et le soudage de coques de chars" dans le "Bulletin de l'industrie des chars" de l'année victorieuse 1945. Son travail était basé sur l'étude de deux usines de coques blindées à Kirchmeser et Brandenburg. De toute évidence, ces usines pouvaient s'offrir un tel luxe technologique sous la forme de soudeurs séparés pour des coutures séparées jusqu'aux derniers mois de la guerre.
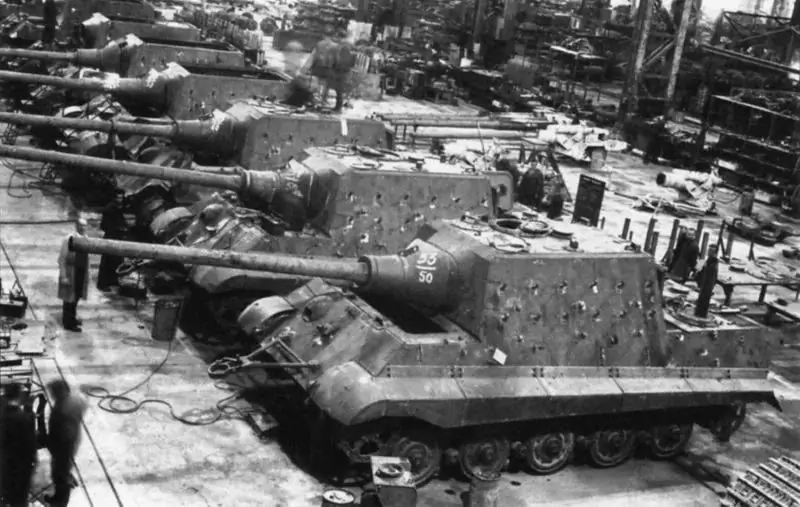
Avant de souder les coques, les plaques de blindage étaient découpées, ce qui jusqu'en 1942 était réalisé mécaniquement. Pour découper les plaques de blindage pour les connexions épine dans épine, il était beaucoup plus pratique d'utiliser la coupe acétylène-oxygène, qui était également utilisée dans des situations similaires dans l'industrie des chars soviétiques. Ici, les Allemands étaient en avance sur nos constructeurs de chars à la fois en efficacité et en qualité de coupe. Ceci est en grande partie le résultat de l'utilisation d'outils de haute qualité (machines de découpe au gaz Messer et Grisheim) avec la possibilité d'affiner l'épaisseur de la plaque de blindage. En outre, les Allemands utilisaient de l'oxygène d'un degré élevé de purification - plus de 99%. Enfin, au cours de la découpe de l'armure, les Allemands ont utilisé plusieurs torches, notamment pour le chanfreinage. Le processus d'oxycoupage lui-même était automatisé, ce qui a permis d'accélérer le processus et de le rendre beaucoup plus précis.
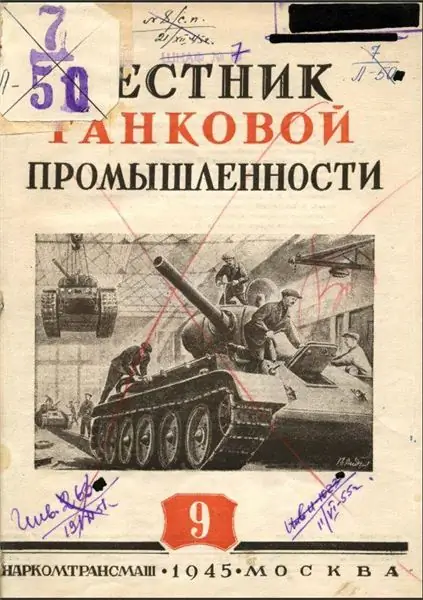
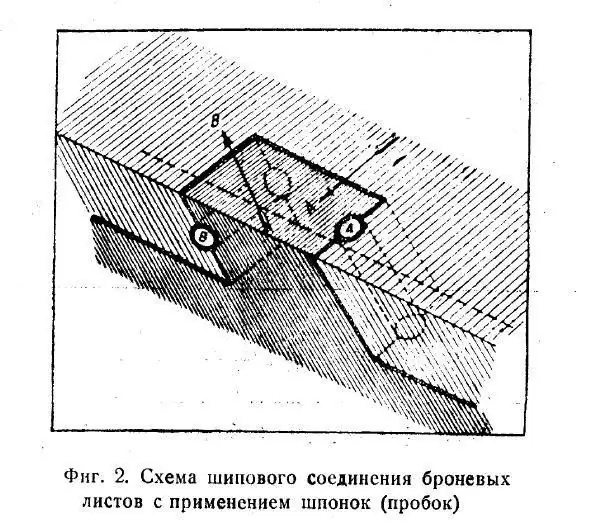
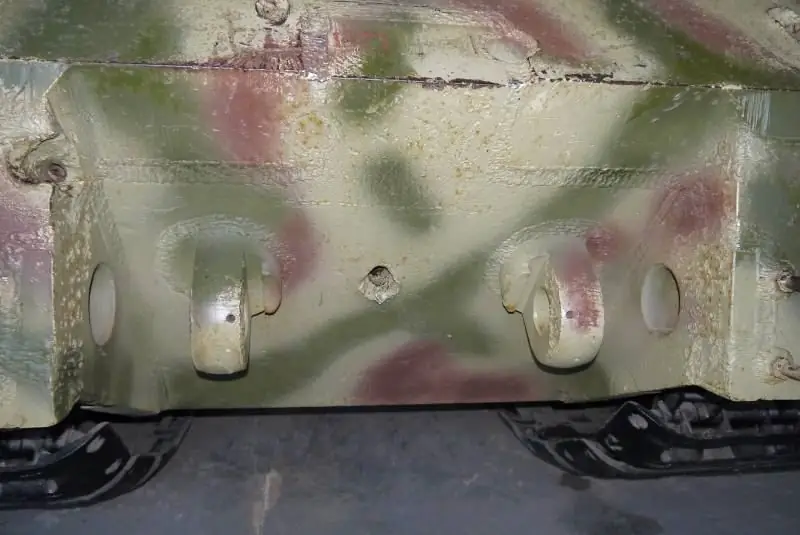
[centre]
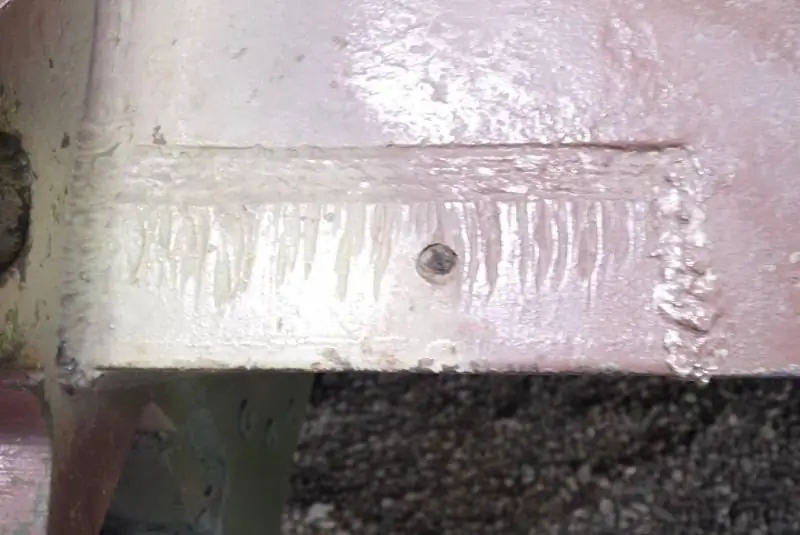
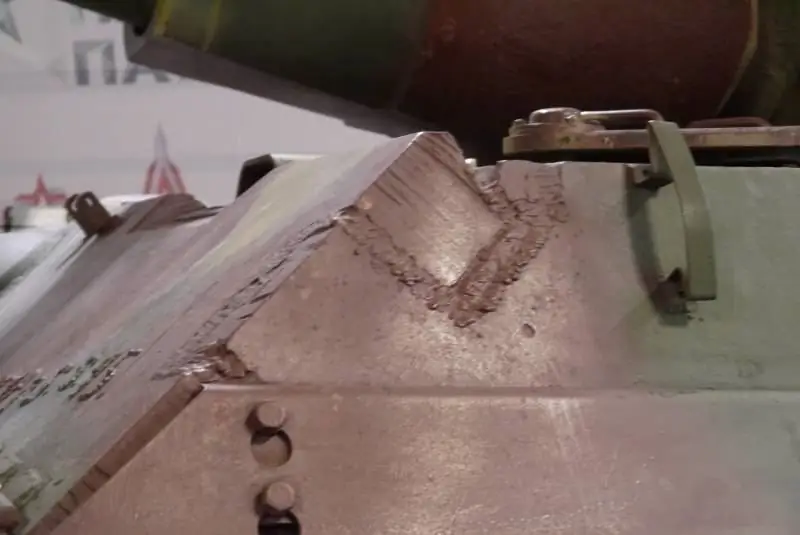
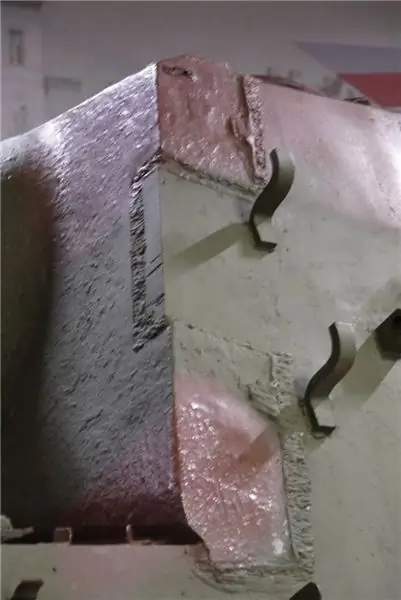
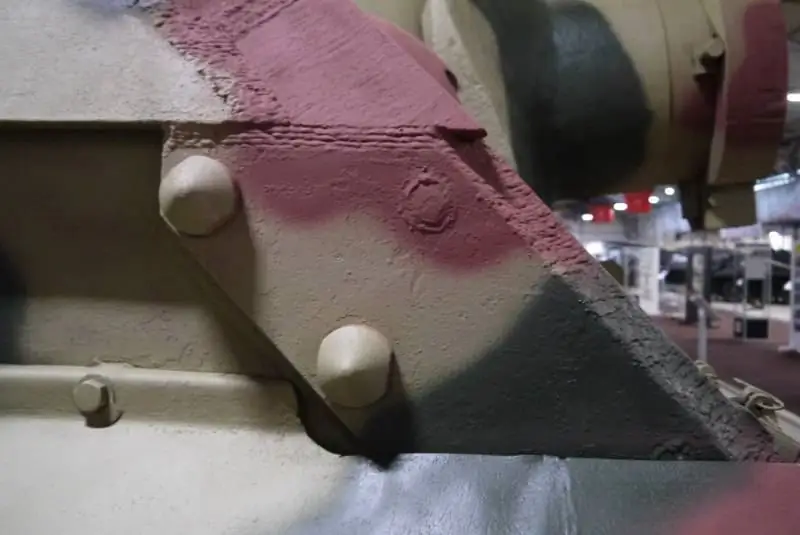
[/centre]
Comme vous le savez, l'une des caractéristiques distinctives des coques des chars allemands de 1942 était la connexion à pointes des plaques de blindage avec une pointe rectangulaire ou oblique. Dans le même temps, les Allemands ne se limitaient pas à une simple articulation - de plus, pour plus de solidité, des clés cylindriques ou des bouchons étaient introduits dans les articulations. En particulier, cela était courant sur les chars moyens "Panther", les canons automoteurs "Ferdinand", les tours de lourds "Tigers" et quelques corps de "Maus". De tels bouchons étaient des rouleaux d'acier jusqu'à 80 mm de diamètre insérés dans les joints des tôles à assembler après avoir été assemblés pour le soudage. Les bouchons ont été placés dans le plan des bords de la pointe des plaques de blindage - une paire d'entre eux était nécessaire pour chaque joint. En fait, après l'installation des clés, la connexion à pointe est devenue monobloc avant même le soudage. Dans ce cas, les goujons ont été montés au ras de la surface avec l'armure et soudés le long du périmètre de la base. La connexion par pointes des plaques de blindage des coques de chars a nettement amélioré la protection balistique à la fois des soudures et du blindage. Tout d'abord, cela a été assuré en augmentant la longueur totale de la soudure, constituée de segments séparés, ce qui a quelque peu réduit la propagation des fissures.
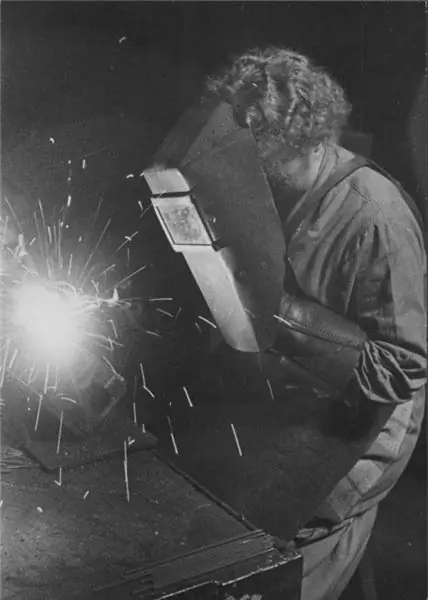
L'un des problèmes dans la fabrication des coques des chars allemands était la fabrication de découpes et de trous (par exemple, pour les joints de blindage mentionnés ci-dessus). Il était impossible de les couper avec du gaz, donc le forage a été utilisé. Initialement, pour les aciers des nuances E-18 et E-19, qui ont subi la procédure de durcissement superficiel, il était généralement impossible de trouver un foret adapté tant la couche externe de l'armure s'est avérée si dure. Dans le cas du perçage d'un trou avant la trempe, une trempe inégale s'est formée dans la zone du trou, suivie d'une déformation et d'une fissuration radiale. Oui, et il y avait des fissures sur les chars allemands, et des fissures considérables, et les efforts allemands pour les éviter seront discutés plus tard. En partie, le problème du durcissement inégal de l'armure dans la zone des trous a été résolu par une pâte réfractaire spéciale, qui a été utilisée pour couvrir les trous avant d'être envoyée au four. Mais, encore une fois, cela n'a résolu que partiellement le problème. Ce n'est qu'à la fin de 1944 à l'Institut électrothermique d'Essen que ce problème a été résolu par une procédure de trempe locale sur la zone durcie de l'armure. L'unité, développée par les Allemands, est décrite dans son article par le lauréat du prix Staline, candidat des sciences techniques A. A. Shmykov. Le matériel a été publié dans l'édition spécialisée "Bulletin of Tank Industry", qui était secrète pour l'époque et qui nous était familière, à la fin de 1945. Dans les années d'après-guerre, les pages du Vestnik étaient riches en analyses détaillées des astuces d'ingénierie des ingénieurs allemands, car il y avait suffisamment d'équipement capturé.
Mais revenons à la libération locale de l'armure où les trous ont été percés. La base de l'unité était une électrode en graphite connectée au site de forage, à travers laquelle passait un courant électrique de 220 ampères et une tension de 380 volts. En conséquence, l'armure a été chauffée à la température de revenu. Selon l'épaisseur de l'armure et le diamètre du trou, cela prenait de 7 à 15 minutes. Après la procédure de trempe, la dureté de l'armure a diminué de 2 à 2,5 fois. Il est à noter que l'industrie nationale (y compris l'industrie des réservoirs) utilisait également la trempe de l'acier par chauffage par courant - le "savoir-faire" des Allemands résidait uniquement dans l'utilisation d'une électrode en graphite.
Allemands et électrodes
Les Allemands ont également utilisé les vacances pour souder des feuilles de leur armure à haute dureté avec une teneur en carbone comprise entre 0,40 et 0,48%. Cela est devenu connu des spécialistes du TsNII-48 (Institut blindé) pendant la guerre, lorsque les ingénieurs métallurgistes cherchaient des recettes pour réduire la fissuration du blindage du T-34. En fin de compte, les Allemands ont libéré les plaques de blindage à des températures de 500-600 degrés (vacances élevées), puis ont soudé le blindage préchauffé à 150-200 degrés en plusieurs passes. Les soudeurs n'utilisaient pas d'électrodes d'un diamètre supérieur à 5 mm - difficile à croire, compte tenu de l'épaisseur du blindage des chars allemands. Les électrodes d'un diamètre de 4 mm ont fonctionné à un courant de 120-140 ampères, avec un diamètre de 5-6 mm - 140-160 ampères. Cette technologie a permis de ne pas surchauffer la zone de soudure. Cela signifie qu'une zone de durcissement et de revenu plus petite a été obtenue. De plus, après le soudage, le joint s'est refroidi très lentement - tout cela a finalement permis aux Allemands de traiter avec plus ou moins de succès les fissures aux endroits des joints soudés. De plus, des électrodes austénitiques ont été principalement utilisées, ce qui a conduit à une ductilité élevée de la soudure et à sa transition prolongée vers un état martensitique fragile. Les ingénieurs du TsNII-48 ont étudié très attentivement les caractéristiques du cycle technologique du soudage des blindages des chars, ce qui a permis de transférer avec succès ces techniques au cycle de production du T-34. Naturellement, personne dans l'industrie des chars ne pouvait se permettre une application multicouche aussi minutieuse de soudures sur toute la coque du char, le "savoir-faire" allemand n'était utilisé que dans les coutures les plus critiques sujettes à la fissuration.
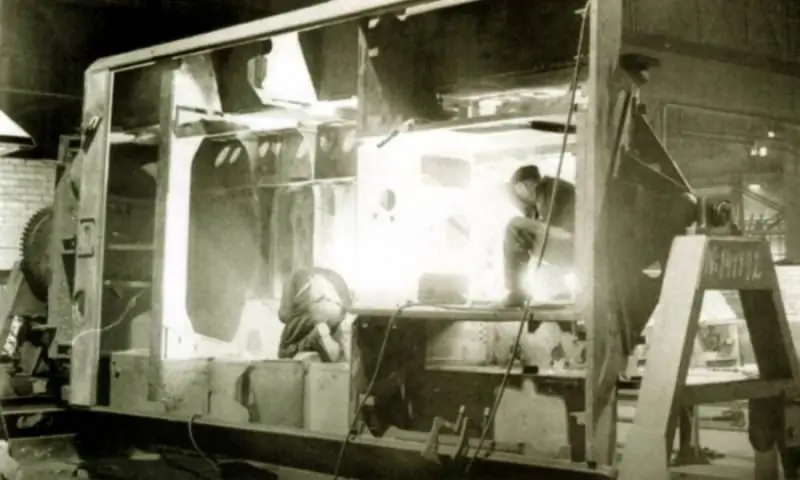
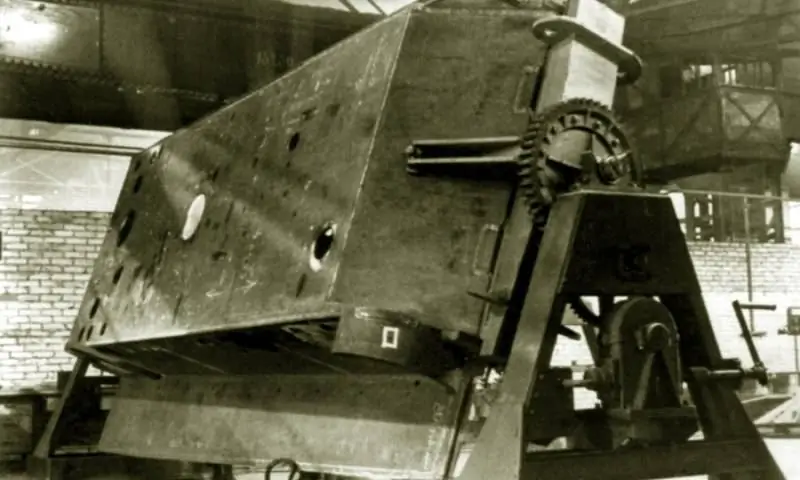
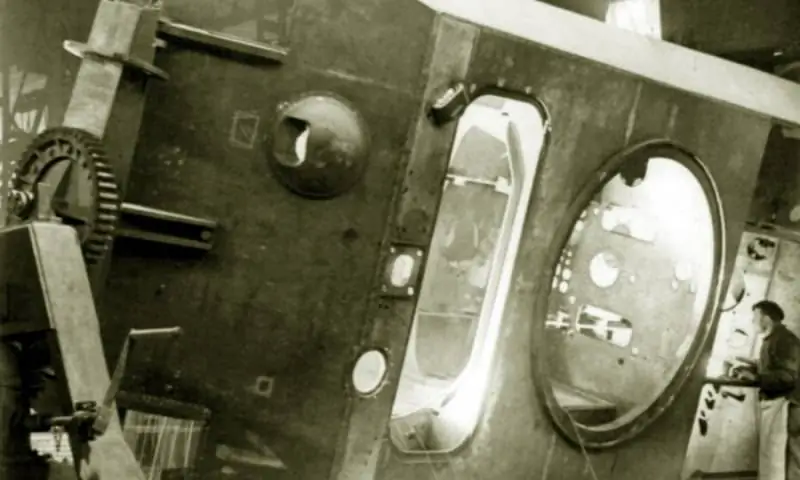
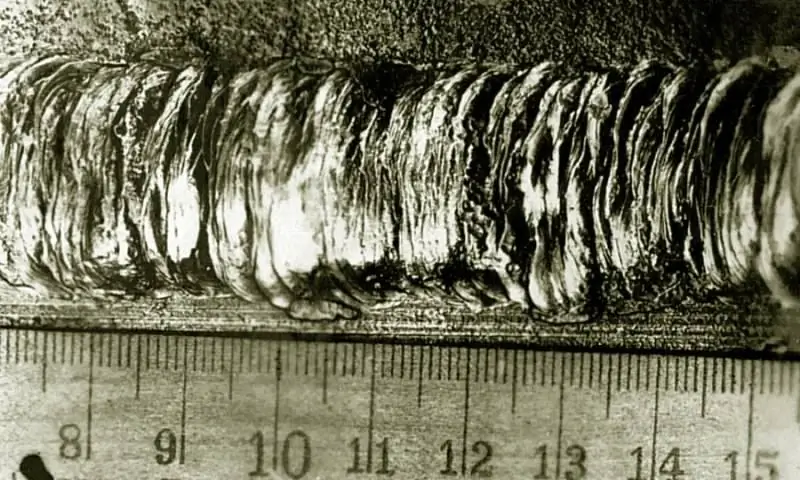
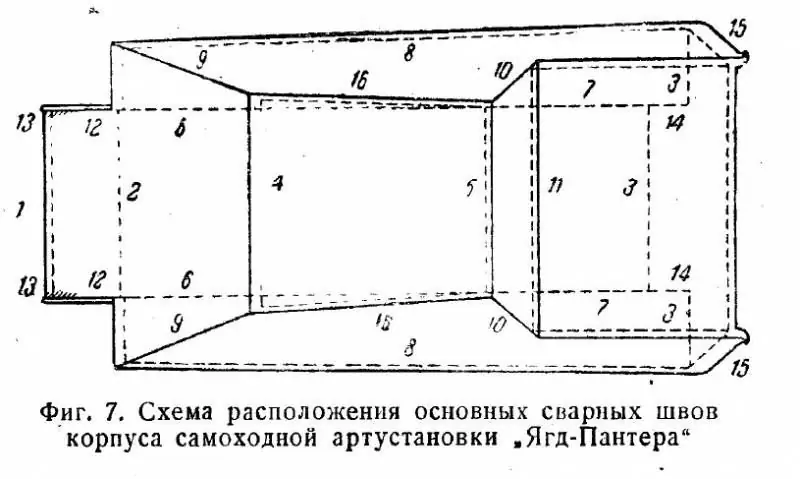
Les Allemands ont effectué le soudage des coques de chars dans des conditions assez confortables sur d'énormes basculeurs sans pointes préalables (bien que dans certains cas, ils soient encore passés à travers une électrode de 5 mm sur toute la longueur du joint). Le basculeur était une structure sur laquelle, comme sur une broche, la carcasse d'un char allemand tournait autour de l'axe longitudinal. L'entraînement était soit manuel, soit électrique. En raison de la grande précision de coupe, les écarts entre les parties du corps assemblées sur le rotateur ne dépassaient pas (au moins pendant la période principale de la guerre) 3-4 mm. Sinon, des joints de processus en acier ont été utilisés. Les soudures longues ont été brisées par les soudeurs en plusieurs petites et soudées simultanément dans une direction. Les coutures de fermeture ont également été soudées par deux soudeurs de manière synchrone l'un vers l'autre. Cela a assuré la contrainte de durcissement minimale de l'acier et la distribution la plus uniforme. Selon l'une des légendes, exprimée par Alexander Volgin dans le document "Cadre pour la ménagerie allemande", le salaire des soudeurs dans certaines entreprises du Troisième Reich était à la pièce - pour la masse de métal déposée sur le réservoir.
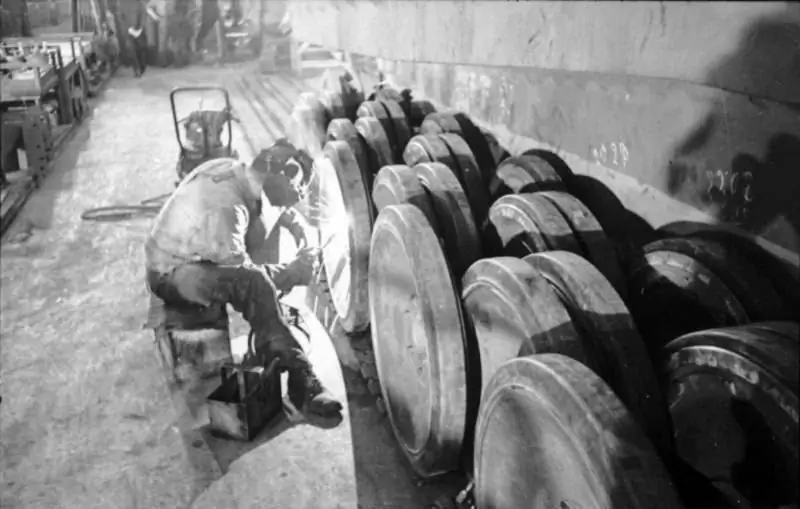
Il n'est pas nécessaire de parler de règles spéciales pour le contrôle des cordons de soudure dans l'industrie allemande des chars - il n'y avait pas de rayons X, pas de détection de défaut magnétique, pas de perçage primitif. Et il y avait des fissures dans les coutures ! S'ils mesuraient jusqu'à 100 mm de long, ils étaient alors meulés et soudés, et s'ils étaient plus longs, ils étaient alors fondus avec un arc électrique et également soudés. Ils ont également fait de même avec des fissures détectées visuellement dans l'armure principale. Soit dit en passant, au fil du temps, les Allemands ont réussi à réduire la proportion de fissures dans les joints soudés de 30 à 40% à 10 à 20% en raison de nouvelles compositions d'électrodes. On a également utilisé l'alternance de passes dans des soudures multicouches avec des électrodes austénitiques et ferrites.