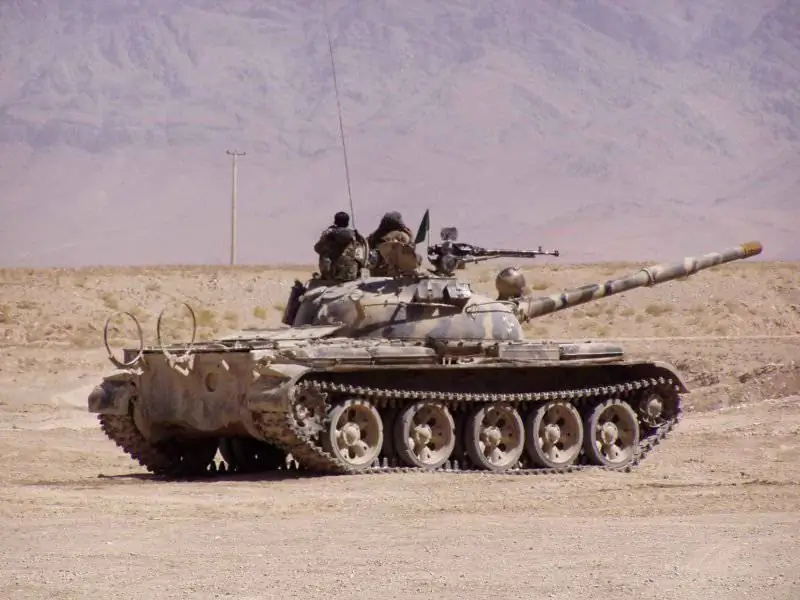
En 1955, une décision du gouvernement a été prise de créer un bureau d'études pour l'ingénierie diesel spéciale à l'usine d'ingénierie des transports de Kharkov et de créer un nouveau moteur diesel de réservoir. Le professeur A. D. Charomsky a été nommé concepteur en chef du bureau d'études.

Le choix du schéma de conception du futur moteur diesel a été déterminé principalement par l'expérience de travail sur les moteurs diesel 2 temps OND TsIAM et le moteur U-305, ainsi que par la volonté de répondre aux exigences des concepteurs du nouveau T -64 tank, développé dans cette usine sous la direction du concepteur en chef AA … Morozov: garantir les dimensions minimales du moteur diesel, notamment en hauteur, en combinaison avec la possibilité de le placer dans le réservoir en position transversale entre les réducteurs planétaires embarqués. Un schéma diesel à deux temps a été choisi avec une disposition horizontale de cinq cylindres avec des pistons se déplaçant de manière opposée. Il a été décidé de fabriquer un moteur avec gonflage et utilisation de l'énergie des gaz d'échappement dans une turbine.
Quelle a été la justification du choix d'un moteur diesel 2 temps ?
Plus tôt, dans les années 1920-1930, la création d'un moteur diesel à 2 temps pour l'aviation et les véhicules terrestres a été retardée en raison de nombreux problèmes non résolus qui ne pouvaient pas être surmontés avec le niveau de connaissances, d'expérience et de capacités de l'industrie nationale accumulés par cet instant.
L'étude et la recherche des moteurs diesel 2 temps de certaines firmes étrangères ont permis de conclure à la difficulté importante de les maîtriser en production. Ainsi, par exemple, une étude du Central Institute of Aviation Motors (CIAM) dans les années 30 du moteur diesel Jumo-4 conçu par Hugo Juneckers a montré des problèmes importants liés au développement de tels moteurs dans la production de tels moteurs par le industrielle de cette période. On savait également que l'Angleterre et le Japon, ayant acheté une licence pour ce moteur diesel, avaient subi des échecs dans le développement du moteur Junkers. Parallèlement, dans les années 30 et 40, des travaux de recherche sur les moteurs diesel 2 temps étaient déjà menés dans notre pays et des échantillons expérimentaux de tels moteurs étaient fabriqués. Le rôle moteur dans ces travaux appartenait aux spécialistes du CIAM et, en particulier, à son Département des moteurs pétroliers (OND). CIAM a conçu et fabriqué des échantillons de moteurs diesel 2 temps de différentes dimensions: OH-2 (12/16, 3), OH-16 (11/14), OH-17 (18/20), OH-4 (8/ 9) et un certain nombre d'autres moteurs d'origine.
Parmi eux se trouvait le moteur FED-8, conçu sous la direction d'éminents scientifiques des moteurs B. S. Stechkin, N. R. Briling, A. A. Bessonov. Il s'agissait d'un moteur diesel d'avion 2 temps 16 cylindres en X avec distribution de gaz soupape-piston, d'une dimension de 18/23, développant une puissance de 1470 kW (2000 ch). L'un des représentants des moteurs diesel 2 temps avec suralimentation est un moteur diesel 6 cylindres turbo-piston en forme d'étoile d'une capacité de 147 … 220 kW (200 … 300 ch) fabriqué chez CIAM sous la direction de BS Stechkin. La puissance de la turbine à gaz était transmise au vilebrequin par l'intermédiaire d'une boîte de vitesses appropriée.
La décision prise alors lors de la création du moteur FED-8 en termes d'idée elle-même et de schéma de conception représentait alors un pas en avant significatif. Cependant, le processus de travail et en particulier le processus d'échange de gaz à un degré élevé de pressurisation et de soufflage en boucle n'ont pas été élaborés au préalable. Par conséquent, le diesel FED-8 n'a pas été développé davantage et en 1937, les travaux sur celui-ci ont été interrompus.
Après la guerre, la documentation technique allemande est devenue la propriété de l'URSS. Elle tombe dans l'A. D. Charomsky en tant que développeur de moteurs d'avion, et il s'intéresse à la valise de Junkers.
Valise de Junkers - une série de moteurs d'avion à deux temps turbo-pistons Jumo 205 avec des pistons à mouvement opposé a été créée au début des années 30 du XXe siècle. Les caractéristiques du moteur Jumo 205-C sont les suivantes: 6 cylindres, 600 ch. course 2 x 160 mm, cylindrée 16,62 litres, taux de compression 17: 1, à 2 200 tr/min
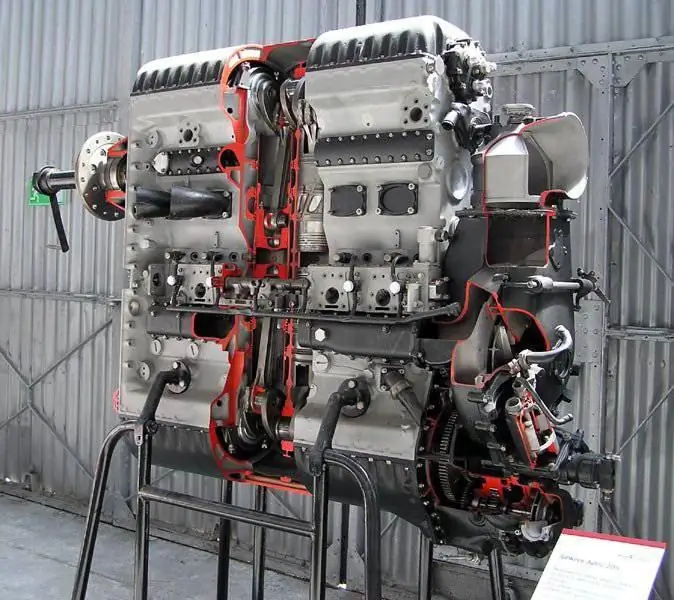
Moteur Jumo 205
Pendant la guerre, environ 900 moteurs ont été produits, qui ont été utilisés avec succès sur des hydravions Do-18, Do-27, et plus tard sur des bateaux à grande vitesse. Peu après la fin de la Seconde Guerre mondiale en 1949, il a été décidé d'installer de tels moteurs sur les patrouilleurs est-allemands, qui étaient en service jusqu'aux années 60.
Sur la base de ces développements, AD Charomsky en 1947 en URSS créa un avion à deux temps diesel M-305 et un compartiment monocylindre de ce moteur U-305. Ce moteur diesel développait une puissance de 7350 kW (10 000 ch) avec un faible poids spécifique (0, 5 kg / h.p.) et une faible consommation de carburant spécifique -190 g / kWh (140 g / h.p.h). Un arrangement en forme de X de 28 cylindres (quatre blocs de 7 cylindres) a été adopté. La dimension du moteur a été choisie égale à 12/12. Une suralimentation élevée était fournie par un turbocompresseur relié mécaniquement à l'arbre diesel. Pour vérifier les principales caractéristiques définies dans le projet M-305, pour élaborer le processus de travail et la conception des pièces, un modèle expérimental du moteur a été construit, qui avait l'indice U-305. G. V. Orlova, N. I. Rudakov, L. V. Ustinova, N. S. Zolotarev, S. M. Shifrin, N. S. Sobolev, ainsi que des techniciens et des ouvriers de l'usine pilote CIAM et de l'atelier OND.
Le projet de l'avion diesel pleine grandeur M-305 n'a pas été mis en œuvre, car le travail du CIAM, comme toute l'industrie aéronautique du pays, à cette époque était déjà axé sur le développement des turboréacteurs et des turbopropulseurs et la nécessité d'un Le moteur diesel de 10 000 chevaux pour l'aviation a disparu.
Les indicateurs élevés obtenus sur le moteur diesel U-305: puissance du moteur en litre 99 kW / l (135 ch / l), puissance en litre d'un cylindre de près de 220 kW (300 ch) à une pression de suralimentation de 0,35 MPa; vitesse de rotation élevée (3 500 tr/min) et les données d'un certain nombre d'essais à long terme réussis du moteur - ont confirmé la possibilité de créer un moteur diesel 2 temps efficace de petite taille à des fins de transport avec des indicateurs et des éléments structurels similaires.
En 1952, le laboratoire n°7 (ex OND) du CIAM est transformé par décision gouvernementale en Laboratoire de Recherche des Moteurs (NILD) subordonné au Ministère de l'Ingénierie des Transports. Un groupe d'initiative d'employés - des spécialistes hautement qualifiés des moteurs diesel (G. V. Orlova, N. I. Rudakov, S. M. Shifrin, etc.), dirigé par le professeur A. D. Charomsky, est déjà dans le NILD (plus tard - NIID). le moteur 2 temps U-305.
Diesel 5TDF
En 1954, A. D. Charomsky a proposé au gouvernement de créer un moteur diesel à réservoir 2 temps. Cette proposition coïncidait avec l'exigence du concepteur en chef du nouveau char A. A. Morozov et A. D. Charomsky a été nommé concepteur en chef de l'usine. V. Malyshev à Kharkov.
Étant donné que le bureau de conception des moteurs de réservoir de cette usine est resté principalement à Chelyabinsk, A. D. Charomsky a dû former un nouveau bureau d'études, créer une base expérimentale, établir une production pilote et en série et développer une technologie que l'usine ne possédait pas. Les travaux ont commencé par la fabrication d'une unité monocylindre (OTsU), similaire au moteur U-305. À l'OTsU, les éléments et les procédés du futur moteur diesel à réservoir pleine grandeur étaient en cours d'élaboration.
Les principaux participants à ce travail étaient A. D. Charomsky, G. A. Volkov, L. L. Golinets, B. M. Kugel, M. A., Meksin, I. L. Rovensky et d'autres.
En 1955, des employés de NILD ont rejoint le travail de conception de l'usine diesel: G. V. Orlova, N. I. Rudakov, V. G. Lavrov, I. S. Elperin, I. K. Lagovsky et d'autres spécialistes de NILD L. M. Belinsky, LI Pugachev, LSRoninson, SM Shifrin ont effectué des travaux expérimentaux à l'OTsU de l'usine d'ingénierie des transports de Kharkov. C'est ainsi qu'apparaît le 4TPD soviétique. C'était un moteur en état de marche, mais avec un inconvénient - la puissance était d'un peu plus de 400 ch, ce qui n'était pas suffisant pour un char. Charomsky met un autre cylindre et obtient 5TD.
L'introduction d'un cylindre supplémentaire a sérieusement modifié la dynamique du moteur. Un déséquilibre est apparu qui a provoqué d'intenses vibrations de torsion dans le système. Les principales forces scientifiques de Leningrad (VNII-100), Moscou (NIID) et Kharkov (KhPI) sont impliquées dans sa solution. 5TDF a été mis en condition EXPÉRIMENTALE, par essais et erreurs.
La dimension de ce moteur a été choisie égale à 12/12, soit le même que sur le moteur U-305 et OTsU. Pour améliorer la réponse de l'accélérateur du moteur diesel, il a été décidé de connecter mécaniquement la turbine et le compresseur au vilebrequin.
Diesel 5TD avait les caractéristiques suivantes:
- puissance élevée - 426 kW (580 ch) avec un encombrement relativement réduit;
- vitesse augmentée - 3000 tr/min;
- efficacité de la pressurisation et de l'utilisation de l'énergie des gaz résiduaires;
- faible hauteur (inférieure à 700 mm);
- une diminution de 30 à 35 % du transfert de chaleur par rapport aux moteurs diesel à 4 temps (à aspiration naturelle) existants et, par conséquent, un plus petit volume requis pour le système de refroidissement de la centrale électrique;
- un rendement énergétique satisfaisant et la capacité de faire fonctionner le moteur non seulement au gazole, mais aussi au kérosène, à l'essence et à leurs divers mélanges;
- prise de force par ses deux extrémités et sa longueur relativement réduite, qui permet d'assembler le réservoir MTO avec une disposition transversale d'un moteur diesel entre deux boîtes de vitesses embarquées dans un volume occupé beaucoup plus petit qu'avec une disposition longitudinale de le moteur et la boîte de vitesses centrale;
- placement réussi d'unités telles qu'un compresseur d'air à haute pression avec ses propres systèmes, un démarreur-générateur, etc.
Ayant conservé la disposition transversale du moteur avec une prise de force bidirectionnelle et deux transmissions embarquées planétaires situées des deux côtés du moteur, les concepteurs se sont déplacés vers les emplacements vacants sur les côtés du moteur, parallèlement aux boîtes de vitesses, le compresseur et la turbine à gaz, préalablement montés en 4TD au dessus du bloc moteur. La nouvelle configuration a permis de réduire de moitié le volume du MTO par rapport au char T-54, et les composants traditionnels tels que la boîte de vitesses centrale, la boîte de vitesses, l'embrayage principal, les mécanismes de rotation planétaires embarqués, les transmissions finales et les freins en ont été exclus. Comme indiqué plus loin dans le rapport GBTU, le nouveau type de transmission a permis d'économiser 750 kg de masse et se composait de 150 pièces usinées au lieu des 500 précédentes.
Tous les systèmes d'entretien du moteur étaient imbriqués au-dessus du moteur diesel, formant le "deuxième étage" du MTO, dont le schéma a été nommé "à deux niveaux".
Les hautes performances du moteur 5TD ont nécessité l'utilisation d'un certain nombre de nouvelles solutions fondamentales et de matériaux spéciaux dans sa conception. Le piston de ce diesel, par exemple, a été fabriqué à l'aide d'un coussin chauffant et d'une entretoise.
Le premier segment de piston était un segment de flamme à lèvres continues. Les cylindres étaient en acier chromé.
La capacité de faire fonctionner le moteur avec une pression d'éclair élevée était assurée par le circuit d'alimentation du moteur avec des boulons en acier de support, un bloc en fonte d'aluminium déchargé de l'action des forces de gaz et l'absence de joint de gaz. L'amélioration du processus de purge et de remplissage des cylindres (et c'est un problème pour tous les moteurs diesel 2 temps) a été facilitée dans une certaine mesure par le schéma de dynamique des gaz utilisant l'énergie cinétique des gaz d'échappement et l'effet d'éjection.
Le système de formation du mélange jet-vortex, dans lequel la nature et la direction des jets de carburant sont coordonnées avec la direction du mouvement de l'air, a assuré une turbulisation efficace du mélange de carburant-air, ce qui a contribué à l'amélioration du processus de transfert de chaleur et de masse.
La forme spécialement choisie de la chambre de combustion a également permis d'améliorer le processus de mélange et de combustion. Les chapeaux de palier principaux ont été tirés avec le carter moteur par des boulons de puissance en acier, prenant la charge des forces de gaz agissant sur le piston.
Une plaque avec une turbine et une pompe à eau était fixée à une extrémité du bloc-carter, et une plaque de la transmission principale et des couvercles avec des entraînements vers le compresseur, le régulateur, le capteur tachymétrique, le compresseur haute pression et le distributeur d'air étaient fixées à l'opposé. finir.
En janvier 1957, le premier prototype du moteur diesel de char 5TD a été préparé pour des essais au banc. À la fin des tests au banc, le 5TD de la même année a été transféré pour des essais d'objets (en mer) dans un réservoir expérimental "Object 430", et en mai 1958 a passé les tests d'État interministériels avec une bonne note.
Néanmoins, il a été décidé de ne pas transférer le diesel 5TD à la production de masse. La raison en était à nouveau le changement des exigences de l'armée pour de nouveaux chars, ce qui nécessitait une fois de plus une augmentation de la puissance. Compte tenu des indicateurs techniques et économiques très élevés du moteur 5TD et des réserves inhérentes à celui-ci (qui ont également été démontrées par des tests), une nouvelle centrale d'une capacité d'environ 700 ch. décidé de créer sur sa base.
La création d'un tel moteur original pour l'usine d'ingénierie des transports de Kharkov a nécessité la fabrication d'équipements technologiques importants, un grand nombre de prototypes de moteur diesel et des tests répétés à long terme. Il convient de garder à l'esprit que le département de conception de l'usine est devenu plus tard le Bureau de conception de Kharkov pour le génie mécanique (KHKBD) et que la production de moteurs a été créée pratiquement à partir de zéro après la guerre.
Parallèlement à la conception du moteur diesel, un grand complexe de stands expérimentaux et diverses installations (24 unités) a été créé à l'usine pour tester les éléments de sa conception et de son flux de travail. Cela a grandement aidé à vérifier et à élaborer les conceptions d'unités telles qu'un compresseur, une turbine, une pompe à carburant, un collecteur d'échappement, une centrifugeuse, des pompes à eau et à huile, un carter moteur, etc., cependant, leur développement s'est poursuivi.
En 1959, à la demande du concepteur en chef du nouveau char (AA Morozov), pour qui ce moteur diesel a été conçu à cet effet, il a été jugé nécessaire d'augmenter sa puissance de 426 kW (580 ch) à 515 kW (700 ch).). La version forcée du moteur a été nommée 5TDF.
En augmentant la vitesse du compresseur de suralimentation, la puissance en litres du moteur a été augmentée. Cependant, en forçant le moteur diesel, de nouveaux problèmes sont apparus, principalement dans la fiabilité des composants et des assemblages.
Les concepteurs de KhKBD, NIID, VNIITransmash, les technologues de l'usine et des instituts VNITI et TsNITI (depuis 1965) ont effectué une énorme quantité de calcul, de recherche, de conception et de travail technologique pour atteindre la fiabilité et la durée de fonctionnement requises du moteur diesel 5TDF.
Les problèmes les plus difficiles se sont avérés être les problèmes d'augmentation de la fiabilité du groupe de pistons, de l'équipement de carburant et du turbocompresseur. Toute amélioration, même insignifiante, n'a été apportée que grâce à toute une série de mesures de conception, technologiques, organisationnelles (de production).
Le premier lot de moteurs diesel 5TDF était caractérisé par une grande instabilité dans la qualité des pièces et des assemblages. Une certaine partie des moteurs diesel de la série produite (lot) a accumulé la durée de fonctionnement de la garantie établie (300 heures). Dans le même temps, une partie importante des moteurs a été retirée des stands avant la période de fonctionnement sous garantie en raison de certains défauts.
La spécificité d'un moteur diesel 2 temps à grande vitesse réside dans un système d'échange de gaz plus complexe que dans un moteur 4 temps, une consommation d'air accrue, et une charge thermique plus élevée du groupe piston. Par conséquent, la rigidité et la résistance aux vibrations de la structure, le respect plus strict de la forme géométrique d'un certain nombre de pièces, les propriétés anti-grippantes élevées et la résistance à l'usure des cylindres, la résistance à la chaleur et la résistance mécanique des pistons, l'alimentation dosée et l'élimination soigneuses du lubrifiant des cylindres et une amélioration de la qualité des surfaces de frottement s'imposait. Pour prendre en compte ces spécificités des moteurs 2 temps, il a fallu résoudre des problèmes de conception et technologiques complexes.
L'une des pièces les plus critiques assurant une distribution précise du gaz et une protection des bagues d'étanchéité du piston contre la surchauffe était une bague de flamme de type manchette à paroi mince filetée en acier avec un revêtement antifriction spécial. Dans le raffinement du moteur diesel 5TDF, le problème de l'opérabilité de cet anneau est devenu l'un des principaux. Au cours du processus de réglage fin, pendant longtemps, des éraflures et des ruptures des anneaux de flamme se sont produites en raison de la déformation de leur plan de support, d'une configuration sous-optimale de l'anneau lui-même et du corps du piston, d'un chromage insatisfaisant des anneaux, d'une lubrification insuffisante, alimentation en carburant inégale par les gicleurs, écaillage et dépôt de sels formés sur la garniture de piston, ainsi qu'en raison de l'usure due à la poussière liée à un degré insuffisant de nettoyage de l'air aspiré par le moteur.
Ce n'est qu'à la suite d'un travail long et acharné de nombreux spécialistes de l'usine et des instituts de recherche et technologiques, que la configuration du piston et de la bague de flamme est améliorée, la technologie de fabrication est améliorée, les éléments de l'équipement de carburant sont améliorés, le la lubrification est améliorée, l'utilisation de revêtements antifriction plus efficaces, ainsi que le raffinement du système de purification d'air, les défauts liés au fonctionnement de l'anneau de flamme ont été pratiquement éliminés.
Les pannes des segments de piston trapézoïdaux, par exemple, ont été éliminées en réduisant le jeu axial entre le segment et la gorge du piston, en améliorant le matériau, en modifiant la configuration de la section transversale du segment (passé de trapézoïdal à rectangulaire) et en affinant la technologie pour la fabrication des anneaux. Les fractures des boulons de la chemise de piston ont été réparées par refiletage et verrouillage, resserrement des contrôles de fabrication, serrage des limites de couple et utilisation d'un matériau de boulon amélioré.
La stabilité de la consommation d'huile a été obtenue en augmentant la rigidité des cylindres, en réduisant la taille des découpes aux extrémités des cylindres, en renforçant le contrôle dans la fabrication des bagues collectrices d'huile.
En ajustant finement les éléments de l'équipement combustible et en améliorant les échanges gazeux, une certaine amélioration du rendement énergétique et une diminution de la pression d'éclair maximale ont été obtenues.
En améliorant la qualité du caoutchouc utilisé et en rationalisant l'espace entre le cylindre et le bloc, les cas de fuite de liquide de refroidissement à travers les bagues d'étanchéité en caoutchouc ont été éliminés.
En relation avec une augmentation significative du rapport de transmission du vilebrequin au compresseur, certains moteurs diesel 5TDF ont révélé des défauts tels que le patinage et l'usure des disques d'embrayage à friction, des pannes de la roue du compresseur et une défaillance de ses roulements, qui étaient absents sur le Moteur diesel 5TD. Pour les éliminer, il était nécessaire de prendre des mesures telles que la sélection du serrage optimal de l'ensemble de disques d'embrayage à friction, l'augmentation du nombre de disques dans l'ensemble, l'élimination des concentrateurs de contraintes dans la roue du compresseur, la vibration de la roue, l'augmentation des propriétés d'amortissement de le support et en sélectionnant de meilleurs roulements. Ceci a permis d'éliminer les défauts résultant du forçage du moteur diesel en termes de puissance.
L'augmentation de la fiabilité et de la durée de fonctionnement du moteur diesel 5TDF a largement contribué à l'utilisation d'huiles de meilleure qualité avec des additifs spéciaux.
Sur les stands de VNIITransmash, avec la participation des employés du KKBD et du NIID, de nombreuses recherches ont été menées sur le fonctionnement du moteur diesel 5TDF dans des conditions de véritable poussiéreux de l'air d'admission. Ils ont finalement abouti à un test "poussière" réussi du moteur pendant 500 heures de fonctionnement. Cela a confirmé le haut degré de développement du groupe cylindre-piston du moteur diesel et du système d'épuration de l'air.
Parallèlement au réglage fin du diesel lui-même, il a été testé à plusieurs reprises en conjonction avec les systèmes de la centrale électrique. Dans le même temps, les systèmes étaient améliorés, la question de leur interconnexion et de leur fonctionnement fiable dans le réservoir était résolue.
L. L. Golinets était le concepteur en chef du KHKBD dans la période décisive de mise au point du moteur diesel 5TDF. L'ancien designer en chef A. D. Charomsky a pris sa retraite et a continué à participer à la mise au point en tant que consultant.
Le développement de la production en série du moteur diesel 5TDF dans de nouveaux ateliers spécialement construits de l'usine, avec de nouveaux cadres d'ouvriers et d'ingénieurs qui ont étudié sur ce moteur, a causé de nombreuses difficultés, la participation de spécialistes d'autres organisations.
Jusqu'en 1965, le moteur 5TDF était produit en séries séparées (lots). Chaque série suivante comprenait un certain nombre de mesures développées et testées sur les stands, éliminant les défauts identifiés lors des tests et lors des opérations d'essai dans l'armée.
Cependant, le temps de fonctionnement réel des moteurs n'a pas dépassé 100 heures.
Une percée significative dans l'amélioration de la fiabilité du diesel a eu lieu au début de 1965. À cette époque, de nombreux changements avaient été apportés à la conception et à la technologie de sa fabrication. Introduits en production, ces changements ont permis d'augmenter la durée de fonctionnement de la prochaine série de moteurs jusqu'à 300 heures. Les tests de fonctionnement à long terme des réservoirs équipés de moteurs de cette série ont confirmé la fiabilité considérablement accrue des diesels: tous les moteurs au cours de ces tests ont travaillé 300 heures, et certains d'entre eux (sélectivement), poursuivant les tests, ont travaillé 400 … 500 heures chacun.
En 1965, un lot d'installation de moteurs diesel a finalement été publié selon la documentation de dessin technique corrigée et la technologie pour la production en série. Un total de 200 moteurs de série ont été fabriqués en 1965. La montée en puissance de la production a commencé, culminant en 1980. En septembre 1966, le moteur diesel 5TDF réussit les tests interservices.
Compte tenu de l'historique de la création du moteur diesel 5TDF, il convient de noter l'avancée de son développement technologique en tant que moteur totalement nouveau pour la production de l'usine. Presque simultanément avec la fabrication de prototypes du moteur et son affinement de conception, son développement technologique et la construction de nouvelles installations de production de l'usine et leur achèvement avec des équipements ont été réalisés.
Selon les dessins révisés des premiers échantillons de moteur, déjà en 1960, le développement de la technologie de conception pour la fabrication du 5TDF a commencé et en 1961, la production de la documentation technologique de travail a commencé. Les caractéristiques de conception d'un moteur diesel à 2 temps, l'utilisation de nouveaux matériaux, la grande précision de son individu et de ses composants ont exigé que la technologie utilise des méthodes fondamentalement nouvelles pour le traitement et même l'assemblage du moteur. La conception des processus technologiques et de leurs équipements a été réalisée à la fois par les services technologiques de l'usine, dirigés par A. I. Isaev, V. D. Dyachenko, V. I. Doschechkin et autres, et par des employés des instituts technologiques de l'industrie. Des spécialistes de l'Institut central de recherche sur les matériaux (directeur F. A. Kupriyanov) ont participé à la résolution de nombreux problèmes de métallurgie et de science des matériaux.
La construction de nouveaux ateliers pour la production de moteurs de l'usine d'ingénierie des transports de Kharkov a été réalisée selon le projet de l'Institut Soyuzmashproekt (ingénieur en chef de projet S. I. Shpynov).
Au cours de 1964-1967. la nouvelle production diesel a été complétée par les équipements (en particulier les machines spéciales - plus de 100 unités), sans lesquels il serait pratiquement impossible d'organiser la production en série de pièces diesel. Il s'agissait de machines d'alésage diamant et multibroches pour le traitement de blocs, de machines spéciales de tournage et de finition pour le traitement de vilebrequins, etc. Avant la mise en service de nouveaux ateliers et zones d'essai et le débogage de la technologie de fabrication d'un certain nombre de pièces principales, ainsi que la fabrication des lots d'installation et de la première série du moteur, des coques de grosses locomotives diesel ont été temporairement organisées à la production. des sites.
La mise en service des principales capacités de la nouvelle production de diesel a été réalisée en alternance au cours de la période 1964-1967. Dans les nouveaux ateliers, un cycle complet de production de diesel 5TDF a été assuré, à l'exception de la production d'ébauches située sur le site principal de l'usine.
Lors de la création de nouvelles installations de production, une grande attention a été accordée à l'élévation du niveau et de l'organisation de la production. La production d'un moteur diesel a été organisée selon le principe de la ligne et du groupe, en tenant compte des dernières réalisations de l'époque dans ce domaine. Les moyens les plus avancés de mécanisation et d'automatisation du traitement et de l'assemblage des pièces ont été utilisés, ce qui a permis la création d'une production entièrement mécanisée du moteur diesel 5TDF.
Au cours du processus de production, un grand travail conjoint de technologues et de concepteurs a été réalisé pour améliorer la fabrication de la conception du moteur diesel, au cours duquel les technologues ont soumis environ six mille propositions au KHKBD, dont une partie importante s'est reflétée dans le documentation de conception du moteur.
En termes de niveau technique, la nouvelle production de diesel a largement dépassé les indicateurs des entreprises de l'industrie qui produisaient des produits similaires obtenus à cette époque. Le facteur d'équipement des processus de production de diesel 5TDF a atteint une valeur élevée - 6, 22. En seulement 3 ans, plus de 10 000 processus technologiques ont été développés, plus de 50 000 équipements ont été conçus et fabriqués. Un certain nombre d'entreprises du Conseil économique de Kharkov ont participé à la fabrication d'équipements et d'outils afin d'aider l'usine de Malyshev.
Dans les années suivantes (après 1965), déjà au cours de la production en série du moteur diesel 5TDF, les services technologiques de l'usine et TsNITI ont effectué des travaux pour améliorer encore les technologies afin de réduire l'intensité de la main-d'œuvre, d'améliorer la qualité et la fiabilité du moteur. Employés de TsNITI (directeur Ya. A. Shifrin, ingénieur en chef B. N. Surnin) en 1967-1970. plus de 4500 propositions technologiques ont été développées, permettant une réduction de l'intensité du travail de plus de 530 heures standard et une réduction significative des pertes de ferraille pendant la production. Parallèlement, ces mesures ont permis de réduire de plus de moitié le nombre d'opérations de montage et d'assemblage sélectif de pièces. Le résultat de la mise en œuvre d'un complexe de conception et de mesures technologiques a été un fonctionnement plus fiable et de haute qualité du moteur en fonctionnement avec une durée de fonctionnement garantie de 300 heures. Mais le travail des technologues de l'usine et de TsNITI, en collaboration avec les concepteurs du KHKBD, s'est poursuivi. Il était nécessaire d'augmenter la durée de fonctionnement du moteur 5TDF de 1,5 … 2,0 fois. Cette tâche est également résolue. Le moteur diesel de réservoir 5TDF 2 temps a été modifié et mis en production à l'usine d'ingénierie des transports de Kharkov.
Un rôle très important dans l'organisation de la production de diesel 5TDF a été joué par le directeur de l'usine O. A. Soich, ainsi qu'un certain nombre de leaders de l'industrie (D. F. Ustinov, E. P. Shkurko, I. F. Dmitriev, etc.), ont constamment surveillé les progrès et le développement de la production de diesel, ainsi que ceux qui étaient directement impliqués dans la résolution des problèmes techniques et organisationnels.
Des systèmes autonomes de chauffage à la torche et d'injection d'huile ont permis pour la première fois (en 1978) d'assurer le démarrage à froid d'un moteur diesel de réservoir à des températures pouvant descendre jusqu'à -20 degrés C (de 1984 à -25 degrés C). Plus tard (en 1985), il est devenu possible avec l'aide du système PVV (réchauffeur d'air d'admission) d'effectuer un démarrage à froid d'un moteur diesel à quatre temps (V-84-1) sur des réservoirs T-72, mais seulement jusqu'à une température de -20 degrés C, et pas plus de vingt démarrages dans la ressource de garantie.
Plus important encore, 5TDF est passé en douceur à une nouvelle qualité de diesel de la série 6TD (6TD-1… 6TD-4) avec une plage de puissance de 1 000 à 1 500 ch.et surpasser les analogues étrangers dans un certain nombre de paramètres de base.
INFORMATIONS SUR LE FONCTIONNEMENT DU MOTEUR
Matériaux d'exploitation appliqués
Le principal type de carburant pour alimenter le moteur est le carburant pour moteurs diesel à grande vitesse GOST 4749-73:
à une température ambiante non inférieure à + 5 ° - marque DL;
à des températures ambiantes de +5 à -30° С - marques DZ;
à une température ambiante inférieure à -30°С - marque DA.
Si nécessaire, il est permis d'utiliser du carburant DZ à des températures ambiantes supérieures à + 50 ° C.
En plus du carburant pour moteurs diesel à grande vitesse, le moteur peut fonctionner avec du carburéacteur TC-1 GOST 10227-62 ou de l'essence à moteur A-72 GOST 2084-67, ainsi que des mélanges de carburants utilisés dans toutes les proportions.
L'huile M16-IHP-3 TU 001226-75 est utilisée pour la lubrification du moteur. En l'absence de cette huile, l'utilisation de l'huile MT-16p est autorisée.
Lors du passage d'une huile à une autre, l'huile résiduelle du carter du moteur et du réservoir d'huile de la machine doit être vidangée.
Le mélange des huiles utilisées entre elles, ainsi que l'utilisation d'autres marques d'huiles, sont interdits. Il est permis de mélanger dans le système d'huile le résidu non drainant d'une marque d'huile avec une autre, rechargée.
Lors de la vidange, la température de l'huile ne doit pas être inférieure à + 40 °C.
Pour refroidir le moteur à une température ambiante d'au moins + 5 ° C, on utilise de l'eau douce pure sans impuretés mécaniques, passée à travers un filtre spécial fourni à la CE de la machine.
Pour protéger le moteur de la corrosion et de la formation d'acipe, 0,15% d'un additif à trois composants (0,05 % de chaque composant) est ajouté à l'eau passée à travers le filtre.
L'additif se compose de phosphate trisodique GOST 201-58, de pic de chrome potassique GOST 2652-71 et de nitrite de sodium GOST 6194-69 doit d'abord être dissous dans 5-6 litres d'eau passé à travers un filtre chimique et chauffé à une température de 60-80 °C En cas de ravitaillement de 2-3 litres, il est permis (une seule fois) d'utiliser de l'eau sans additifs.
Ne pas verser d'additif anti-corrosion directement dans le système.
En l'absence d'additif à trois composants, il est permis d'utiliser un pic de chrome pur de 0,5%.
À une température ambiante inférieure à + 50 ° C, un liquide à faible point de congélation (antigel) de "40" ou "65" GOST 159-52 doit être utilisé. L'antigel de marque "40" est utilisé à des températures ambiantes allant jusqu'à -35°C, à des températures inférieures à -35°C - antigel de marque "65".
Remplissez le moteur de carburant, d'huile et de liquide de refroidissement conformément aux mesures visant à empêcher la pénétration d'impuretés mécaniques, de poussière et d'humidité dans le carburant et l'huile.
Il est recommandé de faire le plein à l'aide de camions-citernes spéciaux ou d'un dispositif de ravitaillement ordinaire (lors du ravitaillement à partir de conteneurs séparés).
Le carburant doit être ravitaillé à travers un filtre en soie. Il est recommandé de remplir l'huile à l'aide de remplisseurs d'huile spéciaux. Remplissez d'huile, d'eau et de liquide à faible point de congélation à travers un filtre à mailles n° 0224 GOST 6613-53.
Remplissez les systèmes aux niveaux spécifiés dans les instructions d'utilisation de la machine.
Pour remplir complètement les volumes des systèmes de lubrification et de refroidissement, après avoir fait le plein, démarrez le moteur pendant 1-2 minutes, puis vérifiez les niveaux et, si nécessaire, faites le plein des systèmes, Pendant le fonctionnement, il est nécessaire de contrôler la quantité de liquide de refroidissement et d'huile dans les systèmes du moteur et de maintenir leurs niveaux IB dans les limites spécifiées.
Ne laissez pas tourner le moteur s'il y a moins de 20 litres d'huile dans le réservoir de lubrification du moteur.
Si le niveau du liquide de refroidissement baisse en raison de l'évaporation ou de fuites dans le système de refroidissement, ajoutez respectivement de l'eau ou de l'antigel.
Vidangez le liquide de refroidissement et l'huile par les vannes de vidange spéciales du moteur et de la machine (chaudière de chauffage et réservoir d'huile) à l'aide d'un tuyau avec un raccord avec les orifices de remplissage ouverts. Pour éliminer complètement l'eau restante du système de refroidissement afin d'éviter son gel, il est recommandé de renverser le système avec 5 à 6 litres de liquide à faible point de congélation.
Caractéristiques du fonctionnement du moteur sur différents types de carburant
Le fonctionnement du moteur sur différents types de carburant est assuré par un mécanisme de commande d'alimentation en carburant qui a deux positions pour régler le levier multi-carburant: fonctionnement sur carburant pour moteurs diesel à grande vitesse, carburant pour moteurs à réaction, essence (avec une diminution de puissance) et leurs mélanges en toutes proportions; ne fonctionne qu'à l'essence.
Le fonctionnement sur d'autres types de carburant avec cette position de levier est strictement interdit.
L'installation du mécanisme de commande d'alimentation en carburant de la position "Fonctionnement au gazole" à la position "Fonctionnement à l'essence" s'effectue en tournant la vis de réglage du levier multi-carburant dans le sens horaire jusqu'à ce qu'elle s'arrête, et à partir de la position "Fonctionnement sur essence" sur la position "Fonctionnement au gazole" - en tournant la vis de réglage du levier multi-carburant dans le sens inverse des aiguilles d'une montre jusqu'à ce qu'elle s'arrête.
Caractéristiques de démarrage et de fonctionnement du moteur lors du fonctionnement à l'essence. Au moins 2 minutes avant de démarrer le moteur, il est nécessaire d'allumer la pompe BCN de la machine et de pomper intensivement le carburant avec la pompe d'amorçage manuelle de la machine; dans tous les cas, quelle que soit la température ambiante, avant de démarrer, injecter deux fois de l'huile dans les cylindres.
La pompe centrifuge à essence de la machine doit rester allumée pendant tout le temps que le moteur fonctionne à l'essence, ses mélanges avec d'autres carburants, et pendant de courts arrêts (3-5 minutes) de la machine.
Le régime minimum de ralenti permanent lorsque le moteur fonctionne à l'essence est de 1000 par minute.
CARACTÉRISTIQUES DE FONCTIONNEMENT
S. Suvorov rappelle les avantages et les inconvénients de ce moteur dans son livre "T-64".
Sur les chars T-64A, produits à partir de 1975, le blindage de la tourelle a également été renforcé grâce à l'utilisation de charge corindon.
Sur ces machines, la capacité des réservoirs de carburant a également été augmentée de 1093 litres à 1270 litres, à la suite de quoi une boîte pour ranger les pièces de rechange est apparue à l'arrière de la tourelle. Sur les machines des versions précédentes, les pièces de rechange et les accessoires étaient placés dans des boîtes sur les ailes droites, où des réservoirs de carburant supplémentaires étaient installés, connectés au système de carburant. Lorsque le conducteur installait la vanne de distribution de carburant sur n'importe quel groupe de réservoirs (arrière ou avant), le carburant était produit principalement à partir des réservoirs externes.
Une paire d'engrenages à vis sans fin a été utilisée dans le mécanisme de tension des chenilles, ce qui a permis son fonctionnement sans entretien pendant toute la durée de vie du réservoir.
Les caractéristiques de performance de ces machines ont été considérablement améliorées. Ainsi, par exemple, l'essai avant le prochain numéro de service a été augmenté de 1500 et 3000 km à 2500 et 5000 km pour T01 et TO, respectivement. A titre de comparaison, sur le char T-62 TO1 TO2 a été effectué après 1000 et 2000 km de course, et sur le char T-72 - après 1600-1800 et 3300-3500 km de course, respectivement. La période de garantie pour le moteur 5TDF a été augmentée de 250 à 500 heures, la période de garantie pour l'ensemble de la machine était de 5 000 km.
Mais l'école n'est qu'un prélude, l'opération principale a commencé dans les troupes, où j'ai fini après avoir obtenu mon diplôme universitaire en 1978. Juste avant l'obtention du diplôme, nous avons été informés de l'ordre du commandant en chef des forces terrestres selon lequel les diplômés de notre école ne devraient être distribués qu'aux formations où se trouvent des chars T-64. Cela était dû au fait que dans les troupes, il y avait eu des cas de défaillance massive de chars T-64, en particulier de moteurs 5TDF. La raison - l'ignorance du matériel et des règles de fonctionnement de ces réservoirs. L'adoption du char T-64 était comparable à la transition dans l'aviation des moteurs à pistons aux moteurs à réaction - les vétérans de l'aviation se souviennent de ce que c'était.
Quant au moteur 5TDF, il y avait deux raisons principales à son échec dans les troupes - la surchauffe et l'usure par la poussière. Ces deux raisons étaient dues à l'ignorance ou à la négligence des règles de fonctionnement. Le principal inconvénient de ce moteur est qu'il n'est pas trop conçu pour les imbéciles, il faut parfois qu'ils fassent ce qui est écrit dans le mode d'emploi. Alors que j'étais déjà commandant d'une compagnie de chars, l'un de mes commandants de peloton, diplômé de l'école des chars de Chelyabinsk, qui formait des officiers pour les chars T-72, a commencé à critiquer la centrale électrique du char T-64. Il n'aimait pas le moteur et la fréquence de son entretien. Mais lorsqu'on lui a posé la question « Combien de fois en six mois avez-vous ouvert les toits du MTO sur vos trois réservoirs d'entraînement et regardé dans le compartiment moteur-transmission ? » Il s'est avéré que jamais. Et les chars sont partis, ont fourni un entraînement au combat.
Et ainsi de suite dans l'ordre. Une surchauffe du moteur s'est produite pour plusieurs raisons. Tout d'abord, le mécanicien a oublié de retirer le tapis du radiateur et n'a ensuite pas regardé les instruments, mais cela s'est produit très rarement et, en règle générale, en hiver. Le deuxième et principal est le remplissage de liquide de refroidissement. Selon les instructions, il est censé remplir d'eau (pendant la période de fonctionnement estivale) avec un additif à trois composants, et l'eau doit être remplie à travers un sulfofiltre spécial, dont toutes les machines à libération anticipée étaient équipées, et sur les nouveaux machines un tel filtre a été délivré par entreprise (10-13 réservoirs). Les moteurs sont tombés en panne, principalement les réservoirs du groupe d'opérations d'entraînement, qui fonctionnaient au moins cinq jours par semaine et sont généralement situés à des champs de tir dans des parcs de campagne. Dans le même temps, les "manuels" de mécanicien (appelés mécaniques de machines d'entraînement), en règle générale, des travailleurs acharnés et des gars consciencieux, mais ne connaissant pas les subtilités du moteur, pouvaient parfois se permettre de verser de l'eau dans le système de refroidissement juste au robinet, d'autant plus que le sulfofiltre (qui est un par entreprise) était généralement conservé dans les quartiers d'hiver, quelque part dans le casier du directeur technique de l'entreprise. Le résultat est la formation de tartre dans les canaux minces du système de refroidissement (au niveau des chambres de combustion), le manque de circulation de liquide dans la partie la plus chaude du moteur, la surchauffe et la panne du moteur. La formation de tartre a été aggravée par le fait que l'eau en Allemagne est très dure.
Une fois dans une unité voisine, le moteur a été retiré en raison d'une surchauffe due à la faute du conducteur. Ayant trouvé une petite fuite de liquide de refroidissement du radiateur, sur les conseils de l'un des "experts" pour ajouter de la moutarde au système, il a acheté un paquet de moutarde dans le magasin et a tout versé dans le système, en conséquence - colmatage des canaux et panne de moteur.
Il y avait aussi d'autres surprises avec le système de refroidissement. Soudain, il commence à expulser le liquide de refroidissement du système de refroidissement à travers une vanne vapeur-air (PVK). Certains, ne comprenant pas de quoi il s'agit, essaient de le démarrer à partir du remorqueur - le résultat de la destruction du moteur. Ainsi, le chef adjoint de mon bataillon m'a fait un "cadeau" pour le nouvel an, et j'ai dû changer le moteur le 31 décembre. J'avais le temps avant le Nouvel An, parce que le remplacement du moteur sur un char T-64 n'est pas une procédure très compliquée et, surtout, ne nécessite pas d'alignement lors de son installation. La plupart du temps, le remplacement d'un moteur sur un réservoir T-64, comme sur tous les réservoirs domestiques, est effectué par la procédure de vidange et de ravitaillement en huile et en liquide de refroidissement. Si nos chars avaient des connecteurs avec vannes au lieu de raccords en dur, comme sur les Léopard ou les Leclerc, alors le remplacement du moteur sur les chars T-64 ou T-80 à temps ne prendrait pas plus que de remplacer l'ensemble du groupe motopropulseur sur les chars occidentaux. Par exemple, en ce jour mémorable, le 31 décembre 1980, après avoir vidangé l'huile et le liquide de refroidissement, l'adjudant E. Sokolov et moi avons « jeté » le moteur hors du MTO en seulement 15 minutes.
La deuxième raison de la défaillance des moteurs 5TDF est l'usure due à la poussière. Système de purification d'air. Si vous ne vérifiez pas le niveau de liquide de refroidissement à temps, mais que vous devez le vérifier avant chaque sortie de la machine, il peut arriver qu'il n'y ait plus de liquide dans la partie supérieure de la chemise de refroidissement et qu'une surchauffe locale se produise. Dans ce cas, le point le plus faible est la buse. Dans ce cas, les joints de l'injecteur brûlent ou l'injecteur lui-même tombe en panne, puis à travers des fissures ou des joints brûlés, les gaz des cylindres pénètrent dans le système de refroidissement et, sous leur pression, le liquide est expulsé à travers le PVCL. Tout cela n'est pas fatal au moteur et est éliminé s'il y a une personne bien informée dans l'unité. Sur les moteurs conventionnels en ligne et en forme de V dans une situation similaire, "mene" le joint de culasse, et dans ce cas, il y aura plus de travail.
Si, dans une telle situation, le moteur est arrêté et qu'aucune mesure n'est prise, les cylindres commenceront après un certain temps à se remplir de liquide de refroidissement, le moteur est une grille inertielle et un filtre à air cyclonique. Le filtre à air, conformément au mode d'emploi, est rincé au besoin. Sur les chars de type T-62, il était lavé en hiver après 1000 km, et en été après 500 km. Sur un char T-64 - au besoin. C'est là qu'intervient la pierre d'achoppement - certains l'ont pris comme le fait que vous n'avez pas du tout à le laver. Le besoin s'est fait sentir lorsque le pétrole est entré dans les cyclones. Et si au moins un des 144 cyclones contient de l'huile, alors le filtre à air doit être rincé, car à travers ce cyclone, de l'air non purifié avec de la poussière pénètre dans le moteur, puis, comme l'émeri, les chemises de cylindre et les segments de piston sont effacés. Le moteur commence à perdre de la puissance, la consommation d'huile augmente, puis s'arrête complètement de démarrer.
Il n'est pas difficile de vérifier l'entrée d'huile dans les cyclones - il suffit de regarder les entrées de cyclone sur le filtre à air. Habituellement, ils regardaient le tuyau d'évacuation de la poussière du filtre à air, et s'il y avait de l'huile dessus, ils regardaient le filtre à air et, si nécessaire, le lavaient. D'où vient l'huile ? C'est simple: le goulot de remplissage du réservoir d'huile du système de lubrification du moteur est situé à côté de la grille d'admission d'air. Lors du ravitaillement en huile, un arrosoir est généralement utilisé, mais comme encore une fois, sur les machines d'entraînement, les arrosoirs étaient généralement absents (quelqu'un a perdu, quelqu'un l'a mis sur une courroie de chenille, l'a oublié et l'a traversé, etc.), puis les mécaniciens ont simplement versé de l'huile dans des seaux, tandis que l'huile s'est renversée, est tombé d'abord sur la grille d'admission d'air, puis dans le filtre à air. Même lors du remplissage d'huile à travers un arrosoir, mais par temps venteux, le vent a éclaboussé l'huile sur la maille du filtre à air. Par conséquent, lors du ravitaillement en huile, j'ai demandé à mes subordonnés de mettre un tapis des pièces de rechange et des accessoires du réservoir sur la grille d'admission d'air, ce qui m'a permis d'éviter les problèmes d'usure du moteur par la poussière. Il convient de noter que les conditions poussiéreuses en Allemagne en été ont été les plus sévères. Ainsi, par exemple, lors des exercices divisionnaires d'août 1982, lors d'une marche dans les clairières d'Allemagne, à cause de la poussière suspendue, on ne voyait même pas où se terminait le canon du canon de son propre char. La distance entre les voitures de la colonne était maintenue littéralement par l'odeur. Lorsqu'il restait littéralement quelques mètres au réservoir de tête, il était possible de discerner l'odeur de ses gaz d'échappement et de freiner à temps. Et donc 150 kilomètres. Après la marche, tout: les chars, les gens et leurs visages, les combinaisons et les bottes étaient de la même couleur - la couleur de la poussière de la route.
Diesel 6TD
Parallèlement à la conception et au raffinement technologique du moteur diesel 5TDF, l'équipe de conception KKBD a commencé à développer le prochain modèle de moteur diesel à 2 temps déjà dans une conception à 6 cylindres avec une puissance accrue jusqu'à 735 kW (1000 ch). Ce moteur, comme le 5TDF, était un moteur diesel avec des cylindres disposés horizontalement, des pistons à contre-mouvement et un soufflage à flux direct. Le diesel a été nommé 6TD.
La suralimentation était réalisée à partir d'un compresseur mécaniquement (ressort) connecté à la turbine à gaz, convertissant une partie de l'énergie thermique des gaz d'échappement en travail mécanique pour entraîner le compresseur.
Comme la puissance développée par la turbine n'était pas suffisante pour entraîner le compresseur, il était relié aux deux vilebrequins du moteur à l'aide d'une boîte de vitesses et d'un mécanisme de transmission. Le taux de compression a été pris à 15.
Pour obtenir le calage des soupapes requis, auquel le nettoyage nécessaire du cylindre des gaz d'échappement et le remplissage d'air comprimé seraient assurés, un déplacement angulaire des vilebrequins a été prévu (comme sur les moteurs 5TDF) en combinaison avec une disposition asymétrique de l'admission et les orifices d'échappement des cylindres sur leur longueur. Le couple prélevé sur les vilebrequins est de 30% pour l'arbre d'admission et de 70% pour l'échappement du couple moteur. Le couple développé sur l'arbre d'admission était transmis par la transmission à engrenages à l'arbre d'échappement. Le couple total pourrait être prélevé aux deux extrémités de l'arbre d'échappement via l'embrayage de prise de force.
En octobre 1979, le moteur 6TD, après une révision sérieuse du groupe cylindre-piston, de l'équipement de carburant, du système d'alimentation en air et d'autres éléments, a passé avec succès les tests interministériels. Depuis 1986, les premiers moteurs de la série 55 ont été fabriqués. Au cours des années suivantes, la production en série a augmenté et a culminé en 1989.
Le pourcentage d'unification pièce par pièce du 6TD avec le moteur diesel 5TDF était supérieur à 76% et la fiabilité de fonctionnement n'était pas inférieure à celle du 5TDF, produit en série depuis de nombreuses années.
Les travaux du KHKBD sous la direction du concepteur en chef N. K. Ryazantsev pour améliorer encore le moteur diesel à réservoir 2 temps se sont poursuivis. Les unités, les mécanismes et les systèmes étaient en cours de finalisation, selon lesquels les défauts individuels étaient identifiés en fonctionnement. Le système de pressurisation a été amélioré. De nombreux essais au banc de moteurs ont été effectués avec l'introduction de modifications de conception.
Une nouvelle modification du moteur diesel, 6TD-2, était en cours de développement. Sa puissance n'était plus de 735 kW (1000 ch), comme dans la 6TD, mais de 882 kW (1200 ch). Son unification détaillée avec le moteur diesel 6TD a été assurée à plus de 90 %, et avec le moteur diesel 5TDF - à plus de 69 %.
Contrairement au moteur 6TD, le moteur 6TD-2 utilisait un compresseur centrifuge axial à 2 étages du système de pressurisation et des changements dans la conception de la turbine, du soufflet, du filtre à huile centrifuge, du tuyau de dérivation et d'autres unités. Le taux de compression a également été légèrement réduit - de 15 à 14,5 et la pression effective moyenne a été augmentée de 0,98 MPa à 1,27 MPa. La consommation de carburant spécifique du moteur 6TD-2 était de 220 g / (kW * h) (162 g / (hp * h)) au lieu de 215 g / (kW * h) (158 g / (hp * h)) - pour 6TD. Du point de vue de l'installation dans un réservoir, le moteur diesel 6TD-2 était complètement interchangeable avec le moteur 6DT.
En 1985, le Diesel 6TD-2 a réussi les tests interdépartementaux et la documentation de conception a été soumise pour la préparation et l'organisation de la production en série.
Au KKBD, avec la participation du NIID et d'autres organisations, les travaux de recherche et développement sur le moteur diesel 2 temps 6TD se sont poursuivis dans le but d'augmenter sa puissance à 1103 kW (1500hp), 1176 kW (1600hp), 1323 kW (1800hp) avec des tests sur échantillons, ainsi que la création sur sa base d'une famille de moteurs pour VGM et machines à économie nationale. Pour les VGM de catégorie de poids léger et intermédiaire, des moteurs diesel 3TD d'une capacité de 184 … 235 kW (250-320 ch), 4TD d'une capacité de 294 … 331 kW (400 … 450 ch) ont été développés. Une variante d'un moteur diesel 5DN d'une capacité de 331 à 367 kW (450-500 ch) pour les véhicules à roues a également été développée. Pour les transporteurs de tracteurs et de véhicules d'ingénierie, un projet a été développé pour un moteur diesel 6DN d'une capacité de 441 … 515 kW (600-700 ch).
Diesel 3TD
Les moteurs ZTD de conception à trois cylindres font partie d'une seule série unifiée avec les moteurs de série 5TDF, 6TD-1 et 6TD-2E. Au début des années 60, une famille de moteurs à base de 5TDF est créée à Kharkov pour les véhicules légers (véhicules blindés de transport de troupes, véhicules de combat d'infanterie, etc.) et de catégorie poids lourds (chars, 5TDF, 6TD).
Ces moteurs ont un schéma de conception unique:
- cycle à deux temps;
- disposition horizontale des cylindres;
- haute compacité;
- faible transfert de chaleur;
- la possibilité d'utiliser à température ambiante
environnements de moins 50 à plus 55 °;
- faible déclassement de puissance à haute température
l'environnement;
- multi-carburant.
En plus des raisons objectives, des erreurs ont été commises dans la création d'une famille de moteurs diesel boxer à deux temps 3TD au milieu des années 60. L'idée d'un moteur 3 cylindres a été testée sur la base d'un 5 cylindres dans lequel deux cylindres étaient étouffés. Dans le même temps, le chemin air-gaz et les unités de pressurisation n'étaient pas coordonnés. Naturellement, la puissance des pertes mécaniques a également été augmentée.
Le principal obstacle à la création d'une famille unifiée de moteurs dans les années 60 et 70 était l'absence d'un programme clair pour le développement de la construction de moteurs dans le pays; le leadership « agitait » entre divers concepts de moteurs diesel et de moteurs à turbine à gaz.. Dans les années 70, lorsque Leonid Brejnev est arrivé à la tête du pays, la situation s'est encore aggravée, la production parallèle de chars avec des moteurs différents - T-72 et T-80, qui, par leurs caractéristiques, étaient des "chars analogues" du déjà produit T-64. On ne parlait plus d'unification des moteurs du char, des véhicules de combat d'infanterie et des véhicules blindés de transport de troupes.
Malheureusement, la même situation était dans d'autres branches du complexe militaro-industriel - en même temps, divers bureaux d'études se développaient dans les fusées, la construction aéronautique, tandis que les meilleurs n'étaient pas sélectionnés parmi eux, mais des produits similaires de différents bureaux d'études (Design Bureau) ont été réalisés en parallèle.
Une telle politique marquait le début de la fin de l'économie nationale, et la raison du retard dans la construction de réservoirs, au lieu d'être unis en un "poing unique", les efforts étaient dispersés sur le développement parallèle de bureaux d'études concurrents.
Les véhicules légers (LME), produits dans les années 60 … 80 du siècle dernier, ont des moteurs de conception obsolète, offrant une densité de puissance de l'ordre de 16 à 20 ch / t. Les machines modernes devraient avoir une puissance spécifique de 25-28 ch/t, ce qui augmentera leur maniabilité.
Dans les années 90 et 2000, la modernisation du LME est devenue pertinente - BTR-70, BTR-50, BMP-2.
Au cours de cette période, des tests de ces machines ont été effectués, qui ont montré les caractéristiques élevées du nouveau moteur, mais, en même temps, un grand nombre de moteurs UTD-20S1 ont été stockés et en production sur le territoire de l'Ukraine après l'effondrement. de l'URSS.
Concepteur général pour la construction de réservoirs de l'Ukraine M. D. Borisyuk (KMDB) a décidé d'utiliser les moteurs de série existants - SMD-21 UTD-20 et allemand "Deutz" pour moderniser ces machines.
Chaque véhicule avait ses propres moteurs qui n'étaient pas unifiés entre eux et avec des moteurs déjà dans l'armée. En effet, il est rentable pour les ateliers de réparation du ministère de la Défense d'utiliser les moteurs disponibles dans les entrepôts du client, ce qui réduit le coût des travaux.
Mais ce poste privé de travail de l'Entreprise d'Etat « Usine du nom de V. A. Malysheva »et, surtout, l'usine de granulats.
Cette position s'est avérée ambiguë - d'un côté, des économies, de l'autre, une perte de perspective.
Il convient de noter que dans la KMDB en relation avec 3TD, un certain nombre de réclamations ont été faites (pour le bruit et la fumée), qui ont été acceptées et éliminées.
Afin de réduire la fumée au démarrage et en modes transitoires, un équipement de carburant fermé a été installé sur le moteur ZTD et la consommation d'huile a été considérablement réduite. La réduction du bruit est assurée en diminuant la pression de combustion maximale et en réduisant le jeu dans le couple piston-cylindre sur les moteurs de 280 et 400 ch, ainsi qu'en réduisant la plage de vibrations de torsion
La réduction de la consommation d'huile sur les moteurs ZTD a été obtenue grâce aux facteurs suivants:
- réduire le nombre de cylindres;
- l'utilisation d'un piston avec un corps en fonte au lieu d'un alliage d'aluminium;
- augmenter la pression spécifique du segment racleur d'huile en
paroi du cylindre.
Du fait des mesures prises, la consommation relative d'huile sur les moteurs ZTD se rapproche de la consommation sur les moteurs à des fins économiques nationales.