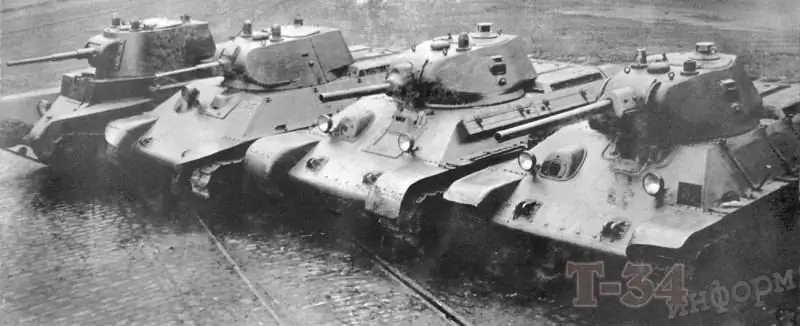
En attendant la guerre
Les problèmes de production de chars en Union soviétique dans les années 1920 et 1930, associés principalement à l'indisponibilité de l'industrie, s'expliquaient en partie par le retard de l'industrie blindée. Au début de 1932, seules deux des quatre entreprises prévues pouvaient fondre et rouler des armures. Il s'agissait des usines d'Izhora et de Marioupol. En raison des exigences excessivement élevées de vitesse de production (c'était un signe de l'époque), ces usines étaient chroniquement en retard sur les plans. Ainsi, dans l'une des plus anciennes entreprises du pays, l'usine d'Izhora dans la ville de Kolpino, en un an, ils n'ont pu maîtriser que 38% du plan, et à Marioupol à l'usine d'Ilyich - seulement un quart. Cela était en grande partie dû à la production d'armures hétérogènes cimentées complexes, qu'ils savaient fabriquer dans notre pays depuis 1910. Un type d'armure similaire était nécessaire pour résister aux projectiles et aux balles à tête pointue, ce que la dureté moyenne et faible homogène habituelle ne fournissait pas. A cette époque, les armures cimentées étaient divisées en deux qualités: à basse température, cimentées unilatéralement avec une face arrière suffisamment dure et, dans la deuxième version, avec une face arrière moyennement dure. Fondamentalement, pour la production de ces "sandwichs", il fallait de l'acier au chrome-molybdène et au chrome-nickel-molybdène, ce qui nécessitait de rares additifs de ferroalliage importés. Le principal élément d'alliage de ces aciers était le chrome (1, 5-2, 5 %), qui favorise une carburation intensive et l'obtention d'une dureté élevée de la couche cimentée après trempe. Une tentative d'utiliser du manganèse et du silicium nationaux pour l'acier de cémentation au lieu du chrome importé a donné un résultat négatif. Lorsqu'il est allié au manganèse, il a été révélé que l'acier est sujet à la croissance des grains à la température de cémentation (920 à 950 degrés Celsius), en particulier avec de longues expositions nécessaires pour une cémentation à grande profondeur. La correction de la couche cémentée surchauffée lors de la cémentation présentait des difficultés importantes et était associée à la nécessité d'appliquer une recristallisation multiple, ce qui provoquait une décarburation importante de la couche cimentée et des fils conducteurs, et était également économiquement non rentable. Néanmoins, jusqu'au début des années 30, le blindage cimenté était utilisé à la fois dans l'aviation et dans la construction de chars. Dans les avions, des plaques de blindage jusqu'à 13 mm d'épaisseur étaient cimentées, comme des blindages de char jusqu'à 30 mm. Il y avait également des développements de blindage cimenté résistant aux balles de 20 mm, qui n'allaient pas au-delà du développement expérimental. Une telle armure devait absolument être massive, ce qui ne nécessitait que des ressources gigantesques pour le développement de la production.
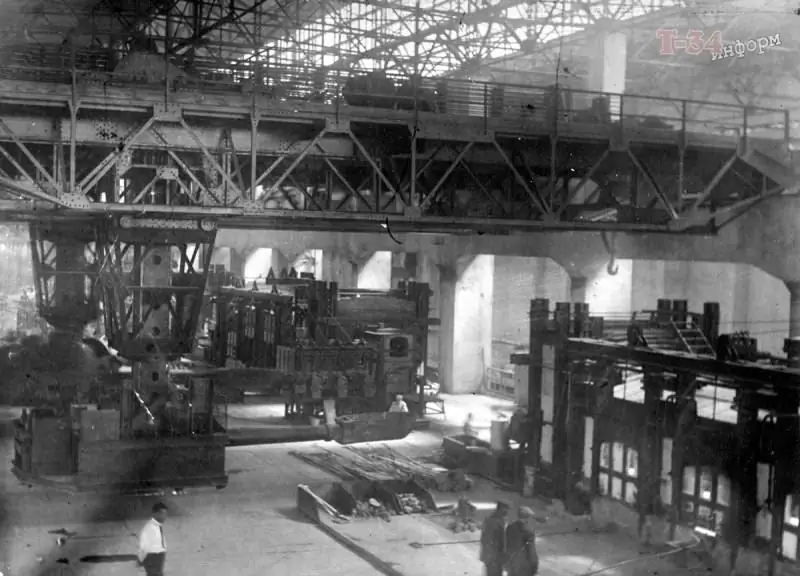
Malgré de telles difficultés avec la production de blindage cimenté, la coque du char T-28 en était presque entièrement constituée. Mais progressivement, l'industrie nationale a abandonné les technologies de cimentation des plaques de blindage, en grande partie en raison des rejets extrêmement élevés. Compte tenu des plans de production exigés par le gouvernement et les commissariats populaires spécialisés, cela n'avait rien d'étonnant. L'usine d'Izhora a été la première à passer à la nouvelle armure, après avoir maîtrisé la fusion de l'armure de chrome-silice-manganèse très dur "PI". A Marioupol, ils maîtrisaient le manganèse hétérogène "MI". Le pays est progressivement passé à sa propre expérience dans la conception d'armures. Jusqu'alors, il reposait sur des technologies étrangères (principalement britanniques). Le refus de cimenter l'armure a rendu les feuilles plus épaisses avec la même résistance d'armure. Ainsi, au lieu d'un blindage cimenté de 10 et 13 mm, la coque du T-26 a dû être soudée à partir de tôles d'acier Izhora "PI" de 15 mm. Dans ce cas, le char pesait 800 kilogrammes. Il convient de noter que la transition de l'acier cimenté coûteux à des technologies de blindage homogènes relativement peu coûteuses s'est avérée très utile en temps de guerre. Si cela ne s'était pas produit dans les années d'avant-guerre, le développement de la fonte et du laminage de types de blindages coûteux aurait été peu probable compte tenu de l'évacuation des entreprises en 1941-1942.
Depuis les années d'avant-guerre, le rôle principal dans la recherche et la recherche de nouveaux types d'armures a été joué par le "Armor Institute" TsNII-48, qui est maintenant connu sous le nom de NRC "Kurchatov Institute" - TsNII KM "Prometheus". L'équipe d'ingénieurs et de scientifiques TsNII-48 a déterminé les principales orientations de l'industrie nationale des blindages. Au cours de la dernière décennie avant la guerre, l'apparition à l'étranger d'artillerie perforante de calibres de 20 à 50 mm est devenue un sérieux défi. Cela a obligé les développeurs à rechercher de nouvelles recettes pour l'armure de réservoir de cuisson.
Naissance de 8C
Remplacez le blindage cimenté résistant aux projectiles à tête pointue et aux balles sur les véhicules blindés légers et moyens uniquement par de l'acier à haute dureté. Et cela a été maîtrisé avec succès par les métallurgistes nationaux. Coques de véhicules blindés BA-10, chars légers T-60 (épaisseur de blindage 15 mm, frontal - 35 mm), T-26 (épaisseur de blindage 15 mm) et, bien sûr, chars moyens T-34 (épaisseur de blindage 45 mm). Les Allemands avaient également une priorité pour les blindages de haute dureté. En fait, toutes les armures (en commençant par les casques d'infanterie et en terminant par les structures de protection de l'aviation) sont finalement devenues d'une dureté élevée, remplaçant celle cimentée. Peut-être que seuls les KV lourds pouvaient se permettre un blindage de dureté moyenne, mais cela devait être payé avec la plus grande épaisseur des tôles et la masse finale du char.
L'acier blindé 8C, base de la défense anti-canon du char T-34, est devenu une véritable couronne de créativité des métallurgistes nationaux. Il convient de noter que la production d'armures 8C dans les années d'avant-guerre et pendant la Grande Guerre patriotique était deux processus très différents. Même pour l'industrie d'avant-guerre de l'Union soviétique, la production de 8C était un processus complexe et coûteux. Ils n'ont réussi à le maîtriser qu'à Marioupol. La composition chimique du 8C: C - 0,22-0,28%, Mn - 1,0-1,5%, Si - 1,1-1,6%, Cr - 0,7-1,0%, Ni - 1,0-1,5%, Mo - 0,15-0,25%, P - moins de 0,035% et S - moins de 0,03 %. Pour la fusion, des fours à foyer ouvert d'une capacité allant jusqu'à 180 tonnes étaient nécessaires, versant les futures armures dans des moules relativement petits de 7, 4 tonnes chacun. La désoxydation de l'alliage liquide (élimination de l'excès d'oxygène) dans le four a été réalisée selon un procédé diffus coûteux utilisant du carbone ou du silicium. Le lingot fini a été sorti du moule et laminé, suivi d'un refroidissement lent. À l'avenir, la future armure était à nouveau chauffée à 650-680 degrés et refroidie à l'air: c'était des vacances élevées, conçues pour donner à l'acier une plasticité et réduire sa fragilité. Ce n'est qu'après cela qu'il a été possible de soumettre les tôles d'acier à un traitement mécanique, car le durcissement ultérieur et le faible revenu à 250 degrés les ont rendus trop durs. En fait, après le durcissement final au 8C, il était difficile de faire autre chose que de souder le corps. Mais là aussi, il y avait des difficultés fondamentales. Contraintes internes de soudage importantes dues à la faible ductilité du métal de l'armure 8C, notamment avec sa faible qualité, conduisant à la formation de fissures, qui s'accentuent souvent avec le temps. Des fissures autour des coutures peuvent se former même 100 jours après la fabrication du réservoir. Cela est devenu un véritable fléau de la construction de chars de l'Union soviétique pendant la guerre. Et dans la période d'avant-guerre, le moyen le plus efficace d'empêcher la formation de fissures lors du soudage d'une armure 8C était l'utilisation d'un chauffage local préliminaire de la zone de soudage à une température de 250-280 degrés. À cette fin, TsNII-48 a développé des inducteurs spéciaux.
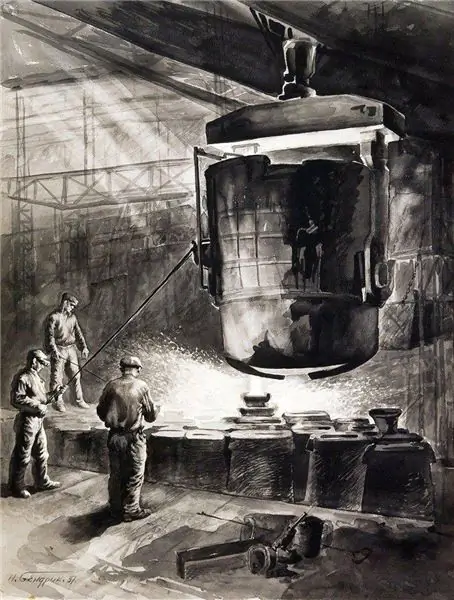
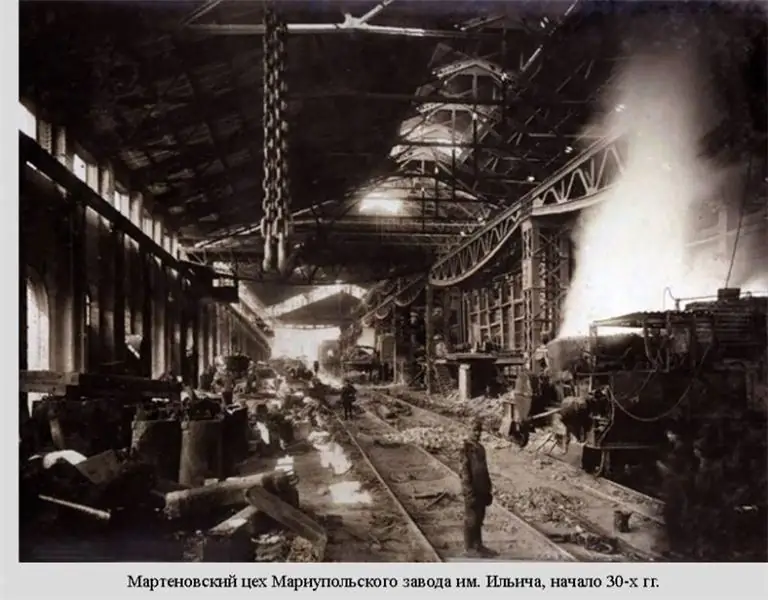
Le 8C n'était pas la seule nuance d'acier pour le blindage T-34. Lorsqu'il y avait une opportunité, il était échangé contre d'autres variétés moins chères. Dans la période d'avant-guerre, TsNII-48 a développé une armure structurelle 2P, dont la production a permis d'économiser de l'énergie de manière significative et de simplifier le laminage des tôles. La composition chimique de 2P: C - 0,23-0,29%, Mn - 1,2-1,6%, Si - 1,2-1,6%, Cr - moins de 0,3%, Ni - moins de 0,5%, Mo - 0,15-0,25%, P - moins de 0,035% et S - moins de 0,03%. Comme vous pouvez le voir, les principales économies ont été réalisées dans le nickel et le chrome rares. Dans le même temps, les tolérances très strictes pour la présence de phosphore et de soufre sont restées inchangées pour le 2P, ce qui, bien sûr, était difficile à atteindre, surtout en temps de guerre. Malgré toutes les simplifications, le blindage structurel en acier 2P subissait toujours un traitement thermique - trempe et revenu élevé, qui chargeait considérablement l'équipement thermique nécessaire au traitement thermique des parties de blindage les plus critiques des réservoirs, et augmentait également considérablement le cycle de production. Pendant la guerre, les spécialistes du TsNII-48 ont pu développer des technologies permettant d'obtenir des aciers similaires, dont la production a libéré des ressources pour le blindage principal 8C.