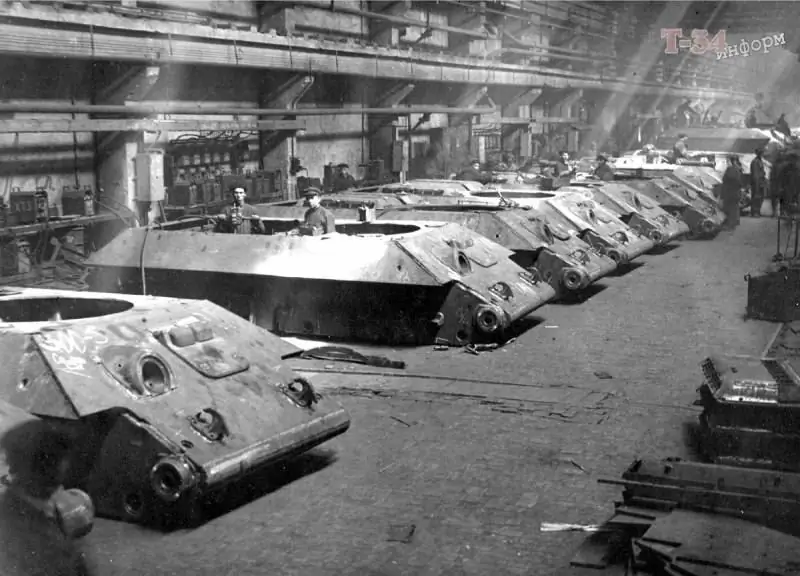
Maillons faibles de la garde en acier
Comment une augmentation de type avalancheuse de la production de chars dont le front a grand besoin ? Le livre de Nikita Melnikov "Tank Industry of the USSR during the Great Patriotic War" fournit des données sur la baisse des conditions de réception des produits finis par les représentants militaires.
Depuis le 15 janvier 1942, les usines de chars se sont montrées très « libérales » dans l'évaluation de la qualité de fabrication des véhicules blindés. Seul un char moyen T-34 sur dix et un KV lourd au choix du représentant militaire ont été soumis à une courte course de cinq kilomètres. Dans le cas des chars T-60, il y avait évidemment plus de doutes, donc un char léger sur cinq était soumis à un essai. Ou, peut-être, de telles machines étaient-elles moins nécessaires à l'avant, elles étaient donc plus strictes à leur égard, même au stade de l'acceptation. Cela confirme indirectement le tir de contrôle du canon de chaque T-60 quittant les portes des usines, alors que les canons T-34 et KV n'étaient testés que sur un véhicule sur dix. Il était permis d'envoyer des chars aux troupes avec des compteurs de vitesse manquants, des moteurs de tourelle, des interphones s'ils étaient remplacés par des lampes de signalisation, ainsi que des ventilateurs de tour. Le dernier point, heureusement, n'était autorisé qu'en hiver.
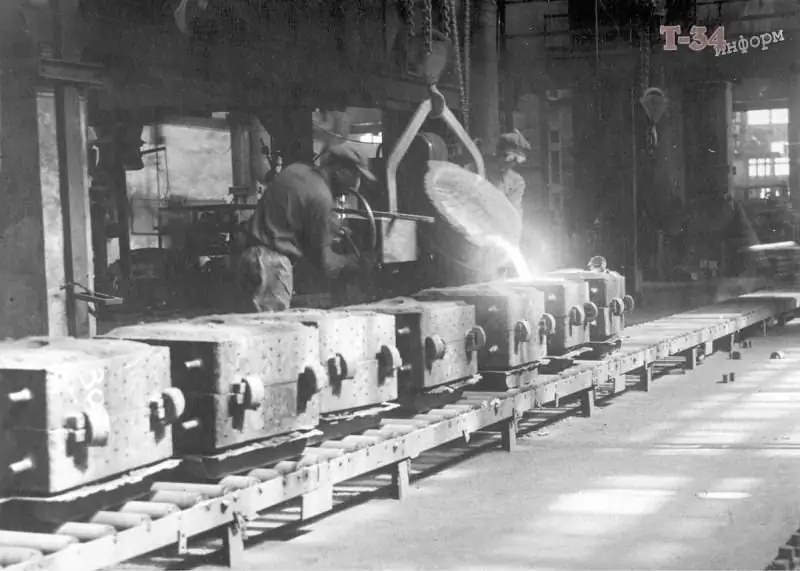
Il convient de noter séparément que l'industrie des chars avait déjà fait face avec succès aux indicateurs quantitatifs de la production de véhicules blindés au milieu de 1942. Uralmash a même régulièrement dépassé les normes de production pour les chars, et l'usine de Kirov à Chelyabinsk, seulement de janvier à mars, a quadruplé la production du moteur diesel V-2.
Ces taux de croissance de la production étaient en grande partie dus à une grave baisse de la qualité des réservoirs sortant de la chaîne de montage. Un exemple illustratif est la 121e brigade de chars, qui, au cours d'un lancer de 250 kilomètres, a perdu la moitié de ses lourds KV en raison de pannes. C'est arrivé en février 1942. Pendant longtemps après cela, la situation n'a pas fondamentalement changé. À l'automne 1942, 84 chars KV ont été inspectés, qui étaient hors d'usage pour des raisons techniques, ce qui n'a même pas fonctionné sur 15 heures de moto. Le plus souvent, il y avait des moteurs défectueux, des boîtes de vitesses cassées, des rouleaux défectueux, des triplex inutilisables et de nombreux défauts mineurs. À l'été 1942, jusqu'à 35 % de tous les chars T-34 ont été perdus non pas à cause d'obus ennemis ou d'explosion par une mine, mais à cause de la défaillance de composants et d'assemblages (principalement des moteurs). Nikita Melnikov dans son travail suggère que certaines des pertes peuvent être attribuées au faible niveau de qualification de l'équipage, mais même en tenant compte de cela, le pourcentage de pertes hors combat est trop élevé. Cependant, de tels dysfonctionnements du KV et du T-34 pourraient bien être éliminés sur le terrain, parfois en remplaçant simplement l'unité ou l'ensemble. Mais il était inutile de se battre avec la qualité insatisfaisante du blindage du T-34 à l'avant - les coques blindées étaient cuites à partir d'acier à faible viscosité, qui, lorsqu'elles étaient touchées par des obus ennemis, provoquaient des fissures, des délaminages et des écaillages. Souvent, des fissures se formaient sur les nouvelles machines, ce qui réduisait considérablement les chances de l'équipage d'une issue favorable lorsqu'un obus allemand touchait une fissure ou une zone de blindage adjacente.
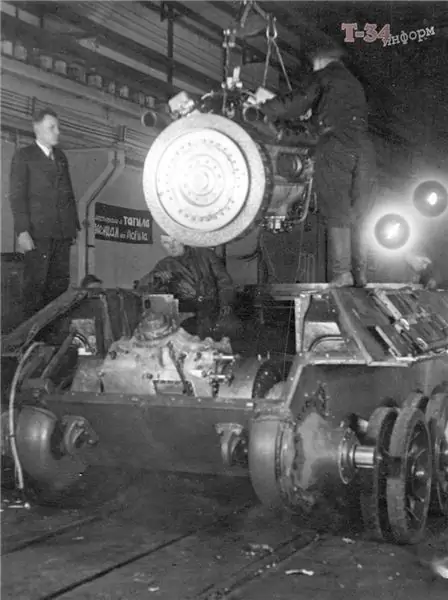
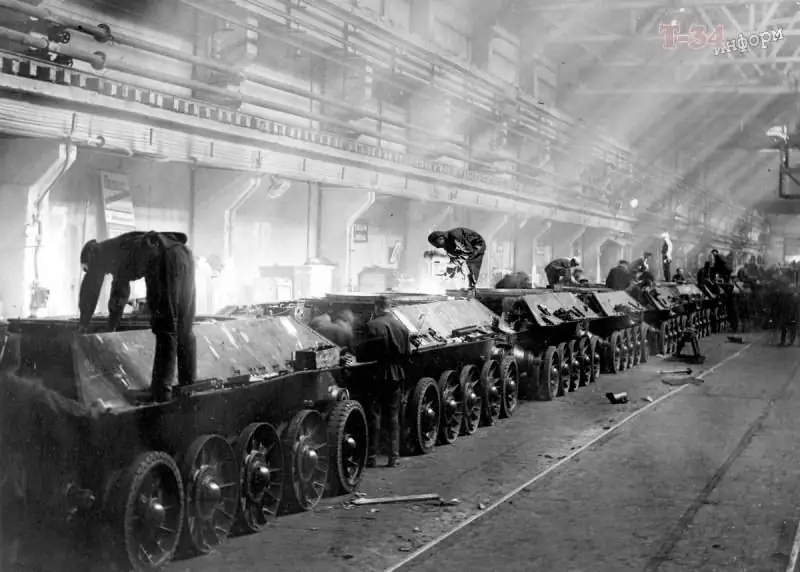
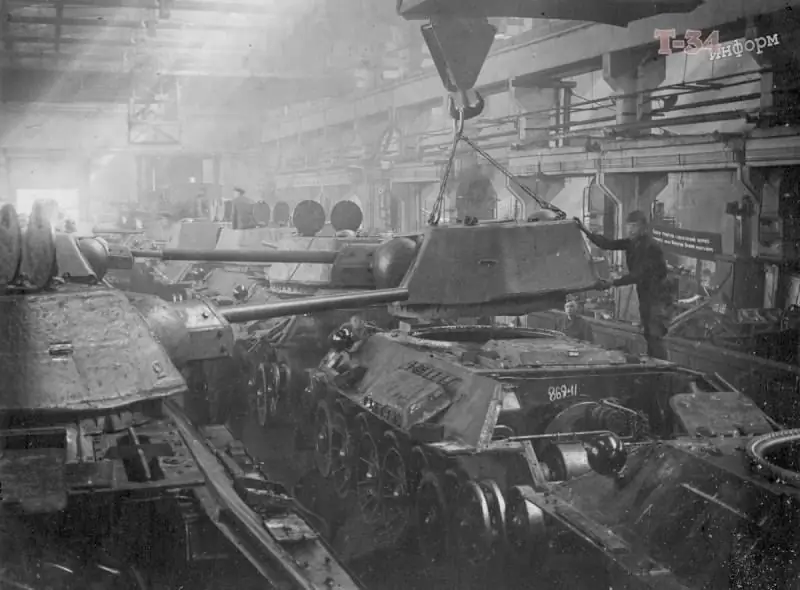
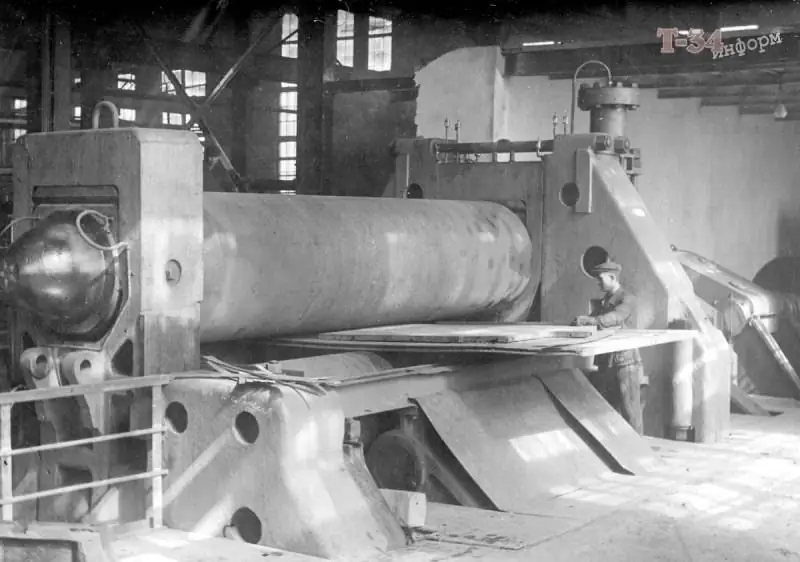
Les premiers appels alarmants sur l'arrivée des unités T-34 avec des fissures retentissent en mai 1942: l'usine # 183 a reçu des réclamations pour 13 véhicules ce mois-là, pour 38 chars en juin, et pour soixante-douze T-34 dans les dix premiers jours de juillet. … Le gouvernement n'a pas pu rester silencieux dans cette affaire et, le 5 juin, la Commission de la défense de l'État a adopté une résolution "sur l'amélioration des chars T-34". Dans le même temps, le parquet de l'URSS a été chargé d'enquêter sur les raisons de cette baisse de qualité des chars.
Au cours des travaux, les enquêteurs ont notamment découvert de nombreux faits de vol de produits de l'alimentation des travailleurs des entreprises de l'industrie des citernes. Les ouvriers de l'usine étaient tout simplement sous-alimentés. Un exemple d'une telle attitude prédatrice est donné dans une série de documents sur Isaac Zaltsman, le leader le plus controversé des usines de chars.
Parmi les entreprises qui se sont "démarquées" dans la production de T-34 défectueux, la célèbre usine de Nijni Tagil a pris la première place. De plus, le pic de la libération de produits défectueux est tombé juste au moment de la direction du Zaltsman susmentionné. Cependant, le directeur de l'entreprise, comme nous nous en souvenons, n'a pas été rétrogradé, mais immédiatement nommé commissaire du peuple de l'industrie des réservoirs. De toute évidence, les autorités ont décidé de blâmer les plus hauts échelons de Viatcheslav Aleksandrovich Malyshev, le 1er commissaire du peuple de l'industrie des chars de l'URSS. Certes, le dégrèvement est venu un an plus tard, à l'été 1943, Malyshev a de nouveau été mis à la place du commissaire du peuple, qu'il a conservé jusqu'à la toute fin de la guerre.
Le bureau du procureur au cours des travaux dans les entreprises évacuées de l'industrie des réservoirs, en plus de l'existence à moitié affamée des ouvriers de l'usine, a révélé un autre problème de qualité insatisfaisante des réservoirs - une violation grave du cycle de production.
Simplification au détriment de la qualité
Comme vous le savez, l'usine de Marioupol du nom d'Ilyich n'a pas pu être défendue, elle s'est retrouvée entre les mains de l'ennemi, et avec une masse d'équipements technologiques qu'ils n'ont pas réussi à évacuer. C'est cette entreprise (la seule du pays) qui était capable de produire des coques blindées à part entière pour le T-34 dans le respect de toutes les normes. Dans l'Oural, pas une seule usine ne pouvait offrir une telle chose, alors l'équipe de recherche de l'Institut blindé (TsNII-48) a commencé à adapter les pratiques de Marioupol aux réalités des usines évacuées. Pour la production d'armures de haute qualité dans les volumes requis par GKO, il y avait une pénurie aiguë de fours thermiques, l'institut a donc développé un nouveau cycle de durcissement des pièces d'armure. À Marioupol, la feuille de blindage est d'abord passée au durcissement, puis aux vacances élevées, puis à nouveau au durcissement. Finalement, des vacances basses ont suivi. Pour accélérer la production, le premier durcissement a d'abord été annulé, puis le revenu élevé, ce qui affecte directement la ténacité de l'acier de blindage et réduit le risque de fissuration. De plus, parmi les mesures nécessaires, selon les spécialistes de l'Armor Institute, l'exigence était de charger non pas une, mais immédiatement quatre ou cinq rangées de plaques de blindage dans le four thermique. Naturellement, cela s'est avéré beaucoup plus rapide, mais la qualité finale des dalles était très hétérogène. Fait intéressant, l'Armored Institute a décidé plus tard d'annuler la procédure de faible revenu, qui réduit les contraintes résiduelles du métal, ce qui n'a pas manqué d'affecter négativement la formation de fissures.
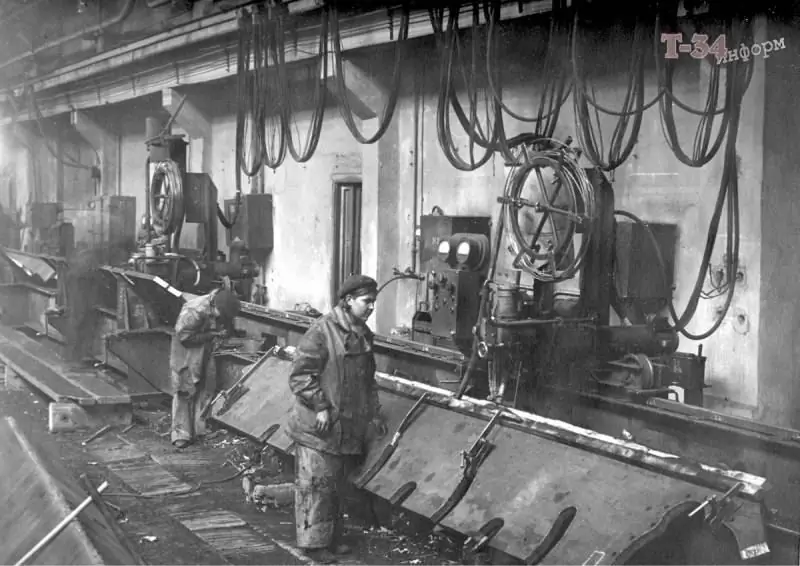
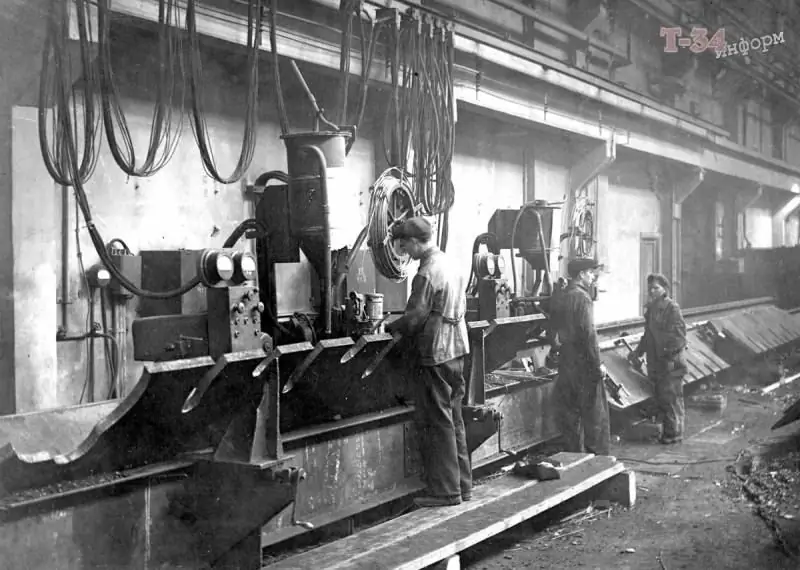
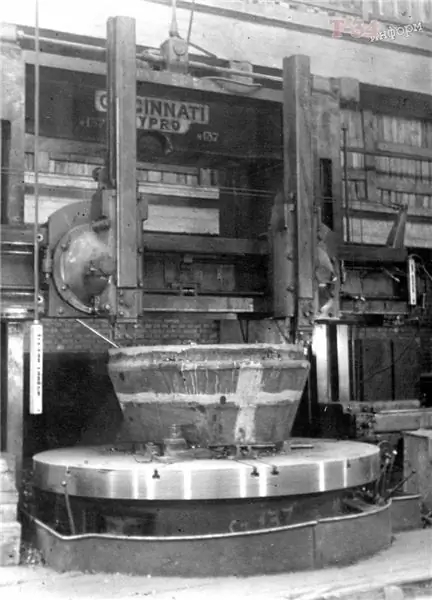
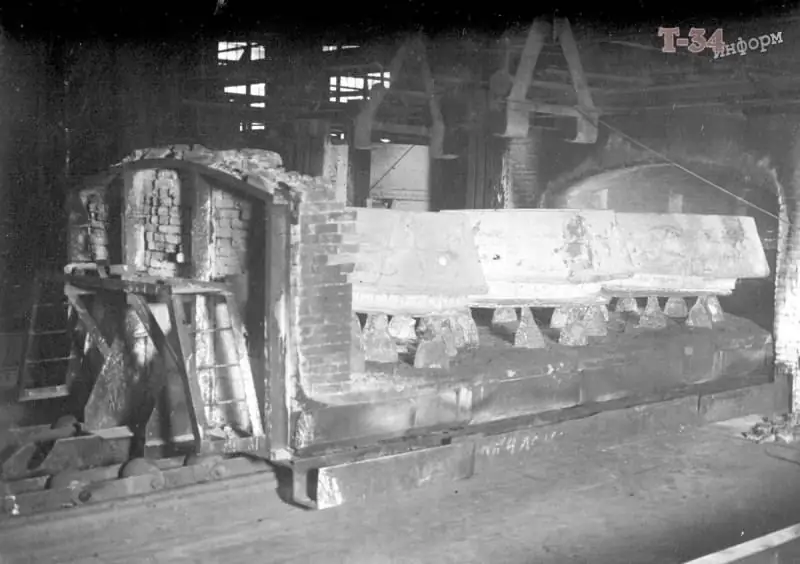
Vous ne pouvez pas couper de l'acier trempé avec des coupeurs à gaz - cette thèse est connue de tous, mais les réalités de la production de coques blindées T-34 obligent à recourir à cette méthode impopulaire. La pointe était en acier 8C, qui s'est dilaté après trempe, et, bien sûr, cela a obligé les ouvriers de l'usine à le couper avec des brûleurs à haute température. Le point de durcissement de l'armure dans la zone de coupe a été perdu.
Il ne vaut pas la peine de prétendre que les recommandations pour améliorer le processus de production n'étaient que négatives pour la qualité de l'armure. Ainsi, une véritable innovation dans l'assemblage des coques des chars T-34 était le soudage de plaques de blindage "en épine" au lieu de l'ancien "dans la serrure" et "dans un quartier". Maintenant, les pièces d'accouplement ne se sont pas coupées l'une dans l'autre, mais se sont partiellement superposées. Seule cette décision a sérieusement réduit le volume d'heures-machines par caisse de 198,9 à 36.
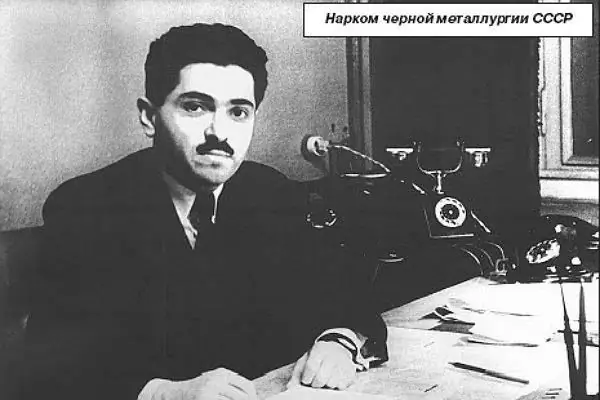
Le principal fournisseur de tôles d'acier défectueuses pour les usines produisant du T-34 était l'usine Novo-Tagil du Commissariat du peuple à la métallurgie ferreuse. Au début, il a été interrompu par les approvisionnements de l'usine de Marioupol, et lorsqu'il est passé à la sienne, un flot de plaintes est venu du front et des usines. En particulier, dans la composition de l'armure 8C de cette entreprise, il y avait de graves divergences avec les spécifications techniques (TU) dans la teneur en carbone, phosphore et silicium. En général, il y avait des difficultés avec TU. Le Commissariat du peuple à la métallurgie des fers n'a pas accepté de conserver le TU selon les normes de Marioupol, dans lesquelles le phosphore, en particulier, ne devrait pas dépasser 0,035%. Début novembre 1941, le commissaire du peuple à la métallurgie ferreuse Ivan Tevosyan a approuvé de nouvelles normes pour le phosphore, qui ont augmenté la teneur possible à 0,04 % et du 4 avril à 0,045%. Il est à noter que les historiens n'ont toujours pas de consensus sur ce, bien sûr, un facteur important dans la qualité de l'acier blindé. Nikita Melnikov, en particulier, mentionne que l'usine de Novo-Tagil, au contraire, vers le milieu de 1942 a réduit la proportion de phosphore de 0, 029% à 0, 024%. Il semble que différents scientifiques trouvent différentes raisons à l'apparition de T-34 défectueux à l'avant. Quoi qu'il en soit, les normes indiquées pour la teneur en éléments chimiques entrant dans la composition de l'acier n'ont parfois pas été respectées. Il était difficile pour les usines d'établir une simple uniformité des produits laminés fournis. Le parquet a également révélé que dans les entreprises de métallurgie ferreuse dans des fours à foyer ouvert, l'acier blindé était "insuffisamment cuit" - au lieu de 15 à 18 heures en réalité, pas plus de 14 heures.
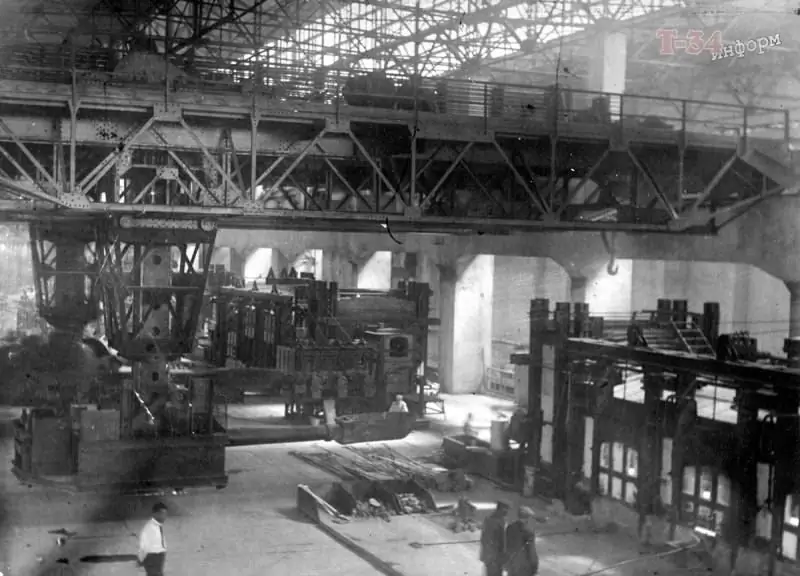
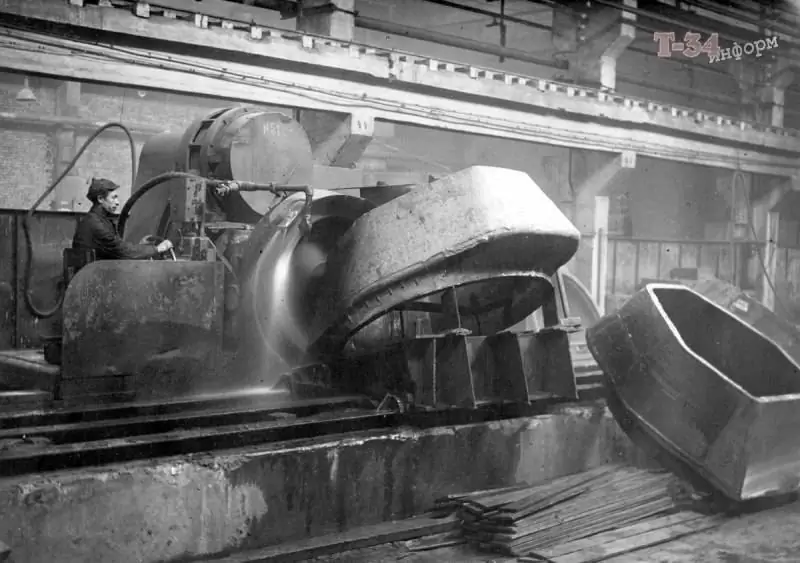
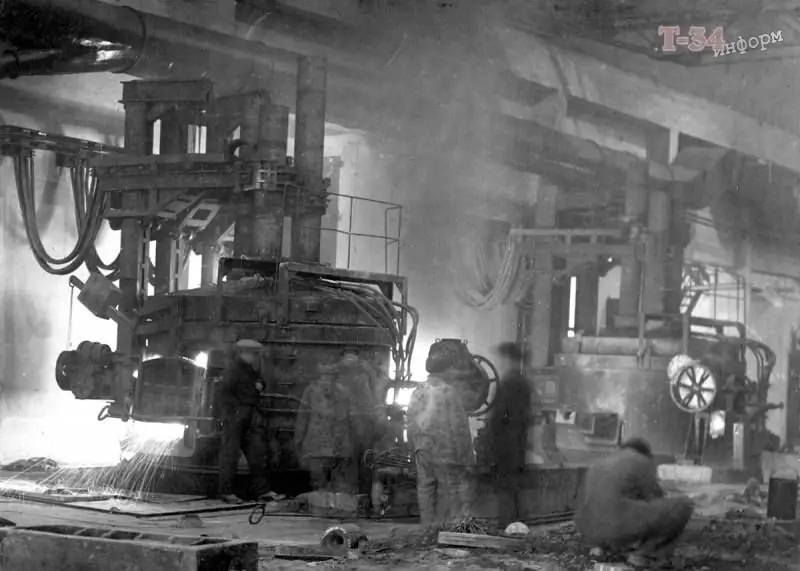
Lorsque les informations sur les causes de la fissuration des coques des T-34 parvinrent à Molotov, les commissariats populaires à la métallurgie ferreuse et l'industrie des chars commencèrent à se rejeter la responsabilité. Pour l'un, la raison principale était la teneur élevée en phosphore dans les plaques de blindage, pour l'autre, de graves violations de la technologie de production de coque dans les usines de chars.
En conséquence, TsNII-48 a été impliqué dans les travaux de lutte contre les fissures sur le T-34 (bien qu'il soit indirectement coupable de leur apparition). L'ensemble des mesures proposées par l'institut seulement à la fin de 1943 a permis d'éliminer certains commentaires. Et l'amélioration de la qualité de la production d'acier dans les entreprises de métallurgie ferreuse a permis de réduire la proportion de rebuts de 56,25 % en 1942 à 13,30 % en 1945. Les entreprises n'atteignirent le niveau proche de 100 % qu'à la fin de la guerre.