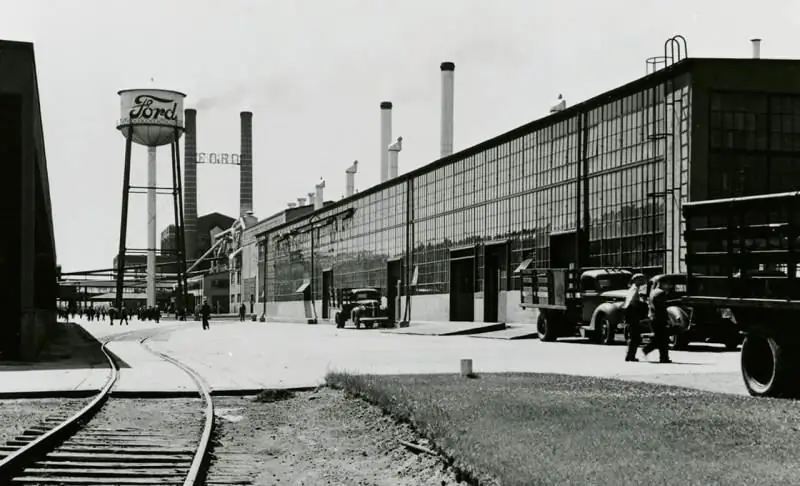
Technologies stratégiques
Avant de se familiariser avec les caractéristiques de la production de blindés dans l'usine Michigan Ford à Detroit (États-Unis), il convient d'expliquer brièvement les conditions dans lesquelles l'industrie blindée s'est établie en URSS. Comme vous le savez, tout s'apprend par comparaison.
La production de blindés pendant la Seconde Guerre mondiale était l'un des facteurs les plus importants de l'avantage stratégique. Avec le début de la guerre, l'Union soviétique s'est retrouvée dans une situation désastreuse - toute la production de blindés était concentrée dans la partie européenne du pays. L'avancée rapide de l'armée allemande pourrait paralyser complètement la production de blindés de char dans le pays. Ce n'est qu'au prix d'efforts incroyables pour évacuer une partie des usines vers l'est au début de la guerre qu'il a été possible de restaurer la production d'armures. Les principales "usines blindées" étaient les usines métallurgiques de Kuznetsk, Nijni Tagil et Magnitogorsk.
Mais l'affaire ne se limitait pas à un simple transfert de production vers un nouveau site derrière la ligne de front. La plupart des nouvelles usines n'étaient pas adaptées à la fusion des blindages de chars - avant la guerre, les usines travaillaient pour les besoins du Commissariat du peuple à la métallurgie ferreuse. Wartime a ajouté ses propres ajustements. Maintenant que les fours à foyer ouvert avaient souvent des travailleurs peu qualifiés, il y avait un problème aigu du manque d'équipements spéciaux thermiques, de pressage et de travail des métaux. Par conséquent, le transfert de la production d'armures s'est accompagné d'une restructuration sérieuse de la technologie elle-même pour la fusion de l'acier militaire. Il a donc fallu adapter la production aux principaux fours à sole pour 120-180 tonnes, hors procédé de désoxydation par diffusion. Le durcissement des plaques de blindage et des pièces de blindage devait être effectué dans l'eau.
Une telle simplification ne pouvait qu'affecter la qualité de l'armure reçue. Cela est particulièrement vrai pour l'acier de réservoir à haute dureté 8C le plus difficile à fabriquer. Les tout premiers échantillons de plaques de blindage sur les tests ont montré une ardoise et une stratification importantes de la fracture, une forte tendance à la formation de fissures lors du soudage et du redressage. En plus de cela, des tests sur le terrain ont révélé la fragilité excessive des échantillons de blindage lors des tirs d'obus.
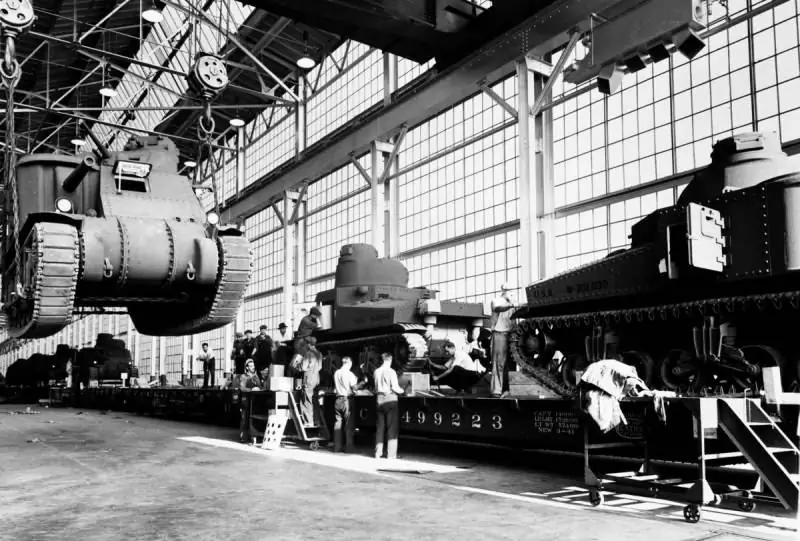
De tels défauts ne pouvaient être ignorés. Et dans le TsNII-48 spécialisé, ils ont développé un certain nombre d'améliorations. Tout d'abord, à partir de maintenant, l'acier de blindage était censé être fondu uniquement dans des fours préchauffés après la fusion des qualités d'acier "civiles". L'acier devait bouillir dans le bain de fusion à foyer ouvert pendant au moins une heure et demie, et versé dans des moules carrés ou convexes. De plus, les métallurgistes ont porté une attention particulière à la teneur en soufre de la fonte d'origine (pas plus de 0,06 %), ainsi qu'au carbone et au manganèse. En combinaison avec d'autres mesures, cela a permis d'améliorer la qualité de l'armure. En particulier, pour réduire l'ardoise et la stratification de la fracture.
Un problème important était la technologie de traitement thermique des armures domestiques. Pour faire simple, le durcissement et la trempe des plaques de blindage prenaient trop de temps et d'énergie, et l'équipement nécessaire manquait. Il fallait simplifier le processus. À cet égard, nous donnerons un exemple typique. En 1942, les métallurgistes de TsNII-48 ont réussi à simplifier le processus de préparation thermique à tel point que seulement pour certaines parties du fond des réservoirs KV et T-34, ils ont économisé environ 3230 heures de four pour 100 coques.
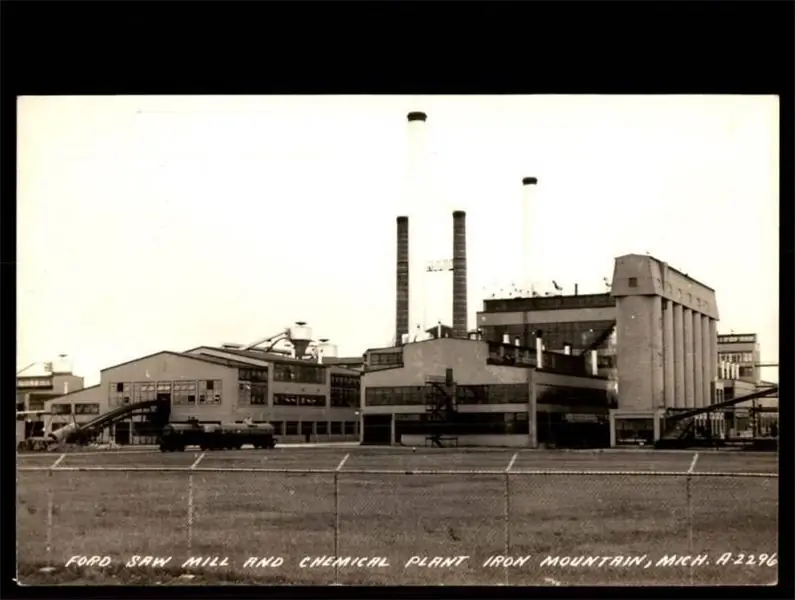
Néanmoins, jusqu'à la toute fin de la guerre en Union soviétique, les conditions pour la production d'un blindage de char stratégiquement important étaient loin d'être requises. On ne peut pas en dire autant de l'industrie militaire du partenaire d'outre-mer, dont le territoire n'a pas été touché par la guerre mondiale. Les ingénieurs métallurgistes soviétiques durent s'en assurer une nouvelle fois le 26 février 1945, 72 jours avant la Victoire.
Le luxe américain
L'histoire peu connue de la visite de la délégation soviétique à l'usine blindée Ford à Détroit a été annoncée par Vasily Vladimirovich Zapariy, candidat aux sciences historiques de l'Institut d'histoire et d'archéologie de la branche de l'Oural de l'Académie des sciences de Russie. Le matériel du scientifique est basé sur le rapport de métallurgistes soviétiques sur les résultats d'un voyage aux États-Unis conservés dans les archives économiques d'État russes (RGAE). A noter que le RGAE n'est qu'un trésor de documents d'archives de l'époque de la Grande Guerre patriotique liés à la production d'équipements et équipements militaires. Il ne reste plus qu'à deviner combien de secrets les archives conservent parmi les preuves jusqu'alors classifiées.
Selon les ingénieurs revenus de Détroit, l'atelier blindé de l'usine Ford était un bâtiment composé de deux travées mesurant 273 mètres de longueur, 30 mètres de largeur et environ 10 mètres de hauteur. Dans le même temps, le magasin ne sentait pas l'armure. Il était principalement destiné au traitement thermique et à la découpe de l'acier. Cela a naturellement suscité un intérêt particulier parmi les métallurgistes soviétiques, étant donné les problèmes décrits ci-dessus de la production nationale de blindés. Le principal profil de production de l'atelier Ford Motors travaillait avec des blindages jusqu'à 76 mm d'épaisseur. Des tôles d'acier traitées thermiquement ont été utilisées pour souder les coques de véhicules blindés légers et moyens dans d'autres usines de Détroit.
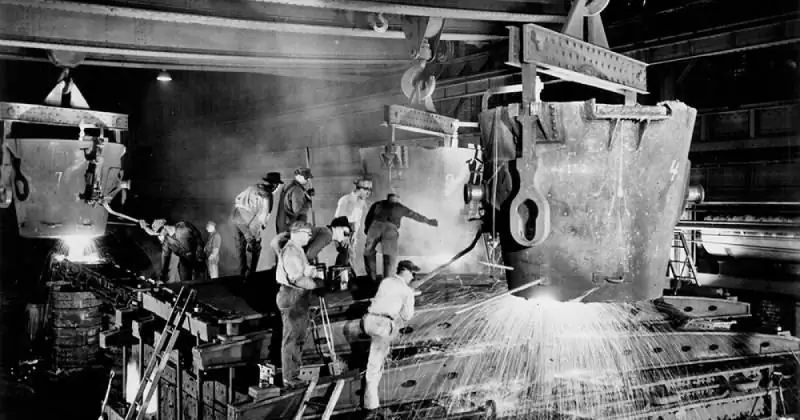
Tout d'abord, la mécanisation du processus de production a impressionné les ateliers Ford. Après fusion et laminage, les plaques de blindage étaient livrées à l'atelier de traitement thermique sur des chargeurs hydrauliques à table United. Les chargeurs, à leur tour, ont pris l'armure des plates-formes ferroviaires situées à proximité de l'atelier. Dans l'atelier lui-même, il y avait deux ponts roulants conçus pour déplacer les tôles de blindage pendant toutes les opérations technologiques, à l'exception des processus de durcissement.
Pour créer la structure cristalline nécessaire de l'armure, deux presses, avec un effort de 2500 tonnes chacune, cinq fours méthodiques à convoyeur de 70 mètres et cinq fours à convoyeur de trempe au gaz de 100 mètres ont été sollicités. L'eau était fournie aux presses de durcissement des blindages par le fonctionnement de six pompes à la fois, pompant plus de 3700 litres par minute. Comme l'ont écrit les ingénieurs russes, la complexité et le coût de la conception de telles presses, capables d'emboutir et de refroidir simultanément des armures chauffées au rouge, étaient prohibitifs. Dans le même temps, il y avait des doutes sur l'opportunité d'utiliser des presses pour les armures d'une épaisseur de 30 à 76 mm. Ici, l'intensité de l'approvisionnement en eau pour le refroidissement est venue au premier plan.
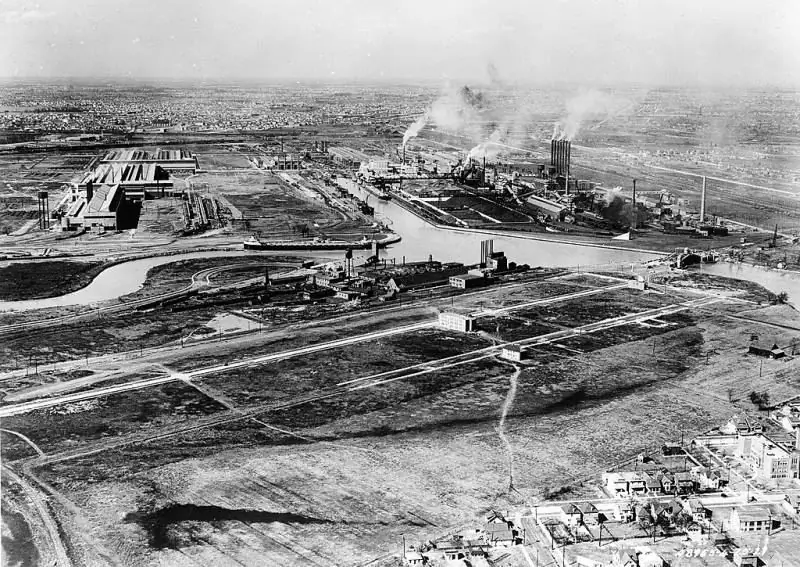
Les presses de 2 500 tonnes n'étaient pas les seules du véhicule blindé Ford. Les presses Toledo # 206 étaient engagées dans la découpe de blindages minces et développaient une pression de 161 tonnes. Pour les blindages de plus de 2,5 cm d'épaisseur, la coupe au feu était exclusivement utilisée.
Lors d'une visite de l'entreprise, les métallurgistes ont pu observer le processus de durcissement d'une fine armure pare-balles. Elle est restée sous une presse de 1000 tonnes pendant 15 secondes, puis la tôle a été envoyée pendant 2,5 heures pour une trempe à 900 degrés Celsius et pour quatre heures de vacances à 593 degrés.
Toute cette richesse technique a été observée par les ingénieurs soviétiques, sans compter divers "petits accessoires": machines à souder, fraiseuses, ciseaux, etc.
La principale caractéristique du traitement thermique de l'armure était le flux de production continu. À presque toutes les étapes du traitement, les tôles d'acier étaient en train de se déplacer sur des convoyeurs à rouleaux et à chaînes. Le convoyeur était commandé à partir d'une console centrale. À l'une des dernières étapes, toutes les plaques de blindage ont été inspectées pour le niveau de dureté Brinell. Dans ce cas, la fluctuation du paramètre de test d'une feuille à l'autre doit être minime - pas plus de 0,2 mm.
D'un intérêt particulier pour la délégation soviétique étaient deux grenailleuses, qui nettoyaient les plaques de blindage presque après chaque opération technologique. Un tel perfectionnisme et un tel luxe ne pouvaient s'offrir que par des Américains, loin des rigueurs de la guerre.